Conexiom: Automating for a Touchless Supply Chain
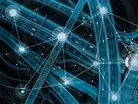
The global supply chain management software market is poised to grow by $9.5 billion between 2020 and 2024. Supply chains are highly complex entities, and this software market covers many management facets. However, whichever form of technological innovation they embrace – be it AI, machine learning, the Internet of Things, or another emerging trend – much of the most exciting software in this space has the same ultimate goal: a touchless supply chain.
What is one of the keys to establishing the touchless supply chain? Automating the processing of core business documents such as purchase orders.
The Dawn of the Touchless Supply Chain
A touchless supply chain is a supply chain that requires little to no human intervention in order to function. Traditionally, supply chains have required a great deal of cognitive brain-power and oversight. At every stage in the chain, human staff members have been right there, executing tasks and overseeing the smooth functioning of the chain. This supply chain oversight has accounted for thousands upon thousands of staff hours.
However, in a touchless supply chain, humans no longer need to be hands-on at any point. Just as automation has been transforming manufacturing processes for decades, it can now automate back office processes. AI processing takes over the vast majority of logistics and internal operations so that everything simply happens.
The resulting benefits are two-sided: One, inevitable human error is eradicated from supply chain operations. Two, staff can ditch repetitive manual tasks, and turn their attention to work high-value work that actually drives revenue.
The Drawbacks of Touch-Heavy Order Processing
Touchless sales order processing plays a key role in the creation of the touchless supply chain. Until enterprises modernize how they process the key business document that is the purchase order, they cannot fully embrace our automated future.
Last year, half of all U.S. manufacturing and distribution sales were processed manually – a total of $8.4 trillion dollars in business-to-business sales. This work was undertaken by customer service representatives (CSRs), who often dedicate a third of every single workday to converting purchase orders into sales orders.
This never-ending manual processing distracts CSRs from providing in-depth customer service, and performing revenue-driving tasks like cross-selling and up-selling. And despite the hours they put in, the overall ROI is poor. There are unavoidable errors. Because CSRs are swamped, purchase-order backlogs sit idle overnight, or require overtime in order to be processed. The unnecessary costs often run as high as $26 per order, and revenue capture grinds to a halt.
Moreover, in the COVID era, this manual approach is more sluggish than ever. Call volumes are higher than ever, at a time when many CSRs are working from home, lacking access to their usual tools.
In short, the way that purchase orders are currently converted into sales orders means that the supply chain is the precise opposite of touchless. Staff spend hundreds of hours on mundane data entry tasks, just to keep the chain moving.
Thankfully, the technology now exists to discard this touch-heavy approach to this portion of the supply chain. Touchless order processing converts the steady stream of purchase orders that manufacturers and distributors receive into a stack of flawless sales orders – all without any human input. With the right SaaS platform, a company can automatically convert emailed purchase orders into sales orders into their ERP system with 100% accuracy.
No CSR has to touch the order. Processing speed is cut from hours to minutes. Onboarding this automation technology takes less than 30 days, and the supply chain is rapidly optimized and accelerated.
As a bonus, when this portion of the supply chain is made touchless, CSRs win back a third of their entire workday. With this new bandwidth, they can over-deliver on customer service, and set enterprises apart from competitors whose CSRs are overwhelmed by manual data entry.
Embracing a Touchless Future
During the pandemic, Sandy Shen, a senior director analyst at Gartner, said that “businesses that can shift technology capacity and investments to digital platforms will mitigate the impact of the outbreak and keep their companies running smoothly now, and over the long term.”
2020 has been a turbulent and difficult year for any enterprise involved in optimizing supply chains. However, moving toward a touchless supply chain is a guaranteed way to future-proof an enterprise against future disruptions. The quicker that companies can remove human intervention from the functioning of their supply chains, the better off they will be. And starting with the core business documents that currently swallow up the most human hours is the sensible and impactful place to begin.