IDTechEx: Metals are Near 3D Printing Market Readiness
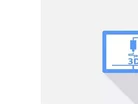
Despite a temporary setback owing to the COVID-19 pandemic, the market for 3D printing of metals is expected to see a significant rise over the next decade. Within that, it is anticipated that most of the revenue will be attributed to material sales. The relevant powders are both gaining supply chain maturity and have a rapidly expanding portfolio; there are many desirable properties, yet to be realised, that are close to the market.
The metal additive manufacturing market will exceed US$10bn within the next decade. IDTechEx has released a detailed report "Metal Additive Manufacturing 2020-2030" providing technology benchmarking, player analysis, and granular 10-year forecasts.
The forecast for metal powders is significant to this future growth. Multiple metals have led the early wave of adoption, including titanium, Inconel, and various steels. However, there are numerous traditional metals and properties missing from the additive manufacturing toolkit. A previous article highlighted some young companies expanding this space, and this article provides a deeper dive into 3 of those properties. The metal alloys highlighted occupy a range of technology readiness; there are some commercial success stories, but notable market adoption will be in the longer-term.
Low Elastic Modulus
A highly desirable property for an additive manufacturing powder would be an elastic modulus of under 50 GPa while maintaining high tensile strength. This is specifically for personalised implants in the medical and dental industry, so also requires biocompatibility and osseointegration. This is a logical and attractive market to additive manufacturing players gaining notable attention. TANIOBIS are the most notable company in this field with their AMtrinsic material; they see good potential for their tantalum and niobium-based alloys and are beginning to ramp up production and look towards certification. Global Advanced Metals (GAM) have also been active in the field of tantalum additive manufacturing again citing the medical sector, and there have been a few early successful examples demonstrating this potential. Z3DLAB is a young company that plans on bringing a new approach by producing a modified CP-Ti alloy with an elastic modulus as low as 35GPa under the brand name ZTi-Med.
Electrical and Thermal Conductivity
Being able to 3D print highly thermally and electrically conductive bulk materials would open up a large opportunity. The most obvious target is copper; many have trialled this and realised it is anything but facile. Very low absorbance of laser energy, rapid heat dissipation, high ductility, and high propensity to oxidation makes it a very challenging material. The potential in fields like heat exchangers, induction coils and beyond make it a key target.
There are notable advancements facilitating this and making it a keyspace to watch. They include:
- Laser optimisation, with blue and green lasers both being trialled.
- Alternatives to SLM approaches such as using EBM or binding in a metal and going via green part.
- Finding suitable copper-rich alloys that can still achieve >85% IACS. GRCop and CuCrZr appearing as the frontrunners.
High-Temperature and Wear Resistance
Refractory metals are the most obvious in this category, of which some Ta and Nb-based alloys were previously outlined. Tungsten-based alloys also show a huge promise as do some of the more exotic high entropy alloys that are rapidly progressing from academic interest to the commercial frontline. Producing suitable spherical powders and the associated printing parameters is not easy for these high melting point alloys, but with again good target markets in bespoke tooling, turbines and beyond it is another prime area to gain market penetration over the next decade.
Beyond this, one repeated approach is having metal alloys tuned for and benefiting from the additive manufacturing process. The inclusion of ceramic particles, as demonstrated by Elementum3D, Gamma Alloys, and others, production of nanocrystalline alloys, such as those from Veloxint, or the use of amorphous alloys, most notably by Heraeus, all exemplify this.
Outside of these property progressions, there are numerous other considerations that can help facilitate this market. The powder morphology, cost and density are all essential not to mention the manufacturing process itself to achieve good yields and particle-size distribution. Young players and highly established players are both gaining prominence, the success will not be quick, and patience is required particularly for end-use applications with extensive qualification requirements, but with the AM powder portfolio in its infancy, there is a huge potential.
The metals are not the only developments progressing this industry; previous articles highlighted the opportunity for cheaper printers and wire-based feedstocks, to name a few. The metal additive manufacturing market report gives targeted analysis into this industry, providing the latest forecasts with key technical insights. This research is based on a long history on the field and includes over 50 company profiles based on primary interviews, bringing the reader the most detailed understanding of the metal additive manufacturing industry.
- Digitalisation as a Strategy to Attract and Retain WorkersDigital Factory
- UPDATED VENUE & DATE – Manufacturing LIVE Chicago 2025Sustainability & ESG
- ABB Cuts Industrial E-Waste in Quest for CircularitySustainability & ESG
- Why Are Manufacturers Doubling Down On Digital Twins?Digital Factory