Breaking down barriers to keep manufacturing connected
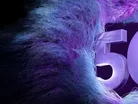
There’s no denying that the manufacturing industry plays a crucial role in the UK’s economy. It provides employment for around 2.6 million people, makes up 44% of total UK exports, and contributes 11% towards Gross Value Added (GVA). Yet, as a sector it’s had to overcome a multitude of challenges presented by socioeconomic turbulence, lockdowns, and the fallout from the global pandemic.
Manufacturers are facing inevitable change at every level of operations. But there is hope. Despite the current uncertainty, 94% of manufacturers are adjusting their businesses in new ways to achieve growth.
One way manufacturers can start to drive positive change is by harnessing the benefits of 5G technology. The application of 5G has the power to drive productivity, efficiency and hyperconnectivity across almost all industries. Integrating this technology will be transformative.
Driving hyperconnectivity
Hyperconnectivity is a term that’s been spoken about for some time now, more commonly associated with the Internet of Things (IoT). 5G is the technology that will make the full vision of this concept a reality. Thus far, the level of connectivity offered by 4G and Wi-Fi networks has not had all the features and functionality needed to facilitate a hyperconnected environment.
Now though, as 5G networks are being built and implemented globally, hyperconnectivity moves from merely a concept to a tangible reality. Universal connectivity paired with Artificial Intelligence means that everything can communicate intelligently. Machines to machines, machines to people and people to people. These interactions are conducted both one to one and one to many.
In addition, 5G provides a level of hyperconnectivity that can support network slicing and splicing. This enables enterprises to create networks customised to specific needs. Networks interacting with public and private networks outside of the enterprise environment, can do so thanks to private 5G networks utilising network slicing and splicing. This optimises performance and reduces costs because only the correct level of connectivity is allocated to each user or device.
Within factory environments this brings about a vast range of benefits, especially at a time when travel and physical interactions are limited. To illustrate, let’s look at supply chains. Typically, these host multiple users and machines all trying to move tracked high-value assets from one place to another. Using a private 5G network, a supply chain can work efficiently - all users and machines talking to one another - and the assets accurately tracked from a remote location in real time. Furthermore, with machines able to alert workers to faults before they become an issue, workplaces will be safer and more reliable.
Ensuring business resilience
Put simply, smart factories are the goal; deploying private 5G networks is how we get there. Smart factories will be able to automate a whole host of activities including real-time linkages to customer demand forecasts, reliable quality, predictable production capacity and lower cost of production. This level of automation brings with it heightened visibility and pace of production, which ultimately drives productivity levels.
Automation can prove particularly useful when navigating lockdown restrictions. 5G, with its low-latency, reliable connectivity and high speeds, enables workers to connect in real-time from remote locations. This means that work and training can continue. For example, using 5G-powered virtual reality, a colleague working from home can connect with an onsite engineer, allowing them to collaborate on tasks without being physically close to one another.
Making this a reality
The benefits of 5G have been touted as revolutionary. But actions speak louder than words and, for organisations to adopt this technology, its value must be clear. We know that organisations are prepared to achieve growth through new avenues. The demand is there, now we need to prove that 5G is the way to facilitate that change. Business use cases need to be developed, tested and deployed.
Encouragingly, we have seen a number of 5G trials looking into the potential benefits of 5G in industrial settings. For example, trials at the Worcestershire 5G Testbed found that 5G could boost productivity by as much as 2%, the equivalent of a £2.6 billion increase when rolled out on a national level. But, in the last year we’ve seen the pace of change accelerate. Now, projects like 5G-ENCODE, part of the UK government’s £200 million 5G Testbeds and Trials Programme, have been set up to demonstrate exactly how 5G can be applied to solve specific problems in an industrial setting.
Led by Zeetta Networks, the 5G-ENCODE project is installing a private 5G network at the National Composites Centre in Bristol. The network will be used to explore new business models and test manufacturing use cases, including augmented reality / virtual reality to support design, manufacturing and training; monitoring and tracking of time sensitive assets and wireless real-time in-process monitoring and analytics.
The results from these projects’ trials will be used to demonstrate how 5G will be applied to solve specific problems in industrial settings. This will be the building block for developing the business model of the future. While projects like 5G-ENCODE may focus on industrial settings, the learnings will be applicable to many others including hospitality, education, and healthcare.
Setting up to win
5G isn’t the answer to all the challenges faced by the manufacturing industry, but it does present an unmissable opportunity to build a hyperconnected future. The opportunities that private 5G networks will bring to businesses within industrial settings, and those further afield, will be truly transformational. Ultimately, it is how technologies like 5G are embraced that will determine who will thrive and who will merely survive. Manufacturers small and large must take it upon themselves to embrace new technologies to create a brighter and stronger future.
For more information on manufacturing topics - please take a look at the latest edition of Manufacturing Global.
- Digitalisation as a Strategy to Attract and Retain WorkersDigital Factory
- Airbus Plans to Expand Groundbreaking Industrial 5G NetworkTechnology
- Assembling the Future: Huawei's New Smart Factory OfferingsSmart Manufacturing
- Tata & Analog Devices Drive Indian Electronics ManufacturingTechnology