5 minutes with IBM’s Skip Snyder on Industry 4.0
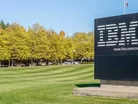
Skip Snyder, Senior Partner at IBM Global Business Services
Talk me through the industrial revolutions so far over the years?
Since the Industrial Revolution of the late 1700’s, manufacturing has continued to evolve, gaining new capabilities & improving efficiency. The first industrial revolution involved mechanisation through water and steam power. The second, with the advent of electricity, heralded assembly lines and mass production. The third involved the adoption of computers and automation and now, the fourth industrial revolution will continue to enhance that with smart and autonomous systems fueled by data and machine learning. Most manufacturers are currently at a transition point from Industry 3.0 to Industry 4.0
So how would you define industry 4.0?
In a nutshell, Industry 4.0. will take what was started in the third revolution with the adoption of computers and automation and enhance it with smart and autonomous systems fueled by data and machine learning to provide balance to thrive in disruption.
The first through third industrial revolutions focused on the efficiency of the physical processes. This Fourth Industrial Revolution with its unprecedented speed and scale allows you to take a more data-driven approach to operations. This data, pulled from your assets, adds value and enables smarter decisions. As you integrate more assets into business workflows, along with technologies like 5G and edge computing, your challenge becomes uncovering what matters – finding the right insights, at scale.
What is the best strategy for organisations to adopt industry 4.0 within their operations?
In a manufacturing plant where IT and OT may operate in information silos or in an organisation where processes differ in varying degrees from plant to plant, connecting the data between the teams is pivotal.
That connection enables you to deliver the right information, to the right people, in the right context, all for better decisions. This collaborative view helps drive improved production efficiency and cost containment. AI-powered manufacturing can drive up to 30% yield improvements and 15% waste reduction.
Take for example L’Oréal. To gain more insight into the wishes and purchasing behavior of its customers and to be able to adjust production accordingly, L’Oréal combined sensors, laser measurement, cameras and advanced conveyor belts. The redesigned production line processes dozens of different products simultaneously and delivers highly personalised products tailored to the individual skin.
In the context of Industry 4.0, L’Oréal chose IBM’s Watson AI and IoT platform to be able to take the right actions at the right time. To this end, the activities of purchasing, production, packaging and delivery have been brought together in an overarching process. Technologies such as IoT, augmented & virtual reality, and artificial intelligence form the basis of this smarter factory.
L’Oreal put the user experience and requirements at the heart of the transformation thus ensuring benefits from high user adoption. Many organisations who we speak to emphasise that an Industry 4.0 project is a business change first and foremost supported by exponential technologies.
What technology is involved when it comes to industry 4.0?
Technologies such as 5G, Edge Computing, AR, AI and IoT form the basis of Industry 4.0
When Klaus Schwab, founder and chairman of the World Economic Forum, first wrote about the Fourth Industrial Revolution in 2016, 5G networks had not even been introduced.
Now, 5G reduces response times from minutes and seconds, to sub-seconds. That accelerates communications to sensors and actuators and delivers amazingly faster results. Then, couple this with edge computing, which makes it much easier to compute the massive amount of data from ubiquitous assets since you are no longer transmitting information across the network. Instead, you’re inferencing and scoring your AI by the data source, so that only the results are transmitted. This becomes especially powerful as you scale your operations.
For example, if you have 500 machines in a manufacturing plant that each uses visual analytics and inferences there on the spot. then you still have 500 machines that can submit videos or pictures, which are large files, to a server for storage if they detect an issue.
How has COVID-19 affected the adoption of industry 4.0?
Manufacturers will be facing the new normal after COVID-19. Going digital is no longer an option, it is critical for survival.
Industry 4.0, with its unprecedented speed and scale allows you to take a more data-driven approach to operations. In the midst of this unusual and global disruption, the insights gleaned from Industry 4.0 can be a vital key to operational resilience.
It can provide remote access to operate and manage plant applications in a reliable and trusted way, leverages AI and augmented reality technologies to minimise “boots on the ground” and maintains the agenda for continuous cost reduction, increasing performance and quality.
For more information on manufacturing topics - please take a look at the latest edition of Manufacturing Global.