Airbus partners with Accenture for productivity efficiency on A330 assembly line
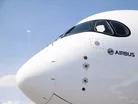
The professional service firm, Accenture, has deployed its remote-support offering on the assembly line of Airbus’ A330 airliner.
The France-based aircraft manufacturer has implemented the remote-support offering to improve productivity and reduce costs.
Accenture’s smartphone application uses video technology that allows mobile operators in the aircraft and those in the office to communicate.
The fast, high-quality communication can ensure those in the office guide mobile operators to resolve issues in the aircraft quickly, reducing assembly costs through time efficient decision-making less non-productive time.
SEE ALSO:
Prior to these technology developments, to resolves aircraft issues, mobile operators would have to send emails, photos, or other forms of media to make workers in the office aware.
96% of SightCall video technology users reported that the remote-support offering reduced time to solve issues.
The average time to manage aircraft issues with the Accenture technology has been reduced by 60 minutes.
“We look forward to continuing to innovate and deliver new solutions that help aerospace manufacturers improve productivity and reduce costs,” reported Julio Juan Prieto, Managing Director for Aerospace & Defense practice at Aerospace.
- Manufacturing Unwrapped: Nasa & Airbus 3D Print in SpaceTechnology
- Accenture: How to Make The Industrial Buying Process GreatProduction & Operations
- Airbus Plans to Expand Groundbreaking Industrial 5G NetworkTechnology
- How Supply Chain Innovation can Stop Unplanned DowntimeProcurement & Supply Chain