Roland Berger, the Automotive Sector and Plastic Circularity
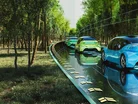
In the 1960s and 70s, plastic was a modern wonder. Soon after it became common - then ubiquitous - with single-use plastic appearing everywhere.
Over generations it has migrated from homes, workplaces and schools into landfills, roadsides and rivers, creating serious environmental hazards.
Today about 36% of the world’s plastic pollution comes from the packaging sector in the form of single-use plastics.
Confronting the sustainability problem of plastic must start with its source - manufacturing.
By 2040, plastic manufacturing and processing could consume as much as 20% of global oil production and use up 15% of the annual carbon emissions budget.
Plastic waste is set to triple by 2060.
Efforts are underway to address this problem across manufacturing, including in the automotive sector.
The EU has mandated that 25% of automotive plastics must by 2030 be made from post-consumer recyclates.
A quarter must also be made from closed-loop, end-of-life vehicle treatment.
Meeting these requirements is essential from both a regulatory and business perspective.
Consumers have made their desire for sustainability clear and it does not stop with clothes, packaging and food products.
Green automation is the future, a future which with growing EV investment is revving into gear.
With this in mind, the transition away from plastics is a no-brainer for the sector. We’ve identified the problem and here is the solution!
But unfortunately, like many things in life, it isn’t quite as easy as that.
The (plastic) bottleneck: recycling
The likelihood of the automotive sector achieving the goal laid out by the EU, as of now, is not particularly high. Less than 5% of automotive plastics are post-consumer recyclates and only a small share of these are then used in manufacturing.
Not to mention the limited lack of facilities capable of recycling EV components.
The root cause of this is the difficulty of recycling plastic polymers, which come in a myriad of different types and forms.
Some polymers like PET/PETE, HDPE and LDPE have a high level of chemical and mechanical recyclability - but the majority do not.
- Incomplete waste collection and sorting
- Limited supply chain efficiency
- Improvable quality from ELV treatment
- Players pending operationalisation
Common polymers used in automotive manufacturing like PUR, PC and Nylon only have a medium level of chemical recyclability and respond poorly to mechanical recycling.
Other polymers like PS, PP and PVC lie somewhere in between.
This range of responses creates significant problems when we consider that polymers are often combined to achieve desired textures, durability and performance.
With the challenges surrounding plastics, many automotive manufacturers seek expert consultancy to guide their approach.
Many turn to renowned experts like Roland Berger, who have a wealth of advice on how automotive manufacturers can strategically approach plastic circularity.
Roland Berger: Enhancing automotive sustainability
Roland Berger is committed to helping automotive manufacturers achieve their sustainability goals and enhance their plastic circularity.
The consultancy applies the ESG framework to all its corporate strategy and actions, taking a holistic approach to sustainable development and helping its clients successfully embrace the eco-transition.
"At Roland Berger, we believe we carry a special responsibility," says Stefan Schaible, Global Managing Partner, Roland Berger.
"We consider it our duty to have a measurable impact on the communities we work and live in. In the past two years, our sustainability-related project portfolio grew fivefold. "
In 2021, Roland Berger presented its ‘Sustainability Award In Automotive’ celebrating brands such as Audi, Polestar, Dana Incorporated and Mercedes-Benz.
Roland Berger's 2022 report ‘The Plastic Balancing Act: driving the Transition and seizing its Opportunities’ takes a three-pronged approach to the challenges of plastic, pinpointing an optimistic and realistic view of the future of plastic circularity.
"There is no ‘silver bullet’ for plastics circularity," says Erwin Douma, Senior Partner, Roland Berger.
"Players need to act now and define their pathway and technology line-up to enable circularity and create opportunities."
The report analyses EU plastic ambitions in targets laid out in the 2020s and explores the big sustainability challenges for plastic producers which include waste disposal and the scalability of alternatives.
The report provides six essential pillars for plastic manufacturers to use to ascertain their circular pathways and work towards establishing a full-scale plastics loop.
These pillars are asset bases, product design, the value chain, material flows, the business model and technology, all of which must work in harmony to support a successful transition away from plastics.
These pillars also apply to automotive manufacturers, who perhaps face some of the greatest challenges- and opportunities- when it comes to plastics.
******
Make sure you check out the latest edition of Manufacturing Digital and also sign up to our global conference series - Procurement & Supply Chain 2024 & Sustainability LIVE 2024
******
Manufacturing Digital is a BizClik brand.
- The University Manufacturing Circuit Boards from LeavesSustainability & ESG
- Tata & JLR: Supercharging Next Gen Automotive ConnectivityTechnology
- Schneider Electric's Commitment to Sustainable ManufacturingSustainability & ESG
- Lenovo & Saudi Alat Building Green Manufacturing FacilitySustainability & ESG