Top four enablers for digital and analytics transformation
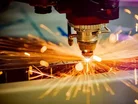
Manufacturing Global takes a look at how the heavy-industry manufacturing sector can make the most of digital and analytical transformation.
Within the heavy-industry manufacturing industry, digital and advanced analytics technology has significant potential to improve operations. In order to unlock this potential on a large scale companies need to harness a systematic approach to successfully identify, develop and roll out solutions that offer the most value.
McKinsey highlights that the best approach to achieve this is subject to the organisation. It will depend on the current digital maturity of an organisation, its goals and the nature and distribution of the opportunities.
However, there are four critical enablers every organisation needs in some form for every digital initiative. Together these enablers comprise an engine to power any heavy manufacturer’s successful digital and analytics transformation.
Talent
Recent advances made in software and hardware, has vastly improved accessibility and usability of new technologies. However, successful application still requires people who understand the capabilities and limitations of digital approaches.
With digital innovation rapidly evolving, digital projects often require new capabilities and new roles. These projects require three core elements in order to be successful:
-
People with expertise in a company’s products and production processes
-
Technology specialists in software development, robotics and automation
-
Digital specialists to run agile projects or design an effective user experience
However, these projects frequently require people’s skills to be able to bridge all three elements:
Access to this talent can be a roadblock for digital projects, with the current wave of digitalisation happening around the world skilled data scientists and technical scientists are in short supply. While external hiring is still a necessity, to fill the capability gap in order to begin digital projects, many are looking to develop in-house skills, not to replace PhD-trained data scientists, but to produce skilled and competent digital practitioners who will be essential for the application of new tools.
Those embarking on large scale digital and analytics transformation, may look to set up a digital academy dedicated to the development of skills across the entire organisation. These in-house academies also make it easier to deliver specific training on a just-in-time basis, which can be applied immediately.
Data
Most heavy-industry manufacturing organisations have the data needed, but the requirement to extract that data and unify large quantities of data in an accessible form is something new.
McKinsey, states that many organisations fear that digital transformation will require a complete rework of their entire existing data infrastructure which is costly, complex and prone to failures. However the company assures that the reality is very different, with modern data platforms or integration systems having the ability to be set up as a new layer, sitting above the existing system, interacting flexibly.
Though some may require additional actions prior to integrating, it is important to remember that to avoid failures and minimise costs, organisations should gradually integrate data that is needed for ongoing projects.
Once the data is understood, organisations need to ensure that they can manage it. This requires the stablishment of governance policies and processes, as well as standardisations.
Something which is frequently underestimated is data quality as a challenge. In order to get the best value from data, organisations need to ensure that they understand the characteristics of the data, having processes to identify and manage missing or erroneous data. Organisations also need a systematic process to identify potential risks and define appropriate mitigation actions and improvements when handling data.
SEE ALSO:
Technology
McKinsey notes that it is common for companies to take a technology first perspective when it comes to digital transformation. In order to be successful and see value from a digital project, organisations in the first instance need to define the problem, access the appropriate data and then integrate the best technological solutions for the problem in order to see the best outcome.
It is also worth noting that not all digital approaches require significant technological upgrades. Many existing manufacturing sites can be tuned or reconfigured to deliver additional value via insights from machine learning systems or other similar technology.
However, more important than a digital tool is an organisation's ability to support the use of the tool, as the use of open-source technology increases. Companies need to be careful to not make their existing functions obsolete due to continuous updates of hte technology.
Technology tools selected by an organisation should reflect its working environment and should be standardised across the operations wherever possible, however McKinsey stresses that this shouldn;t keep organisations from improving their technologies.
“The digital space is fast-moving, with new solutions emerging all the time. Since frontline teams don’t have the time to keep scanning the market, it’s useful to establish a corporate group with responsibility for identifying and evaluating promising technologies. Or to build an ecosystem of collaborative relationships with a select group of technology providers.”
Agility
As organisations look to implement digital and analytic transformation within their operations, many have abandoned the traditional waterfall engineering methodology, replacing it with an agile approach. At first this can be challenging, however an agile approach delivers a more incremental and continuous improvement cycle for lean manufacturing.
However in order to become more agile, organisational structures and ways of working will need to change to accommodate this method.
For more information on manufacturing topics - please take a look at the latest edition of Manufacturing Global.
Follow us on LinkedIn and Twitter.
image source: McKinsey