How to make your maintenance suppy chain more effective using data
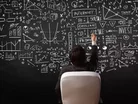
Dan Somers of Warwick Analytics (www.warwickanalytics.com) talks to Manufacturing Global about how software can now accurately automate the maintenance and warranty classification process and what this means for engineers, managers and mechanics in the industry.
Keeping the right equipment and parts on site to repair and maintain production equipment is a balancing act. You need to keep manufacturing running but you don’t want to tie up huge amounts of capital in equipment and parts that might not be used for months, years or maybe never. Alternatively, living with plant equipment that has unpredictable downtime can cost a significant amount through lost production availability and unplanned maintenance.
Effective Maintenance, Repair & Overhaul “MRO” is about planning, managing, coordinating service and deliveries from a wide variety of suppliers, having real-time visibility of where each part is located, and making sure the resource-intensive process is as cost-effective as it can be.
Effective MRO relies upon accurate and timely information. In particular, knowing the precise issues and what actions have been carried out is critical to predicting and preventing these issues in the future.
Analysis of maintenance & repair unstructured ‘free text’ data currently needs considerable human input by experienced personnel throughout the analysis cycle to ensure that the information is consistent and accurate. Otherwise a company might not know how many similar incidents occurred and whether they are rising, or have a common root cause. The information might be buried in text and using different words, short-hand and semantics to describe a similar incident. Conversely similar issues might turn out to be distinct based on subtle differences in the descriptions.
Text mining tools can spot keywords but currently only human beings provide the final insight that converts raw data into knowledge. Typically this comes from a more holistic interpretation of the incident, comparing unstructured data with the structured and inferable information from disparate data sources or prior knowledge.
The challenge with this current approach is that human beings can act subjectively, make mistakes and their individual capacity isn’t quick or scalable.
Further, any analysis across disparate databases (e.g. trying to combine diagnostic or manufacturing data) leads to many more technical challenges.
Given these pressures, the MRO supply chain has long been ripe for efficiency and improvements.
There has been successful adoption of new techniques and technology across the sector which has highlighted the possible savings that can be achieved.
In 2014, PwC surveyed more than 100 manufacturing and maintenance companies and found that the use of 3D printing, otherwise known as ‘additive engineering’ to increase spare part availability at point of use, cut costs by reducing waste, and decrease labour content. Most of the companies had already reported significant gains in speed and flexibility relating to product development and customisation. The research went on to say that if just 50 percent of spare parts were produced using this technology there would be cost savings of $3.4 billion.
There are also technologies already being used in transportation (where MRO issues are often more acute). Key technologies picked out by Espen Olsen, European director for aerospace at IFS, as potentially having the biggest impact on MRO applicable to both manufacturing and aerospace include mobile technology (engineers equipped with mobile apps to access relevant information at the time of need) and wearable technologies. Japan Airlines already use Google Glass in their maintenance process. The glasses are worn by engineers working around the aircraft on the tarmac. Images of the aircraft are sent to maintenance specialists for assessment who then feed any issues they see back to the engineer on the ground.
One other technology trend that Espen highlighted was that Big Data holds the key to predicting the future. He says: “In MRO, there's huge potential of using the secrets of data to enable everything from predictive analytics to greater inventory optimisation, better monitoring of usage patterns and the essential tracking and analysing the health of equipment in real-time. But so far there has been little in the way of answers for its key uses, or more importantly, the means of identifying which data is useful, and which is not.
“In 2015 the commercial sector will and must tackle big data head on. In particular I think in using big data for predictive analysis. By providing key data around asset failures, this can then be integrated into logistics systems to help inform and improve future designs, optimise usage and lower the total lifecycle cost.”
This prediction is now reached realisation with the introduction of new software that can automate the process of MRO classification.
AMROC is a new product from Warwick Analytics and is one possible approach. It automatically transforms disparate and unstructured maintenance data. It has been shown to dramatically improve the insight available for aerospace operators, maintainers and manufacturers and is now being used by manufacturers and energy companies on their plant MRO.
So how does it work? As we know the analysis of maintenance & repair ‘free text’ data currently needs considerable human input by experienced personnel throughout the analysis cycle to ensure that the information is consistent and accurate. However, AMROC converts that unstructured and semi-structured data including text, logs and diagnostics into structured data for classification. The software automatically mines for thousands of different possible patterns from the structured and unstructured data, and then structures and classifies the issues, based on these patterns, in near-real-time, vastly reducing the time taken to manually classify and quantify free-text maintenance & repair data. The data do not need to be cleaned, and therefore are not subjected to assumptions and error.
With new IT technologies like AMROC , MRO costs in transportation and manufacturing are set to decline but it’s not just the large players and OEMs that need to be innovative. Companies at the top of the supply chain are asking their suppliers to also improve their productivity when it comes to MRO.
In conclusion, there are new technologies out there which promise to help improve MRO by finding information from data, and using that to understand and predict issues. They will never be able to replace an experienced human being, but they will be able to dramatically help that person to gain rich, accurate and timely insight and make the whole MRO supply chain more productive.
Visit www.warwickanalytics.com for more information.