ENGIE Impact: Reduction of Scope 1 manufacturing emissions
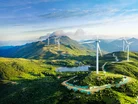
In pursuit of achieving Net Zero within the manufacturing sector, the decarbonisation of heating specifications on site is a fundamental lever that also proves to be a significant challenge. Fortunately, some solutions already exist and can be deployed immediately.
Additional innovative solutions are underway, enabling manufacturers to commence this facet of their decarbonisation journey immediately, with assurance of what the future holds. ENGIE Impact and the World Business Council for Sustainable Development (WBCSD) are working together to develop actionable principles such as the spread of carbon footprints across multiple sites and geographical areas, achieving Net Zero while optimising economic outcomes and developing a strategy that is effective across multiple decarbonisation levels.
In delving into the process of decarbonising heat in the manufacturing sector more efficiently there are four main questions to consider:
What makes decarbonising heat both a challenge and a vital player in achieving Net Zero?
To understand the challenge behind decarbonising heat, it’s important to first identify what is meant by industrial heat. Industrial heat primarily results from processing energy vectors such as oil, gas or coal, as well as Scope 1 emissions.
Additionally, heat can also produce Scope 2 emissions if converted from electricity drawn from the grid. This electricity, however, is not decarbonised.
There are a number of key reasons as to why it is difficult to decarbonise:
- There is an array of temperature and quality requirements behind industrial heating. Unlike electricity that is just one vector, heat is multiple vectors serving various needs requiring low-grade, medium or high- temperature heat, which complicates potential heating solutions
- As a result of industrial heat being used for multiple processes, new heat solutions must be compatible with the exact processes it serves, and with the reactor. This can potentially lead to some limitations or adaptation to how the assets operate
- Operational and commercial risk can be a challenge. For example, it is necessary to apply a new operational method when installing a biomass boiler to replace a gas-based asset. It also requires a new fuel supply and new sourcing avenues
- Heat decarbonisation solutions may be in the early stages of commercialisation and development, particularly regarding high-temperature conditions
- The occurrence of carbon leakage can happen if the decarbonisation of heat changes the sites production costs
- The risk of stranded assets, should energy assets not have reached their end of life before new assets are acquired and used on-site
The industrial sector uses around 32% of all energy globally, with heat representing about three-quarters of that consumption, the remainder being electricity. Moreover, 90% of all industrial heat is currently generated through fossil fuels. As a result, there is enormous potential to reduce emissions with new solutions.
What solutions currently exist and how to get started?
There is a vast array of types of heating on offer for a full range of heat requirements, depending on what the industrial sector needs. Sectors such as food and pharmaceuticals tend to require low-temperature heat, plastics and chemicals industries require medium-temperature heat, and materials processing, such as metals, cement, glass and ceramics need high-temperature heat.
There are numerous mature, low-carbon heating requirements for low-grade heating, such as geothermal solutions, biomass, electric boilers, solar thermal and heat pumps. For high-temperature, there are two proven technologies- biogas and biomethane.
The key question for manufacturers is how to identify the relevant solutions for a site and its activities? This can be achieved by looking at four assessment criteria: regulatory context, commodity availability, physical fit and technical fit.
What promising innovative solutions exist that will aid in achieving Net Zero?
The main focus around heat decarbonisation is on addressing medium and high-temperature heat. Exciting innovations include hydrogen, biomass gasification, which although in the early stages of commercialisation can convert biomass feedstock into synthetic gas, and electroprocessing, which is the electrification of equipment, such as replacing gas burners with electric furnaces.
What are the significant factors in ensuring a successful rollout?
The top factors for a successful strategy are proof of concept through using pilot sites to test new technologies, leading by example through pilot programmes and sites, prioritisation through understanding a site’s emission reduction potential, and analysing decarbonisation investments made from both return-on-investment and total-cost-of-ownership perspective.
Decisions for now and for the future
Whilst it is important to make informed decisions based on today’s possibilities, it’s also essential to know what’s coming in future years. Although a complex area, there is momentum across the manufacturing industry with organisations creating pilots that are leading the way in heat decarbonisation. The first steps for fast tracking decarbonisation efforts are to develop a strong strategy and to find an equilibrium.
Byline written by Clémence Fischer, Senior Manager, Sustainability Solutions, and Stéphane Rapoport, Managing Director, Sustainability Solutions at ENGIE Impact.
- How Consumer Goods Manufacturers Are Tackling Scope 3Sustainability & ESG
- Creating a 'Greener' Approach to Christmas Tree ProductionSustainability & ESG
- Your Guide to Manufacturing LIVE ChicagoProcurement & Supply Chain
- Digitalisation as a Strategy to Attract and Retain WorkersDigital Factory