Remanufacturing: recycling materials, recouping costs, refining designs
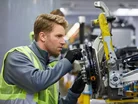
Technological advances in car manufacturing mean our increasingly sophisticated vehicle components have a longer lifespan than they once did. Even when complete automobiles or parts are no longer fit for purpose, they contain valuable elements which hold considerable utility and value. This has opened the door for innovative solutions in automotive manufacturing that repurpose spare parts.
There are two methods for reusing auto parts: remanufacturing and reconditioning. These processes are worlds apart, but they are clouded by misconceptions and are often considered to be interchangeable.
Despite remanufactured car parts having to fulfil much higher criteria for functionality and safety, both manufacturers and consumers are sceptical of the remanufacturing process. This means manufacturers miss an opportunity to diversify their product offering and boost their environmental profile, while consumers often spend more on new parts or opt for reconditioned ones that can be of a lower quality.
But huge benefits can be reaped from remanufacturing. Scepticism stems from unfamiliarity with the process and confusion about how it is distinct from reconditioning. Grasping the fundamental differences between the two processes is crucial to confronting misconceptions and unlocking the value of remanufacturing for the British car industry.
What is reconditioning?
Reconditioning involves stripping and disassembling a vehicle/parts of a vehicle, cleaning the parts, replacing any damaged components and then reassembling them. Although reconditioned parts should be in a satisfactory working condition, the process is unregulated and there is no clear industry benchmarking – resulting in substantial variations in quality and scope for individual subjectivity.
This means consumers do not have any warranty protection or assurances about the longevity of the vehicle parts. What’s more, there is no indication of how the vehicle will perform against original equipment manufacturer (OEM) standards.
Clearly, the reconditioning process has a useful place in the auto sector, but it fails to fulfil the assurance criteria that many consumers will require when buying a car. This is where remanufacturing can help.
What is remanufacturing?
The remanufacturing process restores parts to at least their original performance, but more often than not it actually brings products to a higher standard than a newly manufactured product. How? Because although remanufacturing must bring parts in line with original factory specifications and design, there is also scope for design improvements and the rectification of any “kinks” in the original design.
Because remanufacturers must meet standards established by the British Standards Institution, consumers can be confident that all parts are safe and of a good quality. These high standards mean parts will be as good as new and will reach – or exceed – original performance, reliability and lifespan. To reflect this, remanufactured products come with a new warranty, giving consumers reassurance and protection.
Inevitably, these strict regulations come with an associated cost. To reach these standards, remanufacturing requires specialist equipment and a skilled labour force. This means that there is an increased cost to remanufacture parts, and that they are more expensive for consumers than reconditioned ones, which do not have to adhere to regulations ensuring such high quality.
Four benefits of remanufacturing
Remanufacturing is more expensive than reconditioning, but increased cost is only part of the picture. This negative is outweighed by the four significant benefits of remanufacturing: quality, value, environment and employment.
- Quality Assurance: Unlike reconditioning, which is largely unregulated, remanufacturing ensures parts are restored to at least their original performance in line with original factory specifications. The parts receive a fresh warranty, giving motorists security and peace of mind.
- Value Assurance: Although the cost of equipment and workforce drive up the price of remanufactured parts, their longer lifespan and enhanced quality means they typically represent better value than reconditioned ones. What’s more, because remanufactured parts are recycled from existing parts they are significantly cheaper than newly manufactured ones. These savings in raw material and energy consumption produce an end product which is 40-50 per cent cheaper than a new one – an impressive margin in a highly price-sensitive market.
- Environmental Assurance: Motorists and manufacturers searching for eco-friendly solutions can drastically reduce their environmental impact through remanufacturing; the process salvages around 85 per cent of an engine’s original components. Unsalvageable aluminium, steel and other metal elements can often be recycled in other ways, reducing the amount of waste that ends up in a landfill. Remanufacturing also consumes 80-85 per cent less energy than manufacturing parts from scratch, significantly reducing CO2 emissions.
- Job Assurance: New parts are often manufactured outside the UK, but it’s cost effective for remanufacturing to take place locally. Shifting towards remanufacturing incentivises job creation and the development of skilled expertise in the local economy. Remanufacturing in the UK can also reduce waiting times for new parts, decrease the time, cost and environmental impact that comes with international shipping and increase product availability.
Remanufacturing for the future
Remanufacturing has a lot to offer the British car industry. It re-instils value, quality, economic and performance longevity while reducing environmental impact. It could be the optimum solution for consumers who want to spend less while reducing their carbon footprint and supporting eco-friendly solutions. For manufacturers, it allows them to compete on price and stimulate local economies, boosting levels of skilled employment.
Of course, there are challenges. Consumer knowledge and trust of remanufacturing is low, and there needs to be a concerted effort to educate motorists on the vast difference between remanufactured and reconditioned parts. For manufacturers, there is competition from the Far East, where increasing volumes of low-cost new and remanufactured products are being produced – although these may not comply with industry standards and provide the same level of user confidence. Remanufacturing holds complexities around intellectual property, with the increased complexity of vehicle components and restrictions from original equipment manufacturers requiring skilful navigation of legalities. And with technological innovation accelerating in car manufacturing, remanufacturers need to ensure they keep pace with new developments.
But while these challenges must be taken seriously, they are surmountable with careful planning and consideration, and they should not detract from the opportunity that remanufacturing presents for the UK automotive industry. Simply put, remanufacturing makes sense.
By Ruth Andrew, Principal Associate at Mills & Reeve.