Are robots closing in on your factory?
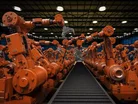
The word ‘robot’ often conjures up a negative image in people’s minds. The rampaging android from the Terminator movies, or the menacing battle droids of Star Wars. Popular opinion holds that in a few decades, we’ll be overrun by artificially-intelligent robots, operating our machinery and encroaching on our jobs, all while plotting our downfall.
Apart from being fairly well divorced from reality, that attitude ignores the fact that most advances in robotisation today are software-based, rather than embodied in a humanoid metal figure. For manufacturers looking to assess the impact of robotisation on their facilities in the near future, that’s an important distinction.
Manufacturing is, of course, one of the industries that has led the deployment of physical robots to great effect. Robots have brought many benefits including longer operating hours, greater efficiency and output and reduced room for error. The question now is ‘what’s next?’. How will the increasing sophistication of software-based automation and artificial intelligence engines translate into the factory?
Software & data analysis
The same applies to robots that essentially consist of software. There’s a clear business case for bots that can execute jobs more efficiently than people. For example, software can handle large volumes of information on system status faster and more accurately than people in order to help floor managers predict and prevent system failures. Similarly, manufacturers can discover potential areas for improved efficiency by using software to conduct digital reviews of the production line and identify processes that are underperforming.
Data analysis is a key aspect of all software robotisation - by running analyses of information coming in from IoT sensors and connected robots on the floor and throughout the supply chain, software bots can help companies get a deeper insight into trends in their business, conditions around the plant and efficiency at all levels. As more and more machines begin to generate analysable data, it’s essential to have bots in place that can turn it into useful insight.
Automated assembly
We’re also starting to see test runs of the first fully automated assembly lines, where everything from order entry to manufacturing to stock processing is conducted by automated software. Such automation makes it possible for orders placed via a webstore in the middle of the night to be automatically processed so that the product rolls off the line an hour later, ready to be despatched first thing in the morning. Intelligent business software can help manage this process from start to finish.
Visual scheduling is a key part of this, enabling drastic reductions in the time spent on shop floor planning. This functionality can come from third party software, or from an integrated part of a full suite ERP system. By integrating graphical planning boards and automatic planning, capacity bottlenecks can be immediately resolved. Full integration of automated planning with the production line ensures the entire ERP system is automatically aligned to any order changes made.
Quality control
Robotisation can also help manufacturers improve their quality control. Effective QC now involves the registry of large volumes of data. Automating these processes prevents a lot of time-consuming hassle and helps significantly reduce errors. Rather than completing paper documentation, employees can enter test results on the spot via a mobile device. This can then be centrally processed, providing a real-time view of the situation.
Real time processing of test results leads to real time reporting on quality issues, which can then be identified and acted upon much faster. Data integrity is ensured, with employees restricted to enter a certain range of data. And storing quality data in your central system offers other functional benefits as well, such as the ability to track back to the test data of a certain product batch. With these processes supported by automation, manufacturers can benefit from increased responsiveness, more effective reporting and improved customer service.
Back-office functionality
The use of robots isn’t just limited to the factory floor, either. In finance, robotisation can be used for automatic approval and processing of invoices, for example. However, this is just the beginning. If we can teach a bot to process invoices, it’s not such a big step to help it understand the rules that govern financial processes, using machine learning software. This ensures that software bots can work with a degree of autonomy. People will only be called upon when exceptions arise that the robot cannot assess.
Should you invest?
There is a great deal of speculation today regarding what jobs will or will not be taken over by bots. With a little imagination, you can see how ultimately the majority of human work could be performed by robots. Therefore, it is interesting to look at the short and medium-term impact for manufacturing firms.
In the coming years, it is expected that tasks in which people are the main bottleneck will be taken over by robots, on a large scale. Prime candidates are anything that takes a relatively long time to complete, for which we lack the mental capacity, or which is too dangerous (or boring).
For example, manufacturers could benefit from increased robot supervision of areas such as the supply chain. Robotic systems could automatically resolve issues as they arise and reorder regular shipments on a rolling schedule, with the intelligence to stop the order if the production line undergoes a scheduled – or unscheduled – stop.
The same is true of accounting, which is typically governed by extensive structures and rules, allowing tasks to be standardised and harmonised. A few years ago, it made sense to allow people to process and record invoices, but today’s software is smart enough to allow this to be easily automated.
Key points to consider
As a manufacturer, before you decide to invest in advanced robot technology, it’s advisable to consider the following four questions.
1. What is your need?
Robotisation for the sake of technology alone is never a good idea. There must be a clear advantage to using robots: for example, because the work that needs to be done is too demanding for people, or too boring and repetitive, or because machines can perform certain tasks more efficiently or qualitatively.
2. Where do you start?
Review your processes and find out where large amounts of repetitive standard operations are hidden.
3. What are the costs?
This is where the business case comes in: how do you justify the investment? When does a robot pay back the amount it cost? How do you incorporate hidden expenses, such as unemployment and retraining, into the business case?
4. Who will take responsibility?
Properly implementing and maintaining bots is a task that should not be underestimated. Make clear arrangements regarding the responsibilities this brings – is the department using the robots responsible or will it fall to the IT department?
Consider the fact that robotisation is not just a matter of technological development. Successful implementation also has important social and corporate culture aspects. In addition, you’ll also need to reconsider employees’ tasks once part of their work has been handed over to robots.
Where does that leave us?
For now, as a manufacturer, you need to focus on tasks in which people are the biggest bottleneck. Once you’ve done that, the next step is easily made: the development of a business case.
The more effective and efficient robots become, the sooner that business case can be made. Even if you don’t develop this for your business, one of your competitors definitely will, and that means they’ll eventually take the lead. It is not a question of 'whether' you’ll need to look into robotisation, but 'when'.
By Gavin Fell, General Manager UK, Exact