Top 10: Uses of IoT in Manufacturing
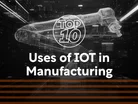
Industry 4.0 continues to transform manufacturing operations.
Among the many innovative technologies that have emerged, one in particular has come to have the most diverse manufacturing applications: IoT.
Though difficulties have surrounded its integration with operational technology, IoT has on the whole had a transformative impact.
It's enabled manufacturers to unleash the full potential of data, enhance connectivity throughout the supply chain and improve overall efficiency and productivity.
How has it done this? Read on to discover the top ten applications, ranked, as we shine a spotlight on the manufacturers leading the way.
10. Remote monitoring of manufacturing operations
Remote monitoring is one prominent and valuable application of IoT.
By connecting systems, sensors and machines via the internet, IoT enables manufacturers to keep an eye on operations wherever they are.
This extends to tracking production lines, machine health and overall performance in real time. The constant flow of data helps manufacturers optimise processes, identify inefficiencies and detect problems early, ultimately leading to less downtime and greater efficiency, in an approach that gives manufacturing leaders greater flexibility and oversight.
Manufacturer Danfoss is a big proponent of remote IoT monitoring, utilising its Alsense IoT Cloud to enhance manufacturing operations.
9. Automation of production processes
By linking machines to a centralised monitoring and control system, IoT can help manufacturers completely automate their production processes.
This works through sensors and actuators that assess various stages of production and trigger real-time automatic adjustments, reducing the need for manual intervention.
Automating production processes leads to greater precision, speedier production times and reduced human error.
All these results elevate the overall productivity and efficiency of manufacturing environments.
An example of a manufacturer leading on automation is Henkel with its state-of-the-art, fully automated Laundry & Home Care Warehouse based in Montornès del Vallès.
8. Quality control
Quality control is of paramount importance in manufacturing environments.
In certain verticals like pharmaceutical, food & beverage and chemical manufacturing, insufficient quality control can have severe financial and legal repercussions.
To mitigate these risks we have IoT, which today plays an essential role in many manufacturers approaches to quality control.
IoT-based sensors and cameras are used to continuously monitor product quality and different stages of the manufacturing process. IoT systems can detect deviations and alert operations to quality issues, by capturing data on alignment and temperature parameters.
Subsequently there are fewer defective products, leaving manufacturers confident they can meet customer expectations and industry standards.
Food and beverage manufacturers like Diageo use IoT throughout their quality control process, to ensure product consistency and efficient production.
7. Product lifecycle management
What it means to manage a product's lifecycle has change a lot in manufacturing.
With growing sustainability concerns its expanded beyond the factory to the broader supply chain, with manufacturers responsible for how their products are used and disposed of.
IoT has helped to make this lifecycle more sustainable, tracking products from development through to end-of-life.
By collecting data at every stage of production, distribution, and even usage by customers, manufacturers have been able to better optimise, recall and update products.
The subsequent collected data helps elevate future designs, reduce waste and enhance customer satisfaction.
One manufacturer who cares deeply about its product lifecycle management is BASF, using the latest technologies to track and augment the process.
6. Predictive maintenance
Predictive maintenance is an especially innovative use of IoT, enabling manufacturers to avoid unplanned downtime, lower maintenance costs and extend equipment lifespan.
It works by monitoring machine equipment and predicting potential failures before they happen, collecting and analysing vibration, temperature and operational data.
One manufacturer leading on predictive maintenance is John Deere, which has embraced it to enhance the maintenance of its tractor and equipment offerings as part of its broader servitisation strategy.
5. RFID tracking for materials and products
Another interesting application of IoT in manufacturing is using RFID (Radio-Frequency Identification) technology to track materials and products as they move through the supply chain.
This use is growing as manufacturers seek to achieve greater supply chain resiliency and strengthen their relationships with vital partners and vendors.
It works by using RFID tags, which are attached to items and communicate with IoT-enabled systems, from this the manufacturer receives real-time updates on product inventory levels, location and status.
This ensures efficient inventory management, reduces the risk of stockouts and optimises logistics.
One global manufacturer successfully utilising RFID technology is Amazon, inspired by the success stories of retail leaders like H&M, Walmart and Zara.
4. Digital twin technology
IoT enables the creation of digital twins, virtual models of physical systems.
These digital replicas are constantly updated with real-time data from IoT sensors, allowing manufacturers to simulate and analyse operations without disrupting actual production.
This technology helps optimise processes, test new scenarios and improve decision-making.
Manufacturers like Siemens and Dassault Systemes are leaders in digital twins.
3. Environmental monitoring
IoT also has the capacity to make manufacturing environments more sustainable and comfortable for workers.
Through IoT sensors, manufacturers can monitor environmental conditions such as air quality, temperature, humidity and emissions in facilities.
The real-time data enables them to adjust heating, investigate hazards and identify issues with air quality, making the workplace safer and more environmentally friendly.
This also better enables manufacturers to meet environmental regulations and respond in a timely manner to potential hazards.
For pharmaceutical manufacturers like AstraZeneca, who need to maintain consistent, controlled temperatures for drug manufacturing, IoT has had a significant impact.
2. Smart energy management systems
One of the most valuable uses of IoT is its capacity to enable smart energy management.
Smart energy management refers to systems that track energy usage across facilities, optimising power consumption by automatically adjusting energy flows.
Sensors identify inefficiencies and areas for improvement by monitoring equipment, while IoT platforms enable real-time adjustments to reduce waste.
This saves manufacturers costs, makes operations more efficient and massively enhances their sustainability.
ABB is a leader in this field, as an industrial automation leader dedicated to the clean energy transition.
1. Augmented reality integration
Now for our top application of IoT we have something that covers training, design and engineering.
By integrating IoT with augmented reality systems workers can access real-time guidance during assembly or maintenance tasks. These technologies can be combined through smart glasses which enable workers to see data overlays on physical objects that provide vital data and history information.
IoT and augmented reality integration enables manufacturers to access and interact with digital twins of assets or factories, fundamentally changing approaches to design and engineering.
Overall this integration helps to improve accuracy, reduce training time for new workers and speed up complex manufacturing tasks.
This is our top use because of its capacity to shape every aspect of product development, machine and factory maintenance and the management of the broader supply chain.
Deloitte and Amazon have recently unveiled their own augmented reality training solution for manufacturers that adopts these integrated technologies.
All in all, IoT is helping to positively transform manufacturing environments, making processes more efficient, cost-effective and reliable.
If you haven't evaluated where IoT could help in your operations, now is the time.
Make sure you check out the latest edition of Manufacturing Digital and attend the next Manufacturing LIVE event - Manufacturing & Mobility LIVE (virtual)
Also sign up to our global conference series - Procurement & Supply Chain 2024 & Sustainability LIVE 2024
Manufacturing Digital is a BizClik brand.
- Manufacturing in 2025: A Virtual, Interconnected WorldDigital Factory
- Microsoft, ABB & Chevron: How to Scale Smart FactoriesAI & Automation
- Manufacturing Unwrapped: BASF, ABB & Chemical CircularitySustainability & ESG
- Manufacturing Unwrapped: Impact of American High-Speed RailProduction & Operations