GE Digital: Operational Insights with Data & Analytics
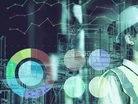
Breaking Down Silos in Manufacturing Information Systems
GE Digital starts its white paper with a vision of what the future of manufacturing operations could look like: “imagine recovering up to 20% of production capacity, reducing finished goods inventories by 30%, while validating supplier quality to reduce operational variability, risk, and rework.”
Despite heavily investing in automation solutions, most manufacturing information systems continue to exist as disparate data silos. Now more than ever manufacturers facing the challenges to balance competing priorities need modern solutions.
In its white paper, GE Digital discusses Manufacturing Operational Intelligence (MOI) as an enabling solution. Manufacturing Global specifically looks at how manufacturers can enable operational excellence, the key business outcomes, and the checklist for getting started.
Image, Image, Image: Enabling Operational Excellence
“If your company isn’t on the path towards using manufacturing performance dashboards, 61% of your competitors will be using them to drive continuous improvements in performance more accurately and rapidly,” said LNS Research.
Key MOI Business Outcomes
Undoubtedly, manufacturing priorities vary among leaders, however, most agree that MOI can have a profound impact on production operations, improving visibility, streamlining decisions, and removing guesswork. Some of the key business outcomes include:
Increase Labour Efficiencies
Looking to optimise workforce productivity? MOI dashboards can visualise operator productivity and downtime metrics.
With these insights, resource allocations can be effectively optimised based on employee productivity. Leaders can also identify additional capacity in the existing workforce instead of hiring new labour or allocating overtime.
Reduce downtime costs
Using MOI manufacturers can run predictive equipment maintenance which can dramatically reduce repairs and costs associated with unplanned downtime.
Reduce defects and related costs
With context-rich quality data, MOI can identify the root cause of a defect as well as eliminate the costs associated with waste.
This can help manufacturers to improve their focus on quality throughout the production cycles, and reduce warrant costs.
Achieve automation efficiencies
The time is now to go paperless. MOI can help plant managers and line supervisors reduce the amount of time they spend collecting, analysing and reporting downtime information. MOI eliminates human-intensive data collection, allowing workers to focus on higher-value tasks.
Increased yield
Finally, by reducing downtime, increasing productivity, and reducing defects with MOI, manufacturers can achieve higher production yields with the same resources.
Checklist For Getting Started
- Don’t go it alone
- Clearly define the objectives of an MOI pilot solution
- Scope the MOI pilot solution to be small (one to three months)
- Once successful, expand the pilot to other areas
- Accelerate the MOI journey by choosing the right partners
To read the full white paper, click here.