Managing the R&D conundrum
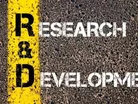
Sometimes, it just takes a small innovation to dramatically change the market. For example, how many of us had ever heard of Saltwater Breweries before last month? The company isn’t a household name in many countries, yet gained headlines across the world with a delightfully creative solution to a major global issue by bringing out edible six-pack plastics. It addresses an issue so many of us relate to - guilt over discarding non-biodegradable plastics, especially when we hear about the damage they can cause to fish and animals. Saltwater’s invention is a great example of how changing a manufacturing chemical or process to be greener, more efficient or more durable can be a key differentiator for a company and a potential game changer for the market.
The globalization of manufacturing has radically increased competition with almost every firm now facing fierce international competition. Therefore, leveraging innovations like edible or even self-healing plastics can help a company stand out in a crowded market. Too many of these opportunities, however, are being squandered as firms waste R&D money on projects which have already been explored by others. In order to maximize the impact of an R&D budget, firms need to make sure they are constantly aware of the latest processes, products and solutions that are coming out and targeting research accordingly.
The cost of R&D
R&D is an incredibly expensive endeavor. Eurostat calculated that, in 2013 alone, the Eurozone spent €272bn euros on R&D. This figure is up nearly 45% compared to 2003. The worldwide automotive and customer electronics sectors spend over $13bn on R&D by themselves. Moreover, as the market continues to globalize, the cost of R&D is only set to rise. If investment continues at the current rate, by 2023 the EU-28 countries will be spending nearly €400bn euros on R&D.
This rate of increase in R&D spending is unsustainable in the long-term, exacerbated by the fact that much of this money is wasted as companies investigate dead-end paths or attempt experiments that have already been previously trialed.
The risks of falling behind
Yet, despite the vast sums, businesses cannot afford to fall behind in the technology stakes – what was cutting edge two years ago is old technology now. Manufacturers are under constant pressure to innovate since the customer experience is always measured against the latest breakthrough. Products like Gorilla Glass were luxuries five years ago, with only one in five mobile handsets using it. Now we have Gorilla Glass 4 and Ford announced this year it will be used for windshields in its cars. What was once new is now standard.
These examples demonstrate how much attention manufacturers must pay to chemistry and chemical innovation in particular. To stay ahead of the competition, researchers need access to reliable, accurate and up to date technical information, not only to speed innovation but to reduce the risk of safety and toxicity issues.
The need for technical insight
To successfully navigate the necessary costs of R&D in a global market, firms must avoid replicating existing work and target funding at the most promising lines of research or identify whitespace areas to explore. It is about finding the continuous incremental improvements that can be made, whether those innovations come from inside or outside the company. Particularly in manufacturing and chemical engineering sectors, R&D may not result in a wholesale reinvention of a product. Yet the discoveries and data to support incremental innovation and product improvement can make a crucial difference to manufacturers’ bottom lines.
Forbes has estimated that 250,000 new products are launched a year, along with 2,000 new chemicals entering the market. The speed of innovation has become a breathless race in which all businesses are running to keep up. In order to keep pace, manufacturers need to have access to deep technical databases to gain cutting-edge insights into which R&D projects to prioritize and which are less likely to yield game-changing results.
Christina Välimäki is Sr. Director, Chemicals Industry at Elsevier
Follow @ManufacturingGL and @NellWalkerMG
- Creating a 'Greener' Approach to Christmas Tree ProductionSustainability & ESG
- Roland Berger, the Automotive Sector and Plastic CircularitySustainability & ESG
- Unilever: Masters at Product & Material InnovationSmart Manufacturing
- Hitachi Energy Plans To Invest Billions In Manufacturing R&DSustainability & ESG