Bala Amavasai on the rise of Intelligent manufacturing
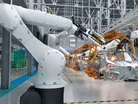
The evolution of the manufacturing sector used to be over decades, yet recent years have forced this evolution to accelerate at an unprecedented rate. Supply chains were hugely disrupted by sharp changes to demand as the world witnessed repeated lockdowns. What we gained from this time of instability, however, was an invaluable lesson - that digital is key. The vast majority (80%) of manufacturers in the UK, for instance, believe industrial digital technologies will be present in their business by 2025.
This pressure to accelerate towards digitalisation is making way for “Intelligent Manufacturing”. This makes use of Internet of Things (IoT), cloud computing, data analytics and machine learning (ML) to optimise how organisations use assets, with a focus on the return of invested capital (ROIC). There are currently four main challenges facing manufacturers. If harnessed correctly, these challenges could also become driving forces of change.
Skills gaps in manufacturing
The rise of Intelligent manufacturing’s use cases is placing high demand on robotics programmers and technicians, cybersecurity experts, digital twin architects, supply network analysts, and people who can leverage data science and ML algorithms. Unfortunately, such skilled individuals are hard to come by, and the industry is facing the challenge of training and retaining staff. For instance, according to the latest ONS figures, in the UK, there were 95,000 manufacturing vacancies in April-June 2022 – almost a 50% year-on-year increase.
Upskilling and reskilling workers in emerging technologies - such as collaborative systems and advanced automation tools - could be a solution to this challenge. Many employees may have existing technical skills that can be bridged into these new use cases. Manufacturers should also tap into open-source technology. Open-source allows organisations to tap into a wider set of skills and expertise, harnessing the power of peer-to-peer learning and alleviating pressures on existing teams.
Strengthening supply chains
The ability to monitor, predict and respond to external factors – including natural disasters, material shortages, and shipping and warehouse constraints – is vital to reduce risk and promote agility. The pandemic only served to highlight the importance of a robust, transparent, and resilient supply chain. This requires up-to-the-minute, end-to-end visibility across all stages of the supply chain. Even today, many manufacturers opt to operate on complex legacy data architectures, like data warehouses. By not switching to a more modern architecture, manufacturers risk information silos forming, preventing easy data access and distribution. Modern architectures, such as a data lakehouse, can prevent the inadvertent sharing of inaccurate datasets that contain duplicated or outdated information.
The answer, therefore, lies in building a strong, modern data foundation that runs off a single, intuitive platform. This removes complexity and enables greater visibility and access to data. A modern architecture makes it easy to gather real-time analysis, by ensuring the timely flow of accurate data, as well as AI and ML use cases. Manufacturers can now make key decisions as and when they receive insights, allowing them to quickly respond to change and face volatility from a far stronger position.
Need for new sources of revenue
The emergence of equipment-as-a-service (EaaS), is changing manufacturers' growth opportunities, as they are no longer limited to new product introductions or expansion into new geographies. While adopting EaaS is not new (Rolls-Royce’s “Power-by-the-Hour” engine subscription model has been around since 1962), it has now emerged as imperative for manufacturers. Why? As the industry is experiencing advances in industrial IoT and a continuing decline in sales and margins, EaaS offers a level of visibility and collaboration that means lower maintenance costs, capital expenditure and human capital management.
Take Rolls-Royce as an example. By using cloud-based models, Rolls-Royce has been able to reduce costs for customers and create new revenue streams. Rolls-Royce has also collected real-time data generated via the creation of digital twins of its engines, and using AI and ML, has been able to help avoid unplanned grounded planes, and reduce millions of pounds from inventory parts costs.
Keeping sustainability in sight
Climate change has also played its part in the growing volatility of global supply chains. For manufacturers, it is no longer just a question of adaptation, but also one of remaining active in reducing the industry’s environmental impact. This spans far beyond the direct emissions of manufacturers to the indirect emissions resulting from activities outside of their control.
Manufacturers must redesign to a circular supply chain in order to achieve greater sustainability - and this is by no means a small task. It all starts with data. Manufacturers must work to improve their collaboration with suppliers and vendors, optimising their production lines and improving customer engagement to extend product life cycles. Collecting data into one place makes it simple to access, as well as storing it for analysis and AI and ML use cases. Manufacturers will gain visibility and intelligence across their entire network, making key decisions to improve efficiency far easier to make. Open-source software also plays a role here as it enables greater data sharing and collaboration across manufacturers, suppliers, and vendors up and down the entire supply chain.
Data and AI have infiltrated almost every industry, and it’s organisations that are choosing to become data and AI driven that are being rewarded. By choosing to leverage data and AI, manufacturers will benefit from a business model that is more flexible, smarter and more competitive than ever before.
- Deloitte: The Key to Optimising Holiday Supply ChainsProcurement & Supply Chain
- McKinsey: How Manufacturers can Ensure Future ProductivityProcurement & Supply Chain
- Carbmee: Helping Maersk & Coca-Cola Curtail Carbon EmissionsSustainability & ESG
- ABB: 2025 Will Be A Balancing Act for Metals ManufacturersProduction & Operations