3DS DELMIA: Manufacturing Innovation with Virtual Twins
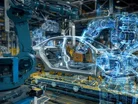
Manufacturers in just about every industry are already embracing the reality of Industry 4.0—that the digital transformation of factories is necessary, replacing manual processes with automated systems in cyber-physical smart factories. This is crucial to manufacturers as challenges caused by global disruptions can make it even more challenging for them to ramp up production to satisfy ever-volatile market demands.
There are many subtle differences in the obstacles faced by manufacturers in different industries, but there are also a few key challenges that all manufacturers have in common. Having a limited number of assembly lines makes it difficult for manufacturers to keep up with the rising demand for customised products as well as the accelerating rate of innovation (and by extension, obsolescence) in new products.
Many manufacturers still lack the visibility required to respond to supply and demand volatility in an agile manner. At the same time, it can be challenging to be mindful of the growing list of certifications required and regulations that manufacturers need to comply with—in addition to the growing pressure for manufacturers to shift towards more sustainable practices.
To be able to adopt digital transformation towards smart manufacturing, what manufacturers need is a solution where the virtual and real worlds converge in perfect synchronisation. With that in mind, manufacturers require real-time data from the real world, that can be used to model, plan, optimise and execute manufacturing operations with minimum risk. The team at 3DS DELMIA, part of the Dassault Systèmes Group, takes a closer look at just how effective virtual twins can be.
Optimising Operations Across the Value Chain
Virtual twin platforms come with a whole host of benefits and equip manufacturers with solutions for improvement at every stage in their value chain, allowing for better strategic and tactical decision-making. Listed below are some of the most pertinent:
Facility Planning
Using anything from 2D drawings to fixed point scans of physical facilities, the 3D virtual twin allows manufacturers to plan assembly lines in a way that optimizes the use of the available physical space. Perfect planning of assembly lines, workstations and tools through the virtual world minimises potential risks and avoids costly layout redesigns after the physical facilities have been installed.
Process Planning
The Virtual Twin Experience can be used to plan the use of materials and resources in products, optimal processes for maximised production output, as well as safe work conditions. Virtual simulation of processes allows manufacturers to eliminate potential process or quality issues ahead of execution—reducing launch times and scrap while saving time and money from building manual prototypes.
Manufacturing Planning
On a more tactical level, the Virtual Twin Experience equips manufacturers with the capabilities to adjust and optimise production while managing constraints in manufacturing, assembly and distribution. This can be applied to areas such as supply and demand planning or sales and operations planning through the use of forecast data—or help generate an optimised master production schedule.
Manufacturing Execution
When it comes to manufacturing operations management, the virtual twins give manufacturers the agility and flexibility needed for tactical decision-making. Real-time visibility over all operations allows manufacturers to promptly carry out unplanned maintenance on machines or identify an urgent need to requisition materials—reducing downtime, eliminating silos and minimising risk.
Raising Competitiveness Through Manufacturing Excellence
Companies have a prime opportunity to optimise and maximise returns in their manufacturing operations by leveraging the extensive capabilities of the virtual twins. By planning optimal processes and enhancing the cohesion between design, engineering and manufacturing, manufacturers can see a significant impact in:
- An increase in efficiency and operation rates
- Cost savings from elimination of physical prototypes
- Increased speed of NPI and time to market
Sustainability in Manufacturing
At the business level, sustainability is becoming the most critical lever for strategy. It is shaping a new set of values that companies must embrace to ensure relevancy, conquer new markets, prepare their workforce for the future, and become part of the solution. Virtual twins are proven to provide manufacturers with a clearer vision of how key equipment can be run more sustainably – with many businesses already tapping into the potential that virtual twins provide.
There is no doubt that the world is moving towards a more sustainable future, and manufacturing must adjust to fit in line with this shift in thinking. Thankfully virtual twins provide business owners with a wealth of information that is geared towards not only sustainability but also longevity and operational excellence.
Innovation is at the heart of everything that manufacturers do, so there’s plenty of reason to get behind virtual twins and the multitude of benefits they offer to your business. From taking positive steps in reducing your business’ overall carbon footprint to guaranteeing each part of the manufacturing process is fully optimised, virtual twins can help.