COVID-19: is manufacturing prepared for home working
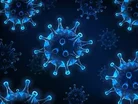
A recent study conducted by Leesman, reveals that the UK manufacturing and industrial engineering industry is not prepared for working from home.
Surveying over 700,000 employees worldwide, 52,240 of those were from the manufacturing and industrial engineering sector. The survey highlighted that 53% of those within the industry have no home working experience.
As the Coronavirus maintains its pandemic status by the World Health Organisation, key players around the world are advising their employees to work from home to attempt to curb the outbreak and protect their workforce. With the UK currently advised to work from home if they can and to definitely stay at home if you are sick, Leesman stresses that with large scale remote working the manufacturing and industrial engineering sectors must prepare itself for a reduction in productivity and innovation.
Across the industry, those that do work from home, 90% typically do so for just one day a week or less, with 0.5% working from home more than four days a week, and 35% of sporadic home workers lacking a dedicated room to work from.
SEE ALSO
The main risks for the manufacturing and industrial engineering industry indicated by Leesman as a result from working from home, include:
-
A reduced sense of community (-21.1%)
-
A reduction in social interactions (-20.4%)
-
A reduction in the transfer of knowledge (-25.8%)
-
A reduction in shared learning (-11.0%)
“Home working will undoubtedly prove pivotal in limiting the impact of the coronavirus crisis. But the data suggests that many employers and employees across the manufacturing and engineering space will be out of their depth should British businesses be forced into lockdown. Our advice is for organisations to quickly quantify where their main obstacles will be and seek support.” commented Tim Oldman, CEO at Leesman.
“We know how and why corporate offices impact employee sentiment but have significantly less understanding of even the short-term impact of dispersing teams to environments designed for living, not working. Industries must brace themselves, but the manufacturing and engineering space must remain one of the most cautious,” added Oldman.
In light of the current actions businesses are having to take in response to the current pandemic, Leesman is mobilising its research tools to enable employers within the private and public sector to support newly remote workers.
Leesman’s index rating covering over 90 indicators in relation to physical, virtual and social workplace infrastructure, highlights how other employees are supported, monitoring key economic indicators including, personal and collective productivity, knowledge transfer and pride.
About Leesman
Established in 1992, Leesman began its operations in order to examine consistently and in depth the affect workplaces have on employees and organisational performance. Leesman prides itself on its intellectual curiosity and determination to challenge common thinking, leading the organisation to where it is today, “the owners of the largest independent database of workplace effectiveness data in the world.”
The team at Leesman have one purpose: “to exceed expectations in everything they do, whether that’s working for a client, a supplier, or each other. We’re here to turn your data into valuable insights so that you can make informed, evidence-based choices when it comes to developing your workplace strategies.”
For more information on manufacturing topics - please take a look at the latest edition of Manufacturing Global.
- MakeUk: Reasons Behind UK Rise in Absences and TurnoverProduction & Operations
- COVID-19: SME manufacturers will ensure UK emerges wiserSmart Manufacturing
- Freshworks: driving maximum business value amidst COVID-19Technology
- COVID-19: VentilatorChallengeUK harnessing big manufacturersSmart Manufacturing