Conquering the challenges of industrial internet
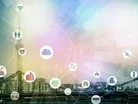
The Industrial Internet is bringing significant changes to manufacturing companies around the world. New possibilities enabled by big data and advanced analytics are pushing forward new software- and service-based business models. However, from our many conversations with senior industrial executives it has become clear that whilst the Industrial Internet is on everybody’s mind, few are managing to leverage and monetise it. So why is turning good intentions into concrete transformation initiatives so difficult?
An uphill struggle?
We have identified five key challenges that leaders of industrial companies need to overcome in order to succeed in moving from traditional manufacturing businesses toward more technologically advanced and service-led businesses.
1. Business models need to be reimagined
Customers are becoming less concerned with owning the physical machine or technology, expecting the best possible service and solution instead. As new revenue streams and entire business models are enabled through capturing data and applying advanced analytics, taking a step back and re-evaluating your business model is an important – and never easy - first stage.
2. Traditional battlefields are being redrawn by new competitors
Legacy hardware manufacturers risk being disintermediated from their customers by more nimble technology companies if they do not place data and software at the centre of their value proposition to customers. It is therefore crucial that industrial goods businesses partner with the right digital individuals and organisations to identify and claim their position in the new digital ecosystem.
3. Digital transformation requires a modern organisational culture that cultivates innovation
Unless traditional industrial businesses rethink their culture and organisational structure, moving the dial in terms of digital transformation is going to be an unlikely outcome. Whether a company should kick-off its digital strategy with a business-wide organisational transformation or start with an incubator, the approach is going to depend on its size, structure and legacy.
4. New talent won’t respond to the old ways of leading people
The executives leading the transformation will not necessarily be ‘digital natives’, so younger talent with software and technology backgrounds are essential due to the many new verticals that require deep expertise of applications. In order to bring together teams that consist of both ‘industrial natives’ and ‘digital natives’, companies must bring in leaders that are able to manage two very different types of talent profiles.
5. Software and services will dictate the required speed and agility
The pressure brought about by the product having shorter life cycles, constant updates and accelerated product development is a key challenge for traditional manufacturing businesses. In order to adjust to the new speed, many businesses will need to start by uncluttering and commercialising their IT function to ensure that it can effectively support and partner with the company as it becomes a more agile version of itself.
A new beginning
It is possible to overcome these challenges and harness the potential of the Industrial Internet.
Finding the right digital transformation leaders to spearhead the change throughout the organisation is one of the key pillars for implementing the digital strategy successfully - taking it from words to actions. Ensure that the most senior digital leader, often in the shape of a Chief Digital Officer, reports directly to the CEO. In an earlier study, Productive Disruptors (2015), Russell Reynolds Associates found that digital transformation leaders’ psychometric profiles look notably different to those of industrial executives. Moreover, across industries, they have less in common with their C-suite colleagues than anyone else in executive management. They are innovative, action-oriented and strive to challenge traditional approaches. They cut through bureaucracy with remarkable resilience, but they also excel at creating followership for their ideas in the wider organization.
Certain industrial executives are more inclined to exhibit some of these traits than others. It is important to identify these individuals via psychometric assessment to leverage the characteristics that make them well-placed to contribute to innovation and create an environment that will encourage digital transformation. The industrial heads who are successfully leading digital transformations today possess several key qualities. The combination of which might already exist among leaders within the organisation. Equally, perhaps the ideal leader is elsewhere and can be recruited to the organisation’s executive leadership. The image below lists our take on the key qualities that are necessary for digital industrial leaders:
Empower your chosen digital leaders to build new teams and lead change across the entire organization. For instance, a “fail-fast” approach is one of the key hallmarks of start-ups and technology companies and is increasingly becoming a necessity in industrial companies too. Being encouraged, even incentivised, to experiment with concept innovation is crucial for individuals to come up with new ideas as they try to reinvent legacy companies. In fact, the biggest difference between an established business and a new joiner is that the former is afraid of losing his or her position, whereas new joiners want to win and have nothing to lose.
Ensure buy-in from the top. The board and CEO need to be in charge of important decisions and changes pertaining to the company’s digital strategy, and they need to communicate their support for these changes throughout the organisation. Not only must they ensure that the company has the right talent to set a meaningful digital strategy and execute it – they must also be supporting and communicating the change as it happens throughout the organisation.
Identify digital directors. Non-executive leadership is equally important for digital success. Traditional industrial goods businesses should ensure the participation of at least one board member who has a digital background. This will help digital stay at the top of the agenda in the boardroom.
Transform your company culture. Even with all necessary systems and processes in place, a digital strategy can be thwarted by old attitudes or conflicts between what the organisation was and what it aspires to be. Company culture regarding creativity, risk taking and innovation will need to adapt to meet the demands of new types of employees and working styles. Creating the right conditions for new ideas to bubble up, and for the best ones to be realised, requires a modern company culture that is committed to attracting, retaining and developing the best technological talent. Only by committing to major changes will major results follow. Even a high-profile digital transformation leader cannot transform an industrial company on their own. Thus, the real challenge lies in taking the organisation’s larger base of industrial leadership talent on the journey towards becoming “digital migrants”, who will, over time, transform the company culture.
Offer competitive packages to the right talent. Digital talent is critical, and their options are plenty. Legacy industrial goods organisations will inevitably be competing with and getting talent from some of the biggest software and digital pure-play companies in Silicon Valley and other sectors. Technology companies typically emphasize the variable component in their compensation schemes, including stock options. Benchmark compensation structures and opportunities for progression against sectors you are competing with to optimize your chances of recruiting and retaining the best talent.
We used to get confronted with the question “Will this digital trend ever become real for Industrial Goods companies?” Nowadays, the only question we hear is “What do I need to do to stay ahead of this massive transformational force?” And in fact, securing the right leadership talent for such a Herculean task is not the worst place to start.
Jens-Thomas Pietralla is Managing Director and Head of Russell Reynolds Associates’ Industrial Goods practice.