Paving the way for Industry 4.0
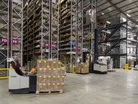
Industry 4.0 has been a buzzword for the manufacturing industry for some time now. Industry experts have described this movement as the fourth industrial revolution which is changing the very nature of manufacturing. Companies are now being presented with the challenge of updating and transforming their existing technologies and capabilities in order to keep ahead of the competition.
As technological developments continue to dominate society, it was inevitable that digitalsation was going to impact the way products are manufactured. The integration of digitalisation and data exchange into the manufacturing process has led to the rapid growth of what are known as smart factories. Within these factories, cyber-physical systems play an increasingly significant role alongside human counterparts. The manufacturing industry is changing once and for all, meaning that manufacturers can no longer simply make physical products but must also find ways to create additional value for customers. This additional value can be achieved through increased connectivity and data capture and analysis.
While this transition is hugely exciting, it can also be quite a daunting prospect for some manufacturing companies. Research by the Institution of Mechanical Engineers in 2016 revealed that there is “a gaping hole” in British manufacturers’ understanding of Industry 4.0. While the creation of these smart factories will inevitably lead to improved and more efficient production facilities, UK manufacturers must adapt their systems now. Time is of the essence and manufacturers must respond to their customers ever-changing demands in an ever-developing technological society.
At Essentra Components, we are just beginning our Industry 4.0 journey. As a leading global manufacturer and supplier of essential components, we understand the need to align our existing systems with these new technological advancements. Incorporating this new manufacturing concept in to our processes will revolutionise our approach to manufacturing and allow us to continue to deliver quality products to our customers with increased efficiency. As part of this transition into Industry 4.0, Essentra Components is incorporating levels of connectivity in to our injection moulding machines. This digitisation drives efficiencies throughout the entire supply chain, resulting in lower costs and significant time savings. For example, the implementation of an online customer order platform means customers can place orders on demand 24hours a day. This process speeds up the digital prototype procedure, enabling Essentra Components to provide customers with high quality samples quickly.
Not only does this digitalisation process benefit the production systems but it can also deepen the customer’s understanding of the whole manufacturing process. We have been able to share production data via the cloud while also sharing stock and future planning information which ensures complete transparency across the entire supply chain. This new technology ensures we are responding to customers’ behavioural changes whilst still ensuring maximum product quality.
Looking to the next steps of our Industry 4.0 transition, Essentra Components has already begun planning the next phase of integration of cutting-edge technology. We are moving towards complete digitalisation of product data and key manufacturing processes, as well as process controls. As part of our long term planning strategy, we want IoT to be at the heart of our business. Through Essentra’s existing cloud, each physical system will register key information and then pass that data onto the next step in the process. This all forms part of Essentra Components long-term investment strategy and will eventually allow it to develop a complete end-to-end supply chain.
Moving towards an Industry 4.0 model was never going to be a simple transition and it will take a significant amount of time to ensure these new processes have been successfully implemented into daily manufacturing processes. But once effectively in place, both manufacturers and customers can reap the benefits of this digitalisation and creation of smarter factories. With multiple sites, hundreds of production lines and 30,000 products across the globe, it is essential that Essentra Components remains at the forefront of this industry transition. While the journey may be a long one, the key to success is recognising the way digitalisation, automation and data collection is completely changing our manufacturing processes once and for all.
By Scott Fawcett, Divisional Managing Director at Essentra Components
For more information about Essentra Components, go to www.essentracomponents.co.uk