Gartner: 5 best practices for post-COVID innovation
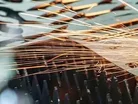
With 50% of factory work expected to be done remotely by 2024, COVID-19 has only increased the investments made by manufacturers into smart manufacturing capabilities.
“But manufacturing operations leaders struggle in an era of continuous disruption to identify, pilot and scale digital technologies and new ways of working,” commented Gartner.
As a result the consultant company closely studied organisations that have “successfully cultivated and delivered innovations across their factories and plants,” identifying five best practices for a systematic approach to delivering innovations post-COVID-19.
The challenges of innovation
“Manufacturers are at a significant crossroads. Factories must not only support organisational endeavors for agility and growth, but they must also manage the ongoing impacts and risks of COVID-19,” noted Gartner.
Challenges for manufacturing operations leaders when it comes to innovation include:
- Innovating at scale, with repeatable performance that enables organisations to move faster
- Generating awareness of successful innovation
- Identifying which sites are ready to adopt, or would benefit from innovative technologies and new ways of working
- Governing innovation management
- Scaling pilots
“Short-term measures to navigate the crisis can only last so long before more strategic, new ways of working and manufacturing need to be established. Put another way, scaling innovation is not episodic; it is cyclical. It requires a deliberate approach to identifying opportunities to innovate, pilot and make successes known, and then to transfer,” added Gartner. “Ultimately, without scaling, innovation will not deliver its full value. It is mission critical for manufacturing operations leaders to overcome the challenges to scaling innovation in an era of continuous disruption.”
Gartner’s Five Best Practices for Post-COVID-19 Innovation
- Aligning smart manufacturing efforts with workplace transformation: Gartner identified that “digitalising manual and offline tasks will not only improve capacity utilisation but also will be a platform for developing new factory worker capabilities.”
- Reduce resistance to change: following a gradual rollout plan, to adapt to social distancing, Gartner also identified the need to “explore and evaluate options with high-impact potential, and focus on the critical paths and core processes first.”
- Align innovation operationalisation with the production system: to ensure site readiness and prioritisation, “in a post-COVID-19 era, lean workforces in particular will need new metrics that integrate with the existing ways factories are managed,” added Gartner.
- Create demand for successful innovation: In addition to the above, Gartner found that companies should “enable project leads to share their direct experiences with peer groups and stakeholders” as well as “Attract a project sponsor from senior leadership to stay apprised and informed of initiatives.”
- Connect Syncornisation with continuous improvements: in doing this, Garntner stated that organisations can “ensure hand-offs, eliminate competition for resources and expose further efficiencies,” as well as identifying that HR could be a good partner to assess new required skills.
Factory Innovation Post-COVID-19: 5 Best Practices for Manufacturing Operations Leaders
For more information on manufacturing topics - please take a look at the latest edition of Manufacturing Global.