Smart Factories & MES: Bridging Tradition with Industry 4.0
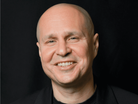
In the dynamic world of manufacturing, where the trendiest topics include the implementation of Industry 4.0, embracing AI and the power of cloud computing, sources usually mention MES in direct connection with Industry 4.0 and the smart factory. However, MES isn’t a brand-new concept or solution. So, should we dismiss MES as seemingly “outdated”, or does it remain a powerful tool for transitioning to Industry 4.0?
What is MES?
MES, or Manufacturing Execution System, is a software-based solution designed to gather and manage data at the production level. It ensures everything operates together seamlessly, from the shop floor to the overall company operations. Its objective is to enhance and simplify manufacturing operations, guaranteeing efficiency, visibility and control throughout the production process.
One widely adopted MES framework is the ISA95 model from the International Society of Automation (ISA).
This model sets the standard for designing, operating and integrating MES systems with other enterprise systems like Enterprise Resource Planning (ERP). It establishes the bridge between the enterprise and control systems, fostering seamless data exchange and coordination across different manufacturing hierarchy levels.
Another notorious MES model was proposed by MESA International in the early 90’s.
The MESA model describes 11 MES functions that are needed within four walls of the manufacturing plant.
MES systems vary significantly depending on the type of production - whether it's discrete, batch, or process-oriented - as well as the specific industry, such as oil and gas, food, pharmaceuticals, automotive and others. Each production type demands unique data collection methods, while industry dictates compliance requirements. Choosing the right solution is vital, it should not only meet your current requirements but also be adaptable to changes in processes over time.
MES and Industry 4.0
It should be noted that MES originated in the 90s during the third industrial revolution, marked by the introduction of computerisation and automation in manufacturing.
Industry 4.0, or Smart Manufacturing, on the other hand, represents the fourth industrial revolution, characterised by the integration of digital technologies such as the IoT, AI, machine learning, big data and cloud computing into manufacturing processes. The goal is to create "smart factories" that embody efficiency, flexibility and responsiveness to customer needs. According to MESA’s White Paper 52, Smart Manufacturing is the endeavour to design, deploy, connect and manage enterprise manufacturing operations and systems that enable proactive management of the manufacturing enterprise through informed, timely (as close to real-time as possible), in-depth decision execution.
In simpler terms, Industry 4.0 is about harnessing smart technology to enhance manufacturing, relying on data-driven insights to continuously improve processes following the cycles “collect data” -> “analyse” -> “act”. But how does MES correlate with Industry 4.0?
MES: A Key Player in Industry 4.0 Implementation
While MES focuses on overseeing operations in real-time and may not heavily emphasise data-driven processes, it plays a crucial role in collecting and organising data, along with a certain level of analytics.
Beyond basic data collection and organisation, modern MES systems often include intelligent real-time actions based on the analysis of the collected data.
An excellent illustration of this is Active Traceability, an MES function that analyses the success of manufacturing operations, preventing the production and shipment of quality suspect products. This function reduces losses related to waste and improves productivity. Moving beyond error-proofing to a broader concept of achieving quality assurance and minimising waste - main goals in the collective pursuit of sustainability - MES plays an important role by facilitating seamless data collection and visualisation.
Another example is the predictive maintenance function that initiates maintenance jobs based on the deviation analysis of process parameters. The AI technologies are capable of “predicting” equipment breakdowns and minimising losses related to unplanned downtimes.
While AI was not originally envisioned in MES, it still has analytic capabilities that contribute to predictive analytics, optimisation and decision-making. Moreover, modern MES systems are getting more and more empowered with digital twin and AI models to drive the decision-making process. The data collected by MES becomes instrumental in crafting AI models and constructing digital twins, facilitating simulation and analysis, offering a clearer understanding and improved management of the manufacturing processes.
Obviously, MES is envisioned as the foundational cornerstone for transitioning to Industry 4.0. Can Industry 4.0 principles be implemented without MES? Certainly. However, dismissing MES as outdated would be overlooking a crucial ally in the journey toward Industry 4.0 excellence. While MES isn't initially a part of Industry 4.0, it not only lays the groundwork for the seamless transition, but also remains an integral part of the present and future manufacturing landscape. MES proves to be a valuable asset, enhancing efficiency, flexibility, and the overall success of the smart factories envisioned by Industry 4.0.
For more articles from Yuri Pilipenko on Industry 4.0 and ways to improve manufacturing, visit https://olsom.net/
******
Make sure you check out the latest edition of Manufacturing Digital and also sign up to our global conference series - Procurement & Supply Chain 2024 & Sustainability LIVE 2024
******
Manufacturing Digital is a BizClik brand.