Bring your phone to work: how everyday smart technology can impact industry
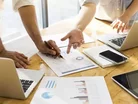
When Google Glass was first released to the public, it did not receive the expected response and the technology was deemed a failure. However, the technology did not disappear altogether, as the new and improved Google Glass is changing the factory floor. Here Jonathan Wilkins, marketing director at obsolete industrial parts supplier, EU Automation, explains how everyday smart technology can impact industry.
Technology is everywhere. It is in cars, houses and our pockets and can perform countless tasks. People depend on technology to make life easier and manufacturers rely on advances in technology to improve productivity in the factory.
As technology advances and becomes more connected by the internet, more smart devices are appearing in industrial applications. With these devices, manufacturers can streamline a range of processes on the factory floor, from assembling products to listing inventory.
With so much technology on the market, manufacturers may struggle to decide what will guarantee the best return on investment for their factory. One solution is to apply the benefits of consumer technology to industry.
Wearable technology
The popularity of wearable technology is growing rapidly, with reports predicting that consumers will buy $34 billion worth of wearable technology in 20200, totalling to around 411 million devices.
Manufacturers have witnessed the benefits of wearable technology for the public and are now using them in the factory to track workers and machines more efficiently.
Google Glass may have failed in the consumer market, but it has gone on to perform a number of useful tasks on the factory floor.
With a camera, touch pad, microphone, camera and both internet and e-mail access, workers on the factory floor can improve productivity by having all the information they need in one place. Workers can scan serial numbers on any machine to access data they need to complete work and record what they do to inform others working further down the production line.
Other types of wearable technology can also improve operations. Smart watches can improve worker safety as they track the location of the wearer, monitoring how often workers approach safety hazards. Manufacturers can then use this information to change workflows or factory layout to increase overall safety in the plant.
BYOD
Some manufacturers have introduced a bring your own device (BYOD) policy to bring more technology into the factory. They encourage workers to bring phones, tablets and other smart devices to work to access corporate data and complete work.
As there are around 2.53 billion smartphone users worldwide — a number that is estimated to increase, it is not difficult for manufacturers to introduce more technology to the factory without excessive costs.
Workers understand their own technology better than new systems, so will be more productive as they will not struggle with unknown software or accounts. Using employee technology also reduces costs as manufacturers can what technology will be the best investment rather than struggle to keep up to date.
Considerations
Adding these devices to the factory floor can vastly improve productivity and safety. However, introducing technology from different users can leave a factory vulnerable to cyber security breaches.
Like computers in our homes, factory devices must be protected from malware. Manufacturers must regularly update antivirus software to prevent systems being vulnerable to viruses.
Just because a piece of technology is not widely accepted in the consumer market, it does not mean that it cannot be used for another purpose. Devices like Google Glass may not be the technology you turn to when you take a selfie, or send a text, but a manufacturer may rely on their features to keep their factory running.