Stora Enso: digital disruption in manufacturing
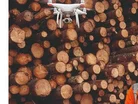
Stora Enso is a leading provider of renewable solutions in packaging, biomaterials, wooden constructions and paper on global markets. With an aim to replace fossil based materials by innovating and developing new products and services based on wood and other renewable materials, Stora Enso’s products provide a climate-friendly alternative to many products made from non-renewable materials, and have a smaller carbon footprint.
Marko Yli-Pietilä is Head of Smart Operations at Stora Enso and has been with the organisation since November 2017. He believes that although digitalisation has been present in the industry for a while, Stora Enso’s digital drive has recently been ramped up. “Digitalisation has been present for a considerable amount of time in the industry because in the process industry you need data to maintain a stable production of your products,” explains Yli-Pietilä. “We’ve collected data for a long time and used it for process optimisation however, there has been an even greater focus on digitalisation over the past few years. As an example, we have implemented a group fund of €10mn annually to support digital innovation and have really outlined our intention to welcome new technologies. Moreover, we have a centralised digitalisation team to support the businesses in all of their digitalisation efforts.”
Stora Enso understood early on that the digitalisation of its mill operations would help with efficient production and resource use, in addition to increased safety and higher quality, as well as product and service innovation. Yli-Pietilä believes in a proactive approach and outlines several key areas his organisation is focusing on at the moment. “The focus is on operational efficiency and safety,” he explains. “We focus on product quality, equipment availability, performance and safety and they are our key areas in terms of digitalisation. We identify problems in our operations that can’t be solved through traditional methodologies or we see that digitalisation provides the best option to improve things.”
With COVID-19 disrupting industries across the world, Yli-Pietilä outlines the impact the pandemic has had on Stora Enso, however stresses that his organisation was fortunate to already have the digital infrastructure in place. “It’s had an impact on our interaction with external partners in the sense that we’re now very careful with letting external people into the mills,” says Yli-Pietilä. “However, our core operations have remained largely unchanged. We already had the core infrastructure and capabilities to do work while mobile and have, for example, used mobile maintenance for a considerable length of time already.” Yli-Pietilä adds that Stora Enso has even introduced a new production line remotely during COVID-19. “It was a great achievement for us because no one thought it could be done,” he explains. “This means our equipment vendor is on the other side of the world helping us locally and commissioning new production lines and supporting us remotely. We harness different virtual collaboration tools so that people at the mill could show what they’re doing and this virtual online collaboration has been key. These tools have been influential in helping us during the pandemic.”
Establishing partnerships with suppliers is important to Yli-Pietilä and he explains that each organisation Stora Enso partners with has the opportunity to be successful and long-term. “In digitalisation, we have an ecosystem approach. We give small and medium sized companies a chance to be successful with us and have worked with a number of startups, as well as working with very large companies,” he explains. “I believe that building mutually beneficial relationships leads to success. In addition you have to have the structures in place. For example, we have implemented a cloud environment and data lake where data from both our own applications and vendor applications can be kept together in one place.”
With the future in mind, Yli-Pietilä has a clear plan of what the next few years at Stora Enso and the wider manufacturing industry could hold. “We’ve defined a vision of what a digital mill will look like in 2030 in Stora Enso,” says Yli-Pietilä. “We expect the automation level to increase, with an increasing amount of centralised operations at the mills in addition to remote operations.” There will be a greater interest in virtual reality and I expect more real-time visibility into what is happening at the manufacturing sites. We will also see more autonomous vehicles present at our mills,” he says. “Robots will become more prominent and there are already a number of industrial robots in place, but we will see more dynamic robots that will perform multiple tasks such as carry and transport products around the mill. We’re already currently using autonomous drones to do area surveillance in some of our mills so this will definitely increase in the future. Over the next few years, we want all of our reactive work to be proactive. For example all maintenance will be planned based on prediction. We’re also building prescriptive capabilities which will mean that away from predicting what will happen we can tell experts what to do in order to optimise their work. Over the next few years, we want all of our reactive work to be proactive.”