Manufacturers’ first step towards Industry 4.0 success
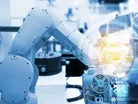
Could fear of failure be preventing Industry 4.0 technology from reaching the factory floor? James Wood, Director of Business Development, EMEA & APAC at Aptean, outlines why manufacturers have to view digital transformation as a journey, rather than a destination.
Have you ever joined a gym, certain that this time round you’ll definitely get fit? Chances are you or someone you know has done this. You’ll also know just how quickly the self-doubt kicks in. Why is everyone else so far ahead of you? Is your workout routine the right one? Should you change your diet to support your gym efforts?
You thought going to the gym would be easy, but you soon realise you’re not prepared to make all the changes needed. Sound familiar? While this article isn’t about fitness, I see plenty of parallels between the way manufacturers approach the discussion around Industry 4.0 and the average person’s struggle to stay fit and healthy.
Digital transformation doesn’t have to be daunting
I’m sure you’ve seen the headlines. Articles like ‘here’s everything you need to know about Industry 4.0’ and ‘how to transform your business with new Industry 4.0 technology’ are everywhere. While many of them have fascinating insights to share, I get the feeling that they’re more than a little intimidating to the average reader.
Sure, it’s exciting to find out about the possibilities of automation, AI and data; however, you can’t become excited about an end goal when you’re not sure how or if you can reach it. Rome wasn’t built in a day. In the same way getting that six pack overnight is impossible, so too is transforming your business.
Why Industry 4.0 is a journey, not a destination
‘Making the most of Industry 4.0’ is realising that creating a smarter manufacturing business is a journey, not a destination. Let’s be honest; you’ll never reach a moment in time where you believe your business no longer needs to change, upgrade and adapt.
When the first industrial revolution took place, no one thought the processes coming in would last forever – and it’s the same with the fourth iteration. Even if you reach your end goal, by the time it happens, you’ll have set new targets based on even newer technology.
I’m not saying that there’s no point in trying because the goalposts will shift. If anything, it’s more reason to take your first step, then the next and the one after that. Each foot forward will improve your manufacturing processes as you stride towards a more efficient, Industry 4.0 ready factory floor.
Manufacturing needs to be more open to new technology
The sooner manufacturers adopt a ‘journey over destination’ mindset the better. As an industry, manufacturing is already behind the curve when it comes to digital transformation and Industry 4.0 - especially in the Food & Beverage space. It can’t afford to fall behind any further.
There’s so much to be gained by engaging with the technologies enabling Industry 4.0. As well as driving efficiency on the factory floor, manufacturers can use integrated and automated data processes to dramatically improve regulatory compliance. For Food & Beverage businesses, this is a huge opportunity to increase customer trust.
That’s why viewing Industry 4.0 as a journey is vital for manufacturers. You have to focus on each step – applying new technology to your business in a structured way that would make sense even if you never reached your end goal.
You also have to avoid overwhelming those on the factory floor. The idea is to blend people and systems – creating a smarter workforce that achieves more. One of the challenges involved in this is making sure teams have the skills needed to work alongside the machines. Training is often overlooked, making the Industry 4.0 journey more difficult than it needs to be.
Just imagine the scenario: you introduce new systems, but fail to make sure your workforce has the skills to make the most of them. Nothing works as efficiently as it should and, eventually, everyone goes back to the manual processes they were used to with a negative perception of Industry 4.0 technology. If anything, this is a step backwards, but one you can avoid by ‘upgrading’ your workers alongside your systems.
The first step all manufacturers need to take towards Industry 4.0
Every journey begins with a first step, but what does that mean for manufacturers? To my mind, your first step is to implement a Manufacturing Execution System (MES) that meets the needs of your factory floor.
An MES provides you with all the data you need to continue your journey towards Industry 4.0. It does this in real-time, giving you complete visibility of your business and its processes – as well as the insight you need to identify areas for improvement. With this in place, it almost doesn’t matter what you think your next step is – the data will tell you. You’ll have a clear path ahead of you; one that sees you constantly improving processes as you work towards your end goal.
Implementing an MES can also kick start your business’ digital transformation, which – coupled with the right implementation approach – will start to win over your teams on the factory floor. Engaging the operators, giving them a voice, and empowering them with information that makes action unavoidable clearly demonstrates that people and technology are a winning combination that can dramatically improve performance.
What you need is a simple and structured program that will start you on your journey, and make the implementation of further useful technology (such as wearable tech, smart energy monitoring or the use of drones to perform inventory turns) much easier. By integrating new systems with your MES, you can ensure the improvements keep coming. This is the basis of a smart factory run by a smart workforce.
The first step is the hardest – the rest is simple
While Industry 4.0 might seem unsettling to manufacturers, it doesn’t have to be. Even if your factory floor is behind the times in terms of technology, there’s nothing to stop you catching up – and quickly – if you approach the challenge with the right mindset.
By viewing Industry 4.0 as a journey, rather than a destination to be reached and settled in, you will discover a variety of ways to improve your business. You’ll also free yourself up to focus on driving performance on your factory floor without the fear of failing to meet unrealistic expectations.
Now’s the time to start out on the path towards Industry 4.0 success. There might be plenty of work to do before you reach your end goal, but you’ll never get there if you put off making the required changes. Just as you can’t achieve fitness without going to the gym, you can’t take the last step towards creating a smarter factory if you don’t take the first. Ready to shape up?
James Wood is a Director of Business Development, EMEA & APAC at Aptean.