Unlocking traceable and efficient manufacturing supply chains
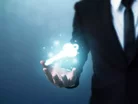
Axel Schmidt, Senior Communications Manager at ProGlove, discusses the ways manufacturers can unlock efficiency and traceability within the supply chain.
With increasing regulation across all industries, from data privacy legislation to technical specifications and product certification requirements, consistent traceability within often large and complex supply chains has never been more important for businesses to achieve. This is not only for compliance reasons, but also to ensure accurate forecasting so companies can deliver on promises made to customers.
Traceability ensures a stringent flow of data so that suppliers and manufacturers can provide detailed information about what happened to a product, by whom and at what time. This is essential for industries such as the automotive industry, that may have to recall a model due to a defect, or in the food industry where traceability is vital to ensure food safety standards are upheld. But as industries move towards longer and more fragmented supply chains, how can businesses keep up with increasing demand for faster product turnaround combined with a growing need for traceability? Axel Schmidt, Senior Communications Manager, ProGlove, explains how wearable technology such as barcode scanners can help to streamline supply chain processes and keep quality at optimum levels – not only addressing the need for traceability, but also transforming worker efficiency levels.
Increasing complexity
With new legislation coming into effect, along with consumer demands for a wider range of products, manufacturers will be required to handle and process an increasing number of parts and components for assembly. This can present increasing challenges for businesses, especially those that operate with complex product variants and short product life cycles which can block the possibility of a fully automated facility.
In addition, the rapid growth of e-commerce business models may have simplified the retail world for consumers, but in turn has increased the volume of work for vendors – by as much as five times according to research. As businesses move closer towards Just-in-Time supply chains, the focus and pressure is firmly placed on logistics operations to deliver efficiency within the supply chain. Moreover, the number of shipping formats available creates an added roadblock to automation and the surge in demand for rapid fulfilment that comes hand in hand with peak periods only adds further complexity.
Consequently, there is an increasing need for organisations to seamlessly document what they do and how they do it to meet compliance requirements. But this must not be at the cost of adding any additional time to the already tight schedules organisations need to adhere to in order to remain efficient and competitive.
Augmenting the workforce
In order to meet compliance needs and unlock crucial efficiencies that can help businesses to meet fluctuations in increased demand, organisations need to be able to access and capitalise on real time data. Research from IDC predicts that more than a quarter of data created will be real-time in nature by 2025, and this is where barcode scanning plays a fundamental role.
The concept of barcode scanning within the supply chain has been around for some time, enabling companies to increase visibility by tracking items along the product journey from manufacturer to the end point. Yet, the use of a conventional pistol scanner is fraught with challenges, such as the significant time lost for each worker due to the repetitive nature of picking up, using and holstering the scanner for each individual item.
Given the format of the traditional pistol scanner, the devices are also liable to breakages as they are easily dropped to the floor. And as the devices are not ruggedised, replacements are regularly required.
SEE ALSO:
This unreliability can be frustrating for workers as well as the organisation, as workers cannot operate with optimum efficiency. Another drawback of the pistol scanner is that it can be easily lost by workers. This could be around the warehouse or factory but it’s also possible that a worker may leave the scanner inside one of the boxes that they are packing. This is an unexpected surprise for the customer, to say the least, but results in economic losses for the company and further replacement scanners required.
Instead, wearable technology with in-built scan functionality can deliver a number of benefits to address these challenges. Minimising unnecessary and tiring repetitive actions and improving accuracy significantly increases the volume of work undertaken by each worker. With adjustable feedback options, such as acoustic signals, vibration and LEDs on the back of the hand, a worker receives immediate confirmation of correct product selection. This feedback not only minimises delays and errors, improving productivity, but also avoids worker frustration.
Display screens can also be connected to wearable terminals to provide workers with additional information, such as the location of the next pick. Unnecessary activity is removed as every movement is directly related to the task at hand. Through this augmentation of the workforce, efficiency can be rapidly transformed.
Legislation, technical evolution and customer demand create an urgent necessity for accurate and efficient barcode scanning to deliver traceability and efficiencies within the supply chain. Organisations must therefore consider the need to implement solutions that streamline these processes whilst keeping quality at optimum levels.
Supply chains will continue to get longer and more complex, and many retailers face the challenge of fulfilling their promises to their customers. In addition, fragmentation of supply chains is also on the rise, with a number of suppliers and components relied upon to work in harmony to make the entire supply chain function. Wearable technology can be a critical link to deliver productivity and efficiency and allow organisations to quickly adapt to fluctuations in demand, giving them a much needed competitive edge.
For more information on manufacturing topics - please take a look at the latest edition of Manufacturing Global.