The importance of business agility in times of uncertainty
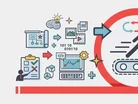
For modern manufacturing companies, successfully navigating the increasingly competitive and global marketplace relies on finding a balance between rigor and agility in planning. While complex, highly structured planning has always been part of manufacturers’ business operations, many have struggled to implement the necessary infrastructure to allow for quick course correction considering unforeseen circumstances. This has become clearer as manufacturing businesses grapple with the ongoing pandemic and have seen supply chains change seemingly overnight. The need for agility has never been more important.
As organisations continue to adapt to the changes in the months ahead, the ability to collect, analyse, and report on accurate, up-to-date data and use it to construct forecasts that can guide operations on the ground is key. While achieving this might seem overwhelming with the pace of change we are currently experiencing, it boils down to adopting five practices:
1. Implement a cadence and system that allows businesses to ingest actuals on an automated basis
Many manufacturing organisations continue to carry out their financial planning with the help of traditional spreadsheets. While this might work well for individual back-of-the-envelope analysis, it makes the forecasting processes unnecessarily time-consuming and error-prone. According to the Association of Finance Professionals, finance professionals say they take an average of 77 days to complete an annual budget and 20 more to perform a forecast. It goes without saying that a cycle that is slow might not cut it in the current situation, where quick course-correction is needed on a regular basis.
What finance teams in the manufacturing industry need is the ability to easily adjust drivers in their models to provide an always-on rolling forecast to management, which can use that information guide business-critical decisions. This requires a highly automated, accessible, and adjustable planning infrastructure, that collects and processes the data in the cloud.
2. Establish a single source of critical business data for the entire organisation
For a business plan to be solid over time, everyone within the organisation needs to have access to a single source of up-to-date data. There needs to be complete alignment on the numbers used for analysis. This can be easier said than done, with finance seeing data coming from multiple sources, such as production, inventory, and expenses. While making sense of this data will always require the concerted work of highly skilled finance professionals, their work is made harder when disconnected spreadsheets are used, as some decisions will almost certainly be delayed or based on old data.
To ensure there is no debate about what data is the most up-to-date and accurate, manufacturing organisations will need to move away from spreadsheets and look into specialised tools that automatically incorporate data to drive standard cost or inventory models in real-time.
3. Work with multiple holistic ‘what-if’ scenarios
It is important for businesses to be agile. For planning, this means being able to model multiple, holistic, ‘what-if’ scenarios that can be used to make sure the organisation is prepared for even the most unlikely situations. For example, finance teams need to be able to determine what the cash impact will be in Q4 due to a longer production cycle, or what happens over time if plant downtime is increased or decreased.
To achieve this, finance professionals need the flexibility to rapidly spin up multiple scenarios to explore the impact and trade-offs of various decisions and settle on a course of action. This requires driver-based models that span the full gamut of operational metrics such as asset utilisation, cycle time, and direct and indirect costs, to name a few. This kind of complex scenario planning can be fast and easy but requires a robust IT infrastructure that can easily be upscaled and accessed through the cloud.
4. Provide stakeholders with real-time, self-service access to the data they need
Research shows that nearly three out of four CFOs identify collaboration as a top initiative. That said, it is often the case that, when plans are locked up on a financial planning analyst’s hard drive, plant managers have difficulty accessing the KPIs for which they are responsible. This creates a lack of ownership and accountability for the results. Instead of seeing business data as their own, it becomes “finance’s number”.
Critical KPI data, whether it is loss rates on the plant floor or the number of customer complaints, needs to be in the hands of relevant decision-makers. As ad hoc questions pop up across the organisation, answering them should not need to involve multiday, one-off exercises for the finance team.
Ensuring that stakeholders take on plans as their own can be difficult, however it is important to make sure the planning system is easy enough for those outside of finance to use if necessary. Intuitive dashboards can achieve this, as plant managers and others can easily review KPIs immediately and see the impact of their decisions in real time without involving the finance team.
5. Combine ground up assumptions with top down models to identify gaps in planning
When it comes to building models, finance teams are often left to choose between taking a top-down approach, which starts from a growth rate to make margin and ratio assumptions, or a bottom-up one, involving a detailed personnel roster and stock-keeping unit (SKU) level costs. Guidance from executives and board members tends to take the top-down perspective, wanting a plan with production targets, growth rates, margin goals, etc. But building an operational plan that can be executed efficiently requires detailed, ground-up assumptions. This can cause a stalemate that hinders agility, leading to planning cycles slowing down.
In these uncertain times, when manufacturers are facing immense pressures from all directions, combining high-level, top-down growth and margin-based models with detailed bottom-up operational models in a single platform is key. Subsequently, gaps can be more easily identified, and differences reconciled
There is no way to predict, or control, how the current economic situation will develop, however these five practices will help manufacturers prepare for every possible scenario that lies ahead—and are agile enough to course-correct in light of further, inevitable, change.
For more information on manufacturing topics - please take a look at the latest edition of Manufacturing Global.