How is technology shaping the future of manufacturing?
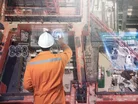
Manufacturing is rapidly changing. For the last decade, manufacturers and smart manufacturers have been experiencing growing shifts towards automation, decentralised technology budgets, adoption of cloud-based services and even the adoption of AI.
Since the pandemic, it’s become increasingly clear that manufacturing companies need to leverage the capabilities of digital solutions – or risk falling behind. Our own research has found that 73% of manufacturing businesses in Europe will increase their IT budgets in 2021. This is not surprising; over the last decade, technology has been instrumental in freeing workers from routine tasks, from warehouse to C-suite. Better productivity as a result, as well as more streamlined operations and faster times to market, are key drivers of this growth.
However, manufacturing organisations have often historically relied on legacy infrastructure and processes – so the road to digital transformation isn’t always straightforward. Barriers such as cybersecurity concerns, and knowledge and skills gaps remain very real obstacles to many. With the cost of raw materials rising, and social distancing remaining a concern, staying ahead of new breakthrough technologies, as well as hardware technologies, will be crucial for manufacturers to amply prepare for the future.
Breakthrough technologies
- Automation
While automation is certainly not a new concept, since the pandemic and the rise of the importance of remote working, manufacturers have been increasingly embracing various forms of automation in a bid to lower costs and speed up productivity. Automation in manufacturing today can look like large plants almost entirely run by robots, all the way through to small operations with strategic automation to improve a few key processes. Although size and scope depending on the individual business, automation is already and will continue to be a mainstay of manufacturing in the future, particularly where businesses struggle to find enough skilled machinists. As machines and humans get better at talking to each other via advances in software, production lines will become increasingly automated.
- IoT, AI and machine learning
As industrial efficiencies and cost-saving measures are uncovered, it’s no wonder that manufacturing sites and factories have become the new hotbed for innovation. IoT, AI and machine learning have a wide range of applications in factory automation, including asset tracking, process lifecycle tracking and enabling remote access and operation of devices that handle materials in an assembly line. By using robotics technology to speed up assembly line operations, these technologies can standardise component creation, reduce product errors and waste, and automate QA processes.
AI and machine learning are perfect examples. According to IDC by 2022, 80% of organisations that shift to a hybrid business model will spend 4x more on AI-enabled and secure edge infrastructure to deliver business agility and insights in real-time. Our own research backs up this prediction: we found that 56% of manufacturers say purchasing decisions around AI and machine learning solutions are more important now than pre-pandemic. This was broken down into 60% for wearable devices, 69% for automation technology and 63% for edge computing solutions.
AR smart glasses are also a great example of breakthrough technologies that can enhance maintenance and production by enabling a range of hands-free tasks and processes. Smart glasses equipped with a ‘See-What-I-See’ functionality can allow an onsite manufacturer who needs to make a safety or time-critical decision, to connect with a wider pool of remote experts and receive valuable support and guidance to complete a task. Additional capabilities from AR smart glasses can be accessed wherever and whenever they are needed, without disrupting the mechanic’s workflow. Indeed, 67% of manufacturers from our own research said they were likely to deploy smart glasses within the next three years, with improved information sharing and collaboration (48%) and hands-free functionality (47%) being the main reasons behind this decision.
To stay relevant in this new world, manufacturers will need to manage the pace of technological change and customer expectations. Edge computing solutions, for example, can combine with next-generation wearable devices such as smart glasses to bring AI and IoT into various professional environments.
Hardware technologies
Naturally, when it comes to technology, hardware is just as important as software. Small details can play a huge role in supporting an increasingly mobile workforce, and careful consideration must be given to laptops in particular – one of the key game-changers in the new remote-working reality.
Equipment for manufacturers that split their time between being remote and onsite needs to fulfil four main criteria. The first is portability. The modern-day machinist needs more lightweight devices that are easy to carry around, particularly if they are working on the move, or balancing remote with on-site work. Indeed, our research found that portability was the most important feature for 70% of manufacturers when thinking about purchasing new devices
The second criteria is performance. Lightweight equipment also needs to be robust and hardworking to both lighten the load on IT support, and to enable optimum productivity for workers. This was seen as one of the most important features for 78% of manufacturing respondents.
The third (and arguably most important) is security. 81% of our manufacturing respondents considered device security when making purchasing decisions and it is easy to see why. When talking about security risks due to remote access, the discussion tends to centre around the office and home working. But manufacturing and industrial facilities also face challenges that have been intensified due to the shift to more remote working. While security risks to Operational Technology (OT) aren’t new, OT engineers traditionally have shared admin access, which becomes challenging when these environments are being logged into remotely. Devices that are built securely, and that allow for monitoring, authentication and access control are crucial for business safety. Indeed, our own research shows that 75% of manufacturers say purchasing decisions around laptops are more important now than before the pandemic
Finally, equipment, including accessories, needs to satisfy a fourth criteria: connectivity features. Organisations need to take special care to monitor all of their remote connections in real-time, and actively manage user access requests based on purpose, length and frequency. As remote connectivity becomes more commonplace, it will become critical to define and enforce granular access permissions for all remote users, to mitigate the chance of opportunistic hackers attempts to gain access to important networks.
Shifting to the new normal has provided the potential for millions of manufacturing companies to improve their operations. However, the foresight of new technologies, business safety and carefully selected hardware is critical for this transition to work successfully. In the face of unprecedented transformation, it is necessary to reconsider how we work, and how technology can help manufacturing leaders learn from these changes and stay ahead of the curve.
- Digitalisation as a Strategy to Attract and Retain WorkersDigital Factory
- UPDATED VENUE & DATE – Manufacturing LIVE Chicago 2025Sustainability & ESG
- ABB Cuts Industrial E-Waste in Quest for CircularitySustainability & ESG
- Why Are Manufacturers Doubling Down On Digital Twins?Digital Factory