Reducing absence, increasing performance
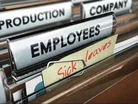
After twenty years of decreasing workplace absence, the last five years have seen a 15 percent rise across the UK workforce. It is the iceberg issue that is causing huge losses in workforce productivity. The issue is far bigger than most organisations realise (as much as 30 percent) and is costing the UK economy billions of pounds every year, but the solutions may be more straightforward than you think.
The rapid rise in absence issues has caught a wide-range of employers unawares. We have an ageing workforce, with FirstCare statistics showing a 132 percent increase in those working past 60 in the last seven years, with this demographic much more likely to suffer musculoskeletal injuries. Alongside this, employees in their 30s and 40s are increasingly more likely to suffer from mental health issues. This combination has driven the increase in absence and has widespread repercussions across the manufacturing sector.
FirstCare data shows that, the average number of days lost per employee across the UK workforce has increased from seven in 2011 to over eight in 2016 – this 15 percent increase results in hundreds of millions of pounds of additional lost productivity. This increase is being driven by the rise of musculoskeletal and mental health issues, with these two categories making up approximately 40 percent of reported absences each year.
Absence comes at a cost and every day lost directly affects the bottom line of all businesses. In particular, manufacturers may be unable to substitute skilled workers at short notice. For example, the estimated cost of absence across one UK based motor manufacturers production line of skilled employees, is estimated at one million pounds per day. Scheduling can be complicated enough without the added pressures of workplace absence. Identifying absence pressure points can help managers create the appropriate processes and support mechanisms that allow for a productive workforce.
Most companies understand that they are, in part, responsible for the provision of workplace welfare if they are to ensure an effective workforce. Astute employers know that a failure to introduce appropriate support networks will directly affect workplace productivity.
Looking more broadly, the UK is experiencing a rapid rise in mental health issues, with MIND predicting that one in four people will suffer at some point during their lifetime. This is supported by FirstCare data that shows that the average annual days lost caused by poor mental health per employee has more than doubled since 2009 from 0.63 to 1.34 in 2015. It is clear that employers across all industries must do more to support employees. Otherwise the upward trend over the last five years will continue to grow.
Those with severe stress and mental health issues are now likely to take time off without the level of comprehensive care which is required, increasing the total time of absence. As a result, the cost of absence due to mental health conditions is increasing.
However, these costs have the potential to be reduced with straightforward initiatives that can have a significant impact. By implementing simple measures such as conducting back to work interviews as part of a wider range of employee check-ins, data across our manufacturing clients shows that absence rates can be halved.
This often requires an openness and transparency that can be lacking on the production floor. Managers must be willing to speak to their employees face-to-face, providing honest advice and support where needed. Providing early access to support and encouraging a climate of early intervention can reduce the length of workplace absence or prevent them entirely. Employers can also train members of staff to provide services such as mental health first aid or crisis counselling. In the same way that workplaces have a designated first aider, a mental health first aider can help recognise crucial warning signs, provide help, reassurance and offer guidance towards the appropriate support services.
Increased engagement with employee welfare not only provides support for those struggling with poor mental health or stress but can also help identify specific issues within an organisation.
FirstCare data shows that when pressure points are successfully identified simple solutions can be implemented to provide a rapid decline in absence rates. Stansted Airport recently achieved a 58 percent reduction in absence, equivalent to 45,000 hours of overtime annually. This was achieved by working in partnership to identify key challenges and appropriate solutions. FirstCare proposed the appointment of an Attendance Manager, who could spend time identifying key issues across the workforce. Through this system of support, individual managers can take a much more active role in achieving the most productivity from their workforce. This data driven analysis has enabled Stansted to focus on the long term benefits of improving attendance, rather than the short term challenge of managing absence.
While most manufacturers focus on their teams using the right equipment, having the correct training and implementing effective working practices to boost productivity, our data shows that through management of absence it is possible to make rapid improvements to workforce performance. Taking on greater responsibility for absence rates gives manufacturers the power to increase engagement, ensure compliance, drive performance and reduce cost.
David Hope is the CEO of FirstCare, workplace absence management specialists.