Overcoming the challenges of Covid-19 with smart factories
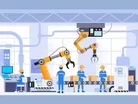
Very few manufacturers have made it through 2020 without significant economic disruption. Many manufacturing organisations have faced significant operational challenges due to the impact of Covid-19, with some suspending production altogether in response to government restrictions or falling demand.
More than 40% of UK manufacturers saw their orders decline between 26% and 50% during the past year.
Yet manufacturers with fully automated production lines have fared better than most. Shanghai-based steel manufacturer Baoshan Iron and Steel, for example, continued operations around the clock through the application of intelligent technologies like remote maintenance operations, big data and artificial intelligence (AI).
By embracing the tenets of Industry 4.0, manufacturers can weave adaptability and resilience into their business framework — and it’s never too late to start.
What makes a smart factory?
Historically, many manufacturers have been lax in their adoption of smart technologies, but this cautious attitude has created a resistance to change that hurts productivity gains in the long run.
The cost of smart technologies may have seemed prohibitive, but now it’s a crucial investment to navigate any potential future upheavals or crises like Covid-19. While human workers are necessary for troubleshooting and supervision, smart factories allow for essentially autonomous production, enabling them to withstand widespread disruption.
Deloitte defines a smart factory as a “fully connected and flexible system—one that can use a constant stream of data from connected operations and production systems to learn and adapt to new demands”. What this means is a shift from many compartmentalised automated processes, to a fully integrated process.
The aggregation and analysis of data provides the fuel to the fire for the next industrial revolution, in which smart factories are key. When everything is quantifiable, manufacturers can gain real-time insights into shop-floor processes, which can, in turn, lead to improvements big and small, including:
- Quality control: using automation to remove some human elements of production can improve quality, efficiency and safety, and can also guard against the kind of worker disruption wrought by a global crisis like Covid-19.
- A more efficient supply chain: machine-driven data collection means a more accurate forecast for demand, reducing both cost and risk across the supply chain.
- Lean inventory, increased profit: the advent of make-to-order increases in efficiency creates room for custom orders that would not otherwise be profitable. Moving from batch-and-queue processing to on-demand part production cuts waste, cost and keeps the inventory lean.
- Faster decision-making: the combination of cloud computing with big data means that every aspect of the supply chain can be more easily visualised and understood. This allows manufacturers to grasp events in real-time, correcting potential issues as they arise.
- Fewer errors: a truly smart factory is one that self-optimises, locating and correcting problems early, at the source. This minimises human time that is often wasted addressing and fixing faults.
Four key pillars of the smart factory
The most ubiquitous technologies in smart factories can operate alone as individual components, or more commonly as cohesive factory-wide systems.
First and foremost is the cloud. While cloud technology remains one of the vaguest terms in the industry, it underpins many of the processes that turn manufacturing systems from legacy to smart.
By switching to a cloud-based model, manufacturers can easily bring together data from all machines and systems across different factories, enabling them to better analyse their processes and increase productivity.
Sitting among the cloud is the Industrial Internet of Things (IIoT): the smart connectivity we all know and love, but bigger. The overarching benefit of IIoT is data collection — a stream of real-time data that enables manufacturers to make quicker and more informed decisions.
Moving beyond the familiar, the cutting edge of remote working is Augmented Reality (AR). AR can support in the event of mechanical breakdown, enabling remote experts to assist workers by overlaying part models in real-time and providing guided instructions.
Finally, robotics is where the rubber hits the road for smart factories. The smartest robots of today are those that can collaboratively work alongside humans to complete production tasks more safely and efficiently.
The Nokia production facility in Oulu, Finland, incorporates all four of these pillars to create of the most fully realised smart factories, operating at 99% automation. With the use of a simulated ‘digital twin’ of the factory, management can test production changes before physical implementation, allowing for outcomes to be studied and risks evaluated.
The factory also makes use of cloud technology and IIoT to monitor processes with mobile robots, all in real-time. This is coordinated on a private wireless network that can reconfigure production lines on the fly, constituting an extremely agile and resilient system.
Taking all this into account, it’s easy to see why Nokia’s facility was designated as an “Advanced Fourth Industrial Revolution Lighthouse” by the World Economic Forum (WEF), of which there are 54.
Looking ahead
The normalcy of 2019 seems a distant memory. Before Covid-19, it was estimated that Industry 4.0 would create $3.7 trillion in value by 2025. That estimate will need to be revised, of course. Now is still the time to invest in a more resilient future, by pursuing smart manufacturing, implementing the technology that makes it possible, and following the example set by the Industry 4.0 Lighthouses.
Widespread, smart automation will not only ensure success in uncertain times, but allow businesses to keep workers healthy and engaged, as the world emerges into an uncharted 2021.
More efficient processes create a far greater depth of manufacturing capability and agility than was thought possible even 10 years ago. Now is the time to be ambitious and start making the change.
For more information on manufacturing topics - please take a look at the latest edition of Manufacturing Global.