The growing shift to smarter supply chains
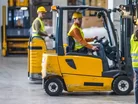
Being just one part of many that form the complexity that is a supply chain, manufacturing can be as simple as buying a small number of raw materials to convert into a product, or it can be a series of components and processes that are interconnected.
Mark Hughes, Vice President (VP) of Epicor (UK&I) explains that “at the heart of it, a smart supply chain is simply one that is as efficient as possible. This means constantly reviewing and understanding where any bottlenecks may exist in your supply chain and working to strengthen the weakest links in order to minimise any potential supply chain shocks. You either eliminate the challenge or move it elsewhere, further up or down the supply chain as required, to make sure you deliver the end result efficiently.”
However, when it comes to being the ‘smartest’ supply chain, “this takes efficiency one step further and is self-organising and self-optimising,” adds Hughes. “For example, it will only introduce components when they’re required —controlling the likes of inventory and storage and prevent the emergence of any bottlenecks by fine tuning the pacing of each stage. In order to achieve this, it’s important to have maximum visibility throughout the whole supply chain — which is where technology can play a beneficial role.”
What is a smart supply chain?
"A smart supply chain is one that draws on data from IoT sensors in the factory, AI and other intelligent technology and data sources to track, monitor and manage goods from manufacturer to retailer. This ability to monitor all processes from design, manufacturing, production and storage of products helps ensure traceability and compliance with the latest standards in quality and hygiene and provides better overall flow, visibility and collaboration across all stages in the value chain.
"The smart supply chain is self-improving and self-optimizing. It can learn from its environment and past actions. It can predict bottlenecks and work around them to avoid disruptions. It can help optimize inventory and make sure that the right quantities are in the right place at the right time. For manufacturers, this can lead to better delivery times and performance, lower costs, efficiency gains, reduced risk and more" - Jim Bureau, CEO of JAGGAER.
So what is driving the shift towards smarter supply chains?
With supply chains being made of several different links - sourcing goods, manufacturing, distribution, shipping and receiving - a vast amount of information and data is being produced. Coupled with a heightened awareness of supply chain risk, the industry is seeing an increase in the adoption of IoT technologies to make supply chains smarter.
“If just one of these links is weakened, it can then have a devastating impact across the whole supply chain. Nobody wants to be the weak link in the chain, so organisations across the whole supply chain are continuously working to mitigate any risk. As a result, this ongoing improvement cycle breeds higher quality supply chains,” says Hughes.
“A great example is the dual sourcing process that takes place in the automotive industry. A car manufacturer may receive 95% of their stock of a single component from one source, but retain 5% of their supply from a different supplier. In the event that something goes wrong with the primary supplier, the manufacturer can then ramp up their order from the secondary. This mitigates risk, reduces the potential for disruption and makes an organisation’s supply chain more robust,” he explains.
Adding to Hughes' comments, both Jim Bureau, CEO of JAGGAER, and Hong Mo Yang, SVP and GM of the Manufacturing Sector at Blue Yonder highlight the part that COVID-19 has played in the shift to smarter supply chains.
“The COVID-19 pandemic has exposed the gaps in our global supply chains and the overall need for greater transparency, efficiency and real-time flow of information. Supply shortages caused major disruptions and placed immense pressure on manufacturers to navigate these challenges as efficiently as possible, especially for critical products like personal protective equipment (PPE), hand sanitiser, media devices and equipment and more,” says Bureau.
“Over the past year, COVID-19 disruptions have affected many industries, but manufacturing has been particularly impacted. Against this backdrop, the transition to smarter supply chains has never been more important: many manufacturers’ legacy supply chain systems simply haven’t been agile enough to react to disruption, let alone anticipate and avoid it. This is driving a shift towards smart supply chains,” adds Yang.
Bureau also adds Industry 4.0 as a driver for smarter supply chains, “Advanced automation is primed to cause large growth for the manufacturing sector over the next few years and the broader supply chain needs to advance at the same rate for the industry to scale the benefits. In addition, the increased demand for mass customisation calls for a smarter, data-driven approach to manage the complexity that comes with producing these tailor-made products while minimising costs, shortages and excess inventory.”
How can manufacturers develop smarter operations in their supply chain?
“For a manufacturer to develop a smart supply chain, it all begins with digitisation,” says Hughes. “As a first step, manufacturers must look inwards and ensure that a comprehensive data-driven picture of their organisation exists. Every factory floor is unique, with unique processes, so there’s no one-size-fits-all approach. With a centralised view, organisations can see clearly which processes might not be driving as much efficiency as they should.
“By digitising operations across the shop floor, manufacturers will be equipped with the data-driven insights they need to ensure each area within the supply chain is as efficient as possible. By sharing these insights with each link, suppliers can react and adjust their supply according to demand, all in real-time. Call it autonomous, or hyperconnected — essentially what we’re talking about is achieving the maximum visibility of information.”
Agreeing with Hughes, Yang adds that it is important to “identify the use-cases and challenges you want to overcome. A pragmatic approach to implementing new technologies to create a smart supply chain will allow companies to scale and deliver greater value. Many companies today are looking to build resilience into their supply chains, and that requires real-time visibility and actionable analytics to navigate supply chain shocks and make data-driven decisions.
“Let’s look at the recent Suez Canal disruption, where a 1,300-foot container ship became stuck sideways in one of the busiest shipping arteries connecting Asia to Europe. With our AI/ML Control Tower, we were able to help our Blue Yonder customers prepare for the early ripple effects by predicting the impact to inventory, production capacity and sales in real-time so they could take corrective actions to mitigate the impact of the disruption.”
With current events such as COVID-19 and the Suez Canal posing severe risks to the supply chain industry, “smart supply chains have never been more important,” says Hughes. “The smarter a supply chain is, the more efficient and resilient it is. There will always be disruptive events that pose a threat to supply chains, both minor and major, but smart supply chains have a better chance of successfully mitigating these risks. True optimisation means dealing with the anomalies, not the norm.
“Ultimately, it’s a case of collecting as much data as possible to increase visibility across the whole supply chain. A smart supply chain will take care of the larger data points and self-optimise to an extent (sudden fluctuations in demand draining stock levels for example). This frees up those on the ground to focus on the small, disruptive anomalies: the flat tyres of the supply chain that can’t be optimised away.
Smart supply chains: the top trends
Jim Bureau, CEO of JAGGAER:
- Agility and better collaboration: the supply chain pressures brought to light by the pandemic have led organisations to crave agility and the ability to quickly respond to change. With the visibility and real-time monitoring the smart supply chain provides, manufacturers and their downstream partners can work together more easily and effectively to solve issues at any point in the supply chain when they arise. This drives efficiency, performance, stronger relationships, and resilience.
- Sustainability: in the broad sense – environmental but also social and economic – has also been an urgent issue, and manufacturing organisations are increasingly becoming more intentional about developing resource-efficient behaviour and really knowing the suppliers with which they work. Driving efficiencies, optimising routes, increasing transparency across the supply base through greater traceability through n-tier suppliers, ensuring compliance, and limiting overproduction, waste, and excess inventory, are just a few of the ways a smart supply chain can further sustainability.
Hong Mo Yang, SVP and GM of the Manufacturing Sector at Blue Yonder:
- Artificial Intelligence (AI)/ Machine Learning (ML): there are many use-cases for AI/ML across the supply chain. From predicting demand and anticipating disruptions, to optimizing transportation routes, resource planning and customer fulfilment strategies, AI/ML is widely implemented to drive efficiencies, automation, and enable greater visibility and integration across the supply chain network.
- Digital twins: to help supply chain leaders make the right decisions across the end-to-end supply chain, a digital twin is critical. By creating a digital representation of the physical supply chain, companies can leverage the digital twin to make local and global decisions, increase situational awareness, and evaluate the impact of various scenarios with confidence. More importantly, organisations can anticipate the impact of decisions on strategic business objectives such as revenue growth, margin control, and customer satisfaction targets.
- Demand for data scientists: as companies continue to invest in new technologies across AI/ML, IoT and robotics, combined with requirements for companies to aggregate higher volumes of data across internal and external resources, the demand for data scientists will grow. Today, data scientists are working to solve many challenges, such as modelling data and building plans to make the supply chain more sustainable, improving response times and agility with greater visibility and control, and automating decision-making processes with AI/ML and big data to enable companies to make smarter and more strategic business decisions.