GE Digital: optimising manufacturing with smart MES
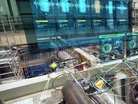
When it comes to manufacturing operations, each step within the production process creates vast quantities of data, including: asset data (real time sensor and measurement results), manufacturing data (real time feed of manufacturing execution events), and enterprise resource planning data (the financial impact to an organisation).
With this information, manufacturers can track, control and document this data within a real-time manufacturing execution system (MES), allowing organisations to optimise production by understanding current conditions on the plant floor, reducing setup time, accurately capturing cost information, increasing machine uptime, reducing waste, and better managing inventories.
As this adoption and acceleration of industry 4.0 technologies continue to revolutionise the manufacturing industry, now more than ever ‘smart solutions’ are vital for effective implementation of these types of innovative technologies. “While not new, lean manufacturing is a goal for many manufacturers in today’s economic climate. Modern lean programs utilise digital technologies to close the loop on continuous improvement and maintain changes through digitised standard work or SOPs. Lean programs of the past would see significant gains, but then the gains would slowly erode. Smart MES helps manufacturers maintain the momentum and drive consistency,” says Joe Gerstl, Director of Digital Product Management at GE Digital, who further explains that maximising overall equipment effectiveness (OEE), improving production scheduling and ensuring product quality by leveraging real-time production data are some of the benefits of lean manufacturing. “Companies can also consolidate and transform manufacturing data across plants for hybrid on-prem/cloud storage, analysis and analytics to optimise processes across assets, ERPs and other manufacturing data,” comments Gerstl.
Other trends Gerstl has seen when it comes to lean manufacturing include manufacturers looking to accelerate their time-to-market and improve just-in-sequence performance on a global scale. “This kind of solution supports lean operations by building the product right the first time, for genealogy and traceability to meet regulatory compliance needs and coordinate across the supply chain,” adds Gerstl. For manufacturers Smart MES is a solution that brings together the digital world with the physical world in a connected enterprise, with this in mind Gerstl explains that “Smart MES allows manufacturers to operate, analyse and optimise their business through insights powered by data integration, the Industrial Internet of Things (IIoT), machine learning, and predictive analytics. This allows holistic end-to-end performance management.”
The challenges, benefits and best strategy for adopting smart MES solutions
While manufacturers are keen to drive this adoption of ‘smart solutions’, plants face a multitude of challenges in implementing any new system or enhancing an existing system. Gerstl highlights that “aging infrastructures, greater productivity challenges and tighter budgets need to be considered as profitability pressures rise. What’s more, with budget restrictions, resources for plant systems are often limited, making it difficult to carry out infrastructure modernisation, expansion, and technology upgrades. Often, due to corporate acquisition and consolidation, manufacturers have several facilities, all with different types of equipment, including various sizes and ages. Companies therefore have no common process for gathering and analysing information, and no internal expertise to integrate systems.”
Another challenge the industry is facing includes a widening talent gap, forcing manufacturers to replace experienced professionals with a younger workforce, “The new generation of workers are experienced with modern technologies such as smartphones but don’t have manufacturing domain expertise or experience with manufacturing software. Manufacturers are losing the institutional knowledge of their more seasoned workforce, so they need to turn this human-based knowledge into a digital asset through the use of work process management systems that capture domain expertise and drive consistent processes across the entire business – all facilities, all systems.”
When faced with these challenges, Gerstl explains that GE Digital would always recommend that a manufacturer finds a partner that has experience in their industry, with their manufacturing challenges, and has a proven product that can address their issues. “By identifying your business outcomes – boosting operational effectiveness, improving performance, driving precision, or ensuring quality – manufacturers can assemble a multi-generational plan that not only addresses these challenges, but doesn’t disrupt the business while implementation and testing are in process,” in order to successfully achieve the benefits that smart MES can provide, including reduced costs, improved quality and faster production.
By aligning resources, energy and efficiency management in manufacturing operations, Gerstl explains that companies can reduce inventory, identify costly production gaps, lower energy and utility waste, and gain valuable insight into throughput and critical manufacturing processes. “Smart MES solutions also capture robust quality data and related traceability information while performing same-time analysis on that data to reduce waste and rework as well as reduce recalls in some industries. And, improved on-time delivery performance, line change agility to respond to supply chain challenges and more successful new product introductions are also facilitated by Smart MES software.”
How GE Digital can help the manufacturing industry implement and maintain smart MES solutions
GE Digital has several services and solutions for those within the manufacturing industry looking to implement and maintain their Smart MES solutions, working with a global ecosystem of experienced services partners. “Together, we start the engagement with Advisory Services that, in collaboration and cooperation with the manufacturer, help plan the implementation that aligns with specific desired business outcomes,” comments Gerstl. “We incorporate best practices used at GE’s own plants, to provide manufacturers with even more insight into opportunities to reduce losses and increase operational efficiency, and our team helps to develop multi-generational plans through our implementation services, to marry existing investments to the right process enhancements and technology.”
Once implemented, GE Digital can help organisations maintain mission critical machines from one of its managed services remote locations around the world using model-based predictive-analytic technology. “Our education services also help to ensure teams are leveraging the solutions with training and certificate programs, while our support services, supports manufacturers to ensure that the solutions operate at the highest efficiency, all while mitigating risks. And, finally, our cyber security services provide industrial-grade security for a wide range of OT network and application topologies.”