Adapt or die – why the manufacturing sector must adopt technology to ensure future success
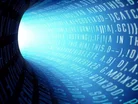
We are in the midst of the new industrial revolution. The Internet of Things and connected devices are driving unprecedented innovation across the world and consumer expectations are evolving towards more complex and customised products, a change that is now shifting towards industry – especially manufacturing.
As manufacturers try to keep up with this shift in expectation and the demand for more complex products, communication across the organisation and its supply chain and the extraction of business-critical data has become more important than ever. However, with IT systems under immense pressure and information in silos, manufacturers are missing out on new revenue streams, opportunities and value-added processes. As an example, imagine a wind turbine in the North Sea.
Today, expensive preventative maintenance routines allow businesses to keep them in optimum working order, however with sensors and predictive analysis telling them when something needs replacing this is becoming more predictive. With the digital thread however, you will also know the exact configuration of the turbine, its last maintenance tasks and even what tools and processes are needed to fix it.
Information silos vs. the digital thread
Manufacturers today have more data than ever before, but with different departments using disjointed software applications, vendor solutions and databases, many are finding that their data is stuck in silos, despite it being vital to future business success. To combat this issue, it’s vital for manufacturers to weave a digital thread of information across the entire business and its extended enterprise.
But what is a digital thread? In short, it is ensuring data flows smoothly across the manufacturing enterprise through software that enables the business and its supply chain to communicate seamlessly. Forming the backbone for digitalisation, this digital thread allows organisations to better understand their data and is the enabler to improved efficiency, product quality and financial performance. It also allows organisations to extract data to analyse and predict consumer behaviours in real-time and the agility to rapidly react accordingly, such as amending product specs in line with demand, and adapting processes to better meet these demands.
Why then are so many manufacturers reluctant to embrace this technology?
The answer lies in the lack of quality in their past systems. Traditionally, IT change at scale and pace has been too daunting, disruptive and costly for manufacturers which has led to the C-suite having an inherent distrust in it. However, Software and IT quality doesn’t just cover IT anymore, instead it affects the whole manufacturing process and the quality of the end product too. This has led to management finding themselves in the position of ‘adapt or die’, where it has become vital to adopt these technologies if the future of a business is to be secured.
Adapt or die
While the digital thread has the potential to transform the manufacturing industry, there remains an air of uncertainty as to whether businesses are ready to implement it. A lack of board level strategy, resistance to change and hordes of stagnant data are proving to be unnecessary barriers for organisations, stopping them from gaining market share through improved efficiency.
Alongside this, many unfairly assume workers within the industry to be luddites, unable to use modern technology and adapt to digital change. This is simply not the case. Gone are the days of the blue-collar worker, and in their place are employees who use smart phones on a day-to-day basis, have AI technologies in their homes and drive software-enabled vehicles. Millennials are starting to make their way through the manufacturing ranks, bringing with them an inherent understanding of digital technologies and the benefits they could bring to an organisation. Now is the time for manufacturers to understand that their increasingly digital savvy workforce is ready to embrace the digital thread and it is the business decisions makers themselves who are actually proving to be the barrier for progress.
It might sound stark, but those who don’t implement a digital thread will simply cease to exist in as little as five years’ time. As a result, CXOs need to understand that their reluctance to change is not only unfounded, but means they will start to fall behind their more digitally advanced competitors as they deliver better quality products at more affordable prices.
Ensuring quality
Software quality is at the core of the digital thread, and manufacturers looking to implement it need to ensure they have an effective quality management regime which covers the entire software lifecycle – from requirements validation through to production monitoring. By hiring quality assurance specialists to smoothly oversee implementation, manufacturers can immediately reap the benefits of a fully functioning digital thread with minimal effects on the business.
By Colin Bull, Principal Consultant Manufacturing and Product Development, SQS