The role of blockchain in manufacturing
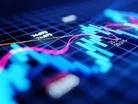
As factories around the world become increasingly interconnected, the influence of blockchain is becoming more prevalent. The Factory of the Future spans across a whole network of machines, parts, products and value chain participants, including machinery providers and logistics companies. Now, more than ever before, manufacturers face the challenge of securely sharing data within and outside factory walls.
To work out the best place for blockchain, a manufacturer must conduct a structured assessment which begins with identifying the company’s current business problems and future needs. Subsequently, it can then explore how it leverages the technology to relieve the factory’s pain points and addresses its needs. Equipped with a strong understanding of the opportunities and challenges it faces, the manufacturer can then choose the most appropriate option from the available technology solutions.
Blockchain can scale transparency and trust through all stages of the industrial value chain, from sourcing raw materials to delivering the finished product. Pain points it could help address, include:
- Supply chain monitoring for greater transparency
- Materials provenance and counterfeit detection
- Engineering design for long-duration, high-complexity products
- Identity management
- Asset tracking
- Quality assurance
- Regulatory compliance
What is blockchain?
Blockchain is essentially, as the name suggests, a chain of blocks. However, instead of a physical chain, there’s digital information (the block) stored in a public database (the chain). When a block stores new data, it is added to the blockchain.
Blockchain-powered solutions can seamlessly aggregate all of the information to deliver significant value for industrial companies and help unlock the full potential of other advanced technologies, such as augmented reality, IoT and 3D printing.
In PwC’s 2018 Global Blockchain Survey, researchers found that 84% of executives across industries said their companies have had some involvement with blockchain, and 15% have live projects. The potential of blockchain-powered solutions to create value by empowering firms to overcome challenging problems is clear. Blockchains can increase transparency throughout supply chains, track the identity and credentials of key personnel and allow for more seamless audit and compliance functionality. Industrial manufacturing firms are already recognised as being out front in developing the technology - with respondents in its survey ranked as the sector second among industries leading the way in blockchain.
Blockchain solutions can create value for industrial organisations in several different ways. However, it doesn’t mean that it is an equally tenable solution for all companies or industrial manufacturing sectors. Through focusing on four key areas in initial blockchain efforts, companies can set themselves on a path towards successful execution. In PwC’s report ‘How can blockchain power industrial manufacturing?’, the four best practices for blockchain solutions were examined.
1. Make the business case
Blockchain can be a powerful tool; however, it’s not indestructible. It’s vital to ensure it is a strategic fit. While there’s a necessity to ensure different parties share and update data, blockchain solutions are particularly effective when time is short, and trust between parties is needed.
2. Build an ecosystem
Bringing together a group of stakeholders to collectively agree on a set of standards that will define the business model is one of the biggest challenges in blockchain. Participants have to decide the rules to take part, how to ensure that costs and benefits are evenly distributed and what risk and control framework can be used.
3. Design deliberately
Much consideration must be given to a blockchain’s design. Will it be permissionless, allowing anyone to initiate and view transactions or permissioned, restricting access to certain parties? PwC’s Global Blockchain Survey shows companies are adopting both of these approaches as well as developing hybrid implementations. Permissioned blockchains are expected to be more appropriate for most enterprise solutions since their owners or governing bodies can structure rules with an eye on privacy and data security.
4. Navigate regulatory uncertainty
Regulators worldwide are still examining the potential responses to the ever-increasing influence of blockchain-led solutions. According to PwC’s 27% of survey respondents, 26% of which are based in the US, believe that regulatory concerns are the number one barrier to blockchain adoption. Instead of waiting for regulators to set the blockchain agenda, organisations that see value in the technology should be proactive. It’s important to engage with regulators, elected officials and industry groups to make the case that blockchain technology can be trusted, sooner rather than later.
Blockchain in manufacturing
There is great potential for blockchain in manufacturing. Increasing visibility across all areas of the process from suppliers, strategic sourcing, procurement and supplier quality to shop floor operations which include machine-level monitoring and service, blockchain can allow for an entirely new manufacturing business model. Supply chains are the basis of all manufacturing businesses, most of which are capable of making use of blockchain’s distributed ledger structure and block-based approach to aggregating value-exchange transactions to improve efficiency. By scaling supplier order accuracy, product quality and track-and-traceability, manufacturers will be able to better hit delivery dates, enhance product quality and ultimately sell more.
Richard Waterhouse, Chief Strategy Officer, NBS, recognises the true value of blockchain and believes its influence will only increase. “Blockchain technology is being increasingly used within manufacturing, particularly in the supply chain. Many industries, including aviation and pharmaceuticals, have well-documented problems with counterfeiting, and using blockchain can help ensure that components are genuine,” he says. “While mass adoption is yet to be seen in construction products manufacturing, this is only likely to be a matter of time, particularly within the UK as legislation will lead to an increased focus on safety.” However, Waterhouse understands that it will take time for the introduction of blockchain to be felt widespread. “In construction, there is a move towards ‘the golden thread of information ‘, and this includes a requirement for unique identifiers for every construction product and its associated literature. The aim is that building standards will improve and errors from incorrect product specification or shoddy work will be stamped out. The blockchain could well be instrumental in improving information auditing and accountability.”
“Being clear, this is not going to happen immediately. There are real barriers, such as the maturity of the systems, along with understanding, and the willingness to adopt.”
BCG: Five ways blockchain can create value in the Factory of the Future?
1. Enhancing track and trace
Companies can leverage blockchain to exchange data more easily, accurately and securely within complex supply chains. It can offer a permanent digital record of materials, parts and products, which allows for the promotion of end-to-end visibility and provides a single source of truth to all participants. These benefits are important if the supply chain includes several participants with independent IT systems or if there is a lack of trust among participants or necessity to onboard new participants.
2. Protecting and monetising critical intellectual property
Organisations across manufacturing industries face a reliance to protect IP. In tandem with cost, IP protection is an important consideration in decisions about whether to make parts in-house or buy them from a supplier. One possibility is for a company to utilise blockchain technology to help prove that it owns IP in the event of a patent dispute. For example, Bernstein Technologies has developed a web service that enables its users to register IP in a blockchain. The service creates a certificate that proves the existence, integrity and ownership of the IP.
3. Simplifying and safeguarding quality checks
By leveraging blockchain to support quality control, an organisation can scale value for customers, another primary objective of the factory of the future. Today, in the place of blockchain, providing full transparency and complete documentation to customers with regard to the quality of processes and products that require expensive support from central parties that operate IT platforms.
In addition to helping customers track and trace inbound parts along a supply chain, blockchain creates immutable documentation of quality checks and production process data. The database uniquely tags each product and automatically inscribes every transaction, modification or quality check on the blockchain. To allow this application, the production setup must include automated quality checks that generate and write measurements directly to the blockchain. This use case supports multiparty access to data and can eliminate the need for inbound quality control to verify checks that the supplier performs. It may also reduce the need for audits by original-equipment manufacturers or central authorities to verify quality controls.
4. Advancing machines as a service
Blockchain accelerates the possibilities of using an innovative pay-per-use model for machinery, often known as machines as a service (MaaS). In this model, instead of selling production equipment, a machinery provider charges for the equipment’s use on the basis of the output that it generates. For example, instead of selling a compressor, the machinery provider sells compressed air by volume. By relying on MaaS instead of owned machines, manufacturers can avoid large upfront investments and can easily upgrade equipment to gain access to the latest technology. If applied correctly, the MaaS model will allow manufacturers to scale their production flexibility effectively.
5. Enabling machine-controlled maintenance
Blockchain can support new maintenance approaches, like automated service agreements and shorter maintenance times. These innovations are necessary to manage the greater complexity and technological sophistication of advanced production machinery. In order to facilitate outsourced maintenance, users append service agreements and installation documentation related to each device to the blockchain record, creating a digital twin of the device. Blockchain technology can then allow for the automated execution of and payment for scheduled maintenance. A machine that requires maintenance can trigger a service request and generate a smart contract for the work or for a replacement part. Upon fulfilment of the order, payment processing happens automatically. In addition, immutable documentation of the maintenance history is appended to the blockchain record. Such applications, which are still in the early development phase, increase the reliability of equipment, facilitates the monitoring of equipment health and attrition and creates auditable health assessments of the machinery.
Rafi Billurcu, Partner, Manufacturing at Infosys Consulting, believes that in manufacturing, one use of blockchain that has seen success is the creation of smart contracts in global supply chains. “Documents and contracts are the beating heart of any supply chain. Rather than storing these in silos across the legal, procurement and accounting departments of various companies, as in a traditional supply chain, in a blockchain, each of these elements can be stored on decentralised and highly-encrypted nodes in a ‘smart contract’.
“Instead of existing on paper, smart contracts exist as a computer programme on a blockchain. The terms and conditions of a contract are unable to be changed, ensuring a level of trust that can’t be achieved by humans alone. What makes smart contracts truly ‘smart’ is their ability to not only streamline and automate entire processes but to perform human tasks such as monitoring inventory or negotiating prices with other parties. In all, smart contracts can automatically track supply chain levels, inventory levels and prices, replacing expensive, manual processes. This ultimately reduces cost and enables manufacturers to maximise profits – without compromising on credibility and trust.”
What does the future hold?
Manufacturing has always been considered an industry that is set in its ways. However, with technology such as blockchain, AI and machine learning playing a more influential role, the Factory of the Future is set to look very different. As blockchain technology matures, it will, through trust, allow manufacturers to clear some hurdles that have impeded the full-scale deployment of other next-generation technologies and innovative business models. As a result, more efficient factory operations that require data sharing and collaboration among complex networks of companies and machines will be created and set as a new norm across the industry.
Billurcu adds that with blockchain-based smart contracts having a greater influence across supply chains, any buyer can find a contract and act on instantaneously. “This means they get the product they need and can pay for it without the expensive overheads associated with traditional supply chains,” says Billurcu. “This could mean a radical overhaul in the way international trade is conducted – by speeding up transactions, reducing reliance on paperwork, and bringing cost-efficiency to the fore.”
With the future in mind, Waterhouse has a clear vision of what the coming years could look like in a blockchain world. “A blockchain approach would improve standards, increase trust and also improve project delivery speed as the need for human validation at every step would be reduced. This would lead to knock on improvements around product availability and lead times.”
- Digitalisation as a Strategy to Attract and Retain WorkersDigital Factory
- UPDATED VENUE & DATE – Manufacturing LIVE Chicago 2025Sustainability & ESG
- ABB Cuts Industrial E-Waste in Quest for CircularitySustainability & ESG
- Why Are Manufacturers Doubling Down On Digital Twins?Digital Factory