5 Minutes With Ericsson's Sebastian Elmgren on 5G
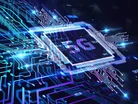
My name is Sebastian Elmgren. I am located in Stockholm, Sweden. I am working at Ericsson as a portfolio manager for smart manufacturing focusing on partnership and business development. I have a background from the Ericsson Supply organization and worked with strategic initiatives in our production for 10 years before moving over to the product side.
How Does Ericsson Operate in the Manufacturing Industry?
Our main focus for the manufacturing industry is dedicated 5G networks optimized for industrial use. These private networks provide a stable, secure and flexible infrastructure for a factory’s communication needs. Around these networks, we are building a broad ecosystem of partners for an end to end use cases.
What role will 5G play in the connected factories of the future, how does the technology further this goal?
The connected factory of the future is driven by data. Data is collected, data is analyzed and then actions are taken based on the data. 5G is the connections between these steps. It makes it possible to collect a huge amount of data from the production floor, move it to wherever it should be analyzed and then send commands back to production all with very little delay.
How Does 5G Further the Advancement Towards Industry 4.0, Could it be the Missing Link?
5G also connects the local factory with the existing global infrastructure as the same technology are used both for local connectivity as well as global. This makes it possible to go beyond connecting only a single factory. We can start connecting the whole supply chain and the whole life cycle of a product. Unlocking all the promises of Industry 4.0.
Yes, I believe 5G could be the missing link. 5G is the only technology that can address all the use cases of industry 4.0 both locally and globally.
How Does 5G Improve Manufacturing Operations, What Value Does it Provide Manufacturers?
- Flexibility: 5G brings the flexibility of wireless connectivity needed for the flexible factory of the future, securely and stably as needed for industrial use cases.
- Improved connectivity: the manufacturer will need to collect a massive amount of data from their production lines. 5G can handle the high density of devices needed for this with high reliability and performance.
- Low latency: to act on the collected data, manufacturers need a network that provided a low and predictable latency to control their operations. 5G will provide this low and predictable latency making the possible to implement closed-loop use cases.
- High reliability: Industrial use cases require very high reliability. Even the shortest stop in a production line can be costly and many shortstops during a year add up to huge amounts. When more things in production become connected the connectivity will be a crucial part to keep production up and running and 5G will be able to deliver the high reliability required by the manufacturers.
- End-to-end traceability: A highly requested feature from 5G is the precise positioning that will be included in the coming releases. This will create an indoor “GPS-System” making it possible to track anything that is connected to the system. To be able to track things indoors without adding tags or installing anchor points and to use the same infrastructure for both positioning and communication will open up a whole array for cost-efficient and easily implemented track and trace use cases.
- Real-time: real-time is not only about things happening fast it is also about the predictability of the communication and that a package always will arrive within a set time frame. Many industrial applications especially within automation require this type of communication as operations are tightly in sync and need to happen in the correct sequence. If we shall be able to substitute cables in this type of applications the wireless technology used need to be able to fulfil these needs. Again 5G will have the performance to do this.
Where Should Manufacturers Start When it Comes to Deploying 5G Within Their Operations?
One area that is easy to start with and often have a short payback time and is applicable for most companies is predictive maintenance. It also creates a good foundation to start building other use cases.
What Are the Best Strategies and Practices?
I think the best strategy is to go step by step and not try to do a big bang implementation. It is also important to have a purpose with everything you are doing. Do not start collecting all data that can possibly be collected only because it might be good to have. Collect only the data that you know what to do with and then build from that.
What Advancements Have Been Made so Far When it Comes to 5G in Manufacturing?
I would say that the biggest advancements have been in the build-up of the ecosystem around 5G. We see more and more companies adopting the technology both from the supplier and user side. This ecosystem is what will unlock the full potential of 5G in the end.
What Real-World Applications of 5G in Manufacturing Have You Seen?
We are starting to see all kinds of 5G applications being implemented. Everything from Drones, AR, machine vision and AGVs to works safety, energy management and connected screwdrivers.
What Are the Challenges When it Comes to Deploying 5G and How Can Manufacturers Overcome Them?
One of the challenges that we often see is that companies do not have an IT infrastructure that supports the massive amount of IoT use cases that are being implemented in factories. Most IT environments are built for handling laptops in an office environment. Not robots, AR headsets and drones in a factory environment. This is creating completely new requirements that need to be fulfilled.
What do You Think the Future Will be for Manufacturing and 5G?
I think we will see an even more flexible production in the future. Where everything is made to order and customized to reduce waste without adding extra cost or lead time. That would be a super exciting future that would have a great impact on every part of our society.