Six tips for improving food manufacturing efficiency
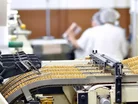
Efficiency is at the heart of all challenges facing food manufacturers. Cutting costs and delivery times boost profits. Take these steps toward improving your plant and enhancing your efficiency.
- Ready your plant for risks
You could lose your entire inventory to a broken refrigerator or chiller unit. Regular maintenance can prevent breakdowns, but you must be ready for inventory losses if a temperature control system stops working. Install backup generators to keep refrigeration units running in blackouts. Like the refrigerators themselves, the generators will also need regular maintenance to ensure they will work when needed.
Aside from keeping up your equipment to prevent failure, you can also invest in business loss insurance. Coverage under business loss policies includes product losses from weather events and power outages. If an unexpected event occurs, you'll be able to get back on your feet faster. Your facility's productivity will improve with the loss recovery from insurance, since the event will not set you back as far as it would if you lacked insurance.
- Become more energy-efficient
Energy-efficiency reduces your operating costs effortlessly. Incorporate natural light into your facility to reduce the number of light fixtures you need. For the ones you do have, select long-lasting LED lightbulbs. LED lights use less power and last years longer than fluorescent or incandescent bulbs.
You spend up to 60% of your energy bill on refrigeration. By making your refrigeration units more efficient, you'll save money. Move any heat-generating equipment away from the refrigerators, because heat sources near a freezer or refrigerator will make the chiller work harder. Lights also generate heat, so avoid incandescent lightbulbs in a refrigeration room. Use LEDs instead, which aren't as sensitive to cold temperatures as fluorescent lights.
- Conserve water
Food production uses more water than many other manufacturing plants. By cutting back on water use, you will save money. You can then reinvest the money you save into making your facility more productive. Conservation measures and recycling water where possible allowed a chicken nugget manufacturer in North Carolina to save $100,000 annually and cut water use by 30%.
Reconsider your facility's cleaning practices, because sanitation uses a lot of water. Invest in equipment such as reuse systems and flow restrictors to reduce the amount of water used for cleaning. Reuse systems take wastewater, treat it and bring it back to the facility for use in nonpotable applications. Flow restrictors cut back on the amount of water wasted during sanitation by reducing the water volume.
- Embrace predictive maintenance
Technology can help make your facility more efficient, even if you don't want to automate everything. Predictive maintenance saves both time and money by telling you when equipment is about to break down. You can plan repairs and upkeep more efficiently and reduce downtime at your facility. When beer brewer New Belgium began using predictive maintenance, it cut downtime by 50%.
To use predictive maintenance, you must install sensors on your equipment and get the software to monitor and analyze information from those sensors. Installing the components needed for predictive maintenance will put your facility on the first steps toward the next industrial revolution, Industry 4.0. This revolution will improve efficiency through data analytics on a broader level than anything seen before.
- Increase use of automation and integration
Automation enhances productivity by reducing errors and increasing uptime. If you have an older facility, you may still rely on human workers for processes that could be automated. Invest in automation equipment to improve efficiency. Train the human workers in other positions around your facility, such as running the machinery, so they can keep their jobs.
Though most food manufacturing facilities use automation for many processes, many sections remain islands of production. Integrating your automated equipment boosts productivity. For instance, if packaging experiences a slowdown, it can send a message to the other equipment in the facility to slow their production to prevent a backlog. This communication between parts of your facility is another aspect of Industry 4.0 that makes your facility more efficient.
- Reduce contamination risk
Recalls waste time and harm productivity. Instead of reacting to recalls, become proactive and prevent contamination in the first place. Food recalls are expensive. Manufacturers in half the food recalls have had to spend $10mn or more. To avoid contamination, only use equipment intended for food and drink manufacturing, which includes everything from cleaning supplies to air compressors.
Watch out for hidden contamination sources. A malfunctioning vehicle or production unit could send microscopic amounts of oil into the air, which can contaminate the food. Dirt is another concern, which is why cleanliness is so vital to the operations of a food manufacturing facility. Hair and germs from people are well-known contaminants and are why food manufacturing facilities require hairnets and face masks. When you control these hidden sources of contamination, you protect your facility's productivity and keep it working at its peak.
A more efficient plant
Food manufacturers have many more factors to consider than other businesses. Though the industry of food and drink manufacturing is complicated, you don't need sophisticated algorithms to improve your efficiency. Take the steps mentioned above to make your plant more productive and improve operations.
By Megan Ray Nichols.