Jump starting digital transformation in manufacturing
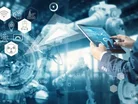
Manufacturing has always been an industry which harnesses technology in order to deliver greater efficiency and productivity. It’s a trend which we’re set to see increase especially as more manufacturers adopt digital technologies and Industry 4.0 gains traction. In fact, IDC research suggests that by the end of 2019, 75% of large manufacturers will update their operations with Internet of Things (IoT) and analytics-based situational awareness.
IoT technology is changing the manufacturing industry and transforming traditional, linear manufacturing supply chains into dynamic, interconnected systems. IoT takes networked sensors and intelligent devices and puts those technologies to use directly on the manufacturing floor, collecting data to drive artificial intelligence and predictive analytics. It means that manufacturers have detailed real-time data at every point during the manufacturing process and through the distribution chain.
Creating a digital network
Manufacturers are increasingly using data to improve their production processes, achieve greater consistency, and to create safer working environments. The combination of the IoT and the increasing digitisation of information has resulted in an explosion of data. With systems and devices exchanging vast amounts of information, manufacturers need to ensure that robust real-time integrations are in place – as information is constantly being shared with supply partners and those within the distribution chain. This level of activity is likely to place substantial strain on IT infrastructure, especially the software-defined wide-area network (SD-WAN) which supports communications spanning large geographical areas.
Many of these existing networks are long in the tooth and were designed before digital manufacturing became commonplace. For Industry 4.0 to be successful manufacturers must have the appropriate network infrastructure in place which has the ability to prioritise applications and workloads to ensure appropriate service levels. With so many moving pieces, it’s important that IT teams build a strategic digital infrastructure platform that can support all of the initiatives enabling Industry 4.0.
Many CIOs in the manufacturing sector view increasing operational efficiency and transforming the business as imperative to driving technology investments. With this in mind, IT platforms should provide the integration and coordination required for success. However, it’s likely that the IT team will also utilise partners with specific expertise, skills, and technology. Managed service providers (MSPs) are a key component to any effective IT strategy as they offer leading solutions and the skills to deploy, administer, and manage them.
See also
- Waymo is looking at partnering with the Nissan-Renault-Mitsubishi alliance
- Tesla looks to develop an electric Mercedes-Benz Sprinter van, reigniting an old partnership
- Hanergy is launching the first $1bn solar industrial park in the Middle East
However, when working with network service providers, manufacturing companies should let their risk management strategy lead the solution design. For instance, network connectivity should be prioritised for high-profile manufacturing plants that greatly impact revenue generation versus other, low-profile plants. Software defined network platforms offer state-of-the-art traffic prioritisation capabilities to create a completely customised IT infrastructure that gives precedence to critical locations, applications, and user groups. Most importantly, these priorities should be quickly and easily adaptable when things change.
Operating seamlessly
With a focus on achieving a new level of automation that integrates any or all parts of manufacturing, it’s also important that IT teams take into account security considerations. As more systems ‘go online’ and data is shared across numerous partners, suppliers and location, the risk of cyberattacks increases. The deluge of data that IoT devices generate will be a huge target for malicious hackers looking to steal proprietary or personal data.
Manufacturing companies can use network segmentation as a way of separating and isolating individual product lines into sub-networks to provide security and improve performance. For instance, if a supplier was to be compromised then they could spread the infection through sharing data with others. SD-WAN allows IT teams to limit or block unauthorised applications in order to safeguard both security and performance.
However, it isn’t just security considerations which need to be accounted for, as new capabilities are introduced to the network it will also bring on new pressures. For instance, there is currently a big focus on machine learning and building machines which can act more intelligently. In doing so, manufacturers can optimise operations by changing activities based on key inputs, without the need for human intervention. The result will be better decision making on both sides of the supply chain. Intelligence at the product level enables proactive support or maintenance to limit any downtime or update products. Although the impact on IT infrastructure will be substantial, as the information being utilised increases logarithmically and requires real-time communications.
Technologies like IoT, big data analytics and SD-WAN are advancing manufacturing forward, with a more efficient workforce, safer operations, and maintaining high standards in production quality. With Industry 4.0 transforming the manufacturing industry into a digital model, the goal of a fully integrated organisation that designs, builds, delivers, and tracks the use of manufactured products is the top priority. It’s important to keep in mind that the starting point for the path to Industry 4.0 will be the deployment of a next-generation and secure IT infrastructure that can support individual projects that are the milestones of this journey.