3 tips for increasing safety in manufacturing facilities
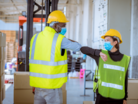
Safety is a significant concern in manufacturing facilities and warehousing. According to the United States Bureau of Labor Statistics, there were 4,764 fatal workplace injuries in the U.S. in 2020. This industry requires workers to take part in high-risk activities such as welding, soldering, heavy lifting, raw material assembly, and metal cutting. In addition, hazards like harmful radiation, extreme temperatures, electricity, and height can cause injury to plant workers.
Workplace accidents can be fatal or cause irreparable damages. They can also lead to litigations against the company.
Therefore, companies need to develop strategies to ensure that the workplace is safe for all employees. This article will provide three essential tips to increase safety in manufacturing and warehousing facilities.
1. Use of appropriate manufacturing machines, equipment, technology and tools
Employers should provide employees with the appropriate and modern tools, equipment, and machines. Warehousing equipment will enable the workers to undertake their duties safely. In addition, personal protective equipment (PPE) plays a crucial role in preventing and safeguarding employees from injuries. PPE may include helmets, safety boots, gloves, and face shields.
Warehousing and manufacturing facilities should also ensure the installation of guarding mechanisms. Guardrails and barriers are crucial in ensuring that only qualified employees can access certain areas. Ensure you equip cutting equipment and machines with safety features that protect the workers’ fingers.
Furthermore, ensure that the machines and equipment are maintained regularly. Remember to inspect the condition of the machines and equipment before use. For example, a loose bolt on a forklift may be a recipe for an accident.
2. Safety training and awareness in manufacturing facilities
Providing regular training on safety protocols is critical, whether the employee is an expert or apprentice. National safety guidelines keep changing, necessitating periodic training for workers. Safety programmes play an essential role in reducing the risk of industrial accidents and injuries.
Furthermore, some workplace-related injuries result from misusing machines, equipment, and tools. Employees should always use machines for their intended use only and should follow the manufacturer’s instructions.
Employers should ensure that all workers are adequately trained on using machines and equipment. Only skilled and qualified personnel should operate machines.
Most manufacturing facilities and warehouses use electrical machines and equipment. Such equipment requires the operator to be alert, and just a tiny mistake can result in fatal accidents. People are prone to making errors and mistakes when they are tired. Providing your workers with periodic breaks will ensure they are not fatigued or overworked.
3. Floor layout and plant design
Proper floor layout and plant design can reduce common safety threats. For example, anti-slip flooring is a must, especially in facilities that handle liquids frequently. Such facilities should also have drip pans and other safety guards that reduce the risk of falls.
A safe plant layout ensures that toxic, flammable, and hazardous materials are correctly stored. Furthermore, the plant design should have adequate ventilation. Equipment like industrial vacuums also assists in ridding off dust and unsafe matter that may cause long-term health issues.
A cluttered workplace also increases the risk of accidents. A well-organised and clear workplace reduces the probability of accidents drastically. Always ensure that exits are clear, giving your employees a quick escape in case of an emergency.
A recent Global Burden of Disease (GBD) study shows that about 1.7bn people have musculoskeletal disorders (MSD) globally. In addition, MSD is responsible for nearly 30% of workplace-related injuries compensation. Therefore, workplace ergonomics is essential in preventing injuries.
Common ergonomic risks include bending and twisting the torso, leading to muscle strain. Employers can invest in robotic systems to automate repetitive tasks. Furthermore, heavy-duty industrial carts can assist in handling heavy materials and reduce the risk of MSD.
Managers should find the right strategy to improve manufacturing facilities and warehouses safety. Such facilities can be much safer with the correct approach. Finally, workers should be aware of common safety hazards to identify and report them early.