Ericsson: driving smarter manufacturing with connectivity
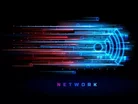
With manufacturers racing to adopt industry 4.0 technology in an effort to gain a competitive advantage, we take a look at the benefits of a connected factory.
As the world continues to technologically advance in the wake of the fourth industrial revolution (Industry 4.0), manufacturers are realising that "connectivity is the thread holding their operations together" amidst their digital transformation.
Ericsson notes that “connectivity has often been a second thought to manufacturers. When the network served fewer devices, manufacturers were satisfied as long as the available communications technology worked—or as long as they could work around the weaknesses. That’s no longer true.”
As the adoption of smarter connected factories continues to rise, so do the new and complex requirements. “As the number of remote-control and autonomous robots and automated guided vehicles (AGVs) on the factory floor increase, they will depend more and more on low latency and high device synchronicity,” says Ericsson.
With customers expecting a great variety of products in a short period of time, the industry requires ever-short market windows for products that have a level of personalisation like never before.
As a result manufacturing is evolving to deliver efficient line changes and optimised workflows for production operations, as installing or moving cables is expensive and time-consuming and a barrier to creating an agile factory.”
Ericsson also highlights that device density is an important consideration. “The number of devices per square foot or meter in the connected factory environment is multiplying exponentially,” comments Ericsson. The industry is transitioning from the proof of concept stay into real world application with dozens of workers using connected devices all at once. Therefore the network needs to be able to handle this surge of demand without hesitation, latency or bottlenecks.
The key to smart manufacturing
Wireless connectivity - this network capability enables mobility for connected devices, agility in operations and an increasing level of device density. Wireless allows manufacturers to connect widespread assets and processes in real time, allowing integration with contributing workflows. “Compared to a fixed network, the scope and ease of wireless contributes to new connections and services that can increase value, limit waste and address more pain points,” says Ericsson.
The foundations for a smarter factory
“To appreciate the role of connectivity in the smart factory, it helps to understand the evolving nature of IoT in the industrial setting,” explains Ericsson, the form different types of connectivity include: Massive IoT, Broadband IoT, Critical IoT and Industrial Automation IoT.
SEE ALSO:
For more information on manufacturing topics - please take a look at the latest edition of Manufacturing Global.