5 minutes with Alessandro Piscioneri on Comau’s robotics
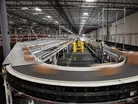
Hello Alessandro, what brought you to this industry?
“I have always had a passion for industrial automation and software development. Already during my studies, where I received a degree in Computer Engineering from the Turin Polytechnic, I was fascinated by the world of robotics and automation. In the following years, I had the opportunity to join Comau and pursue a second Master's degree in Industrial Automation, also at the Polytechnic of Turin.”
What is Comau and what are the advanced systems and products developed for industrial automation?
“Comau is a world leader in the development of advanced systems and products for industrial automation. It helps companies of all sizes and industry segments to harness the potential of digital manufacturing by combining innovative engineering solutions with enabling technologies and 'open', easy-to-use automation. The company's comprehensive portfolio includes: joining, assembly, and machining solutions designed for traditional and electric vehicles; robotic manufacturing systems; a complete family of industrial robots (including collaborative and wearable robotics solutions) with a wide variety of models and multiple payload configurations; and advanced robotics solutions for the most complicated use cases, integrating industrial robots, vision systems, and artificial intelligence (such as advanced solutions for solar panel power plant installation). The offering also extends to project management and consulting, IoT services as well as maintenance and training, for a wide variety of industrial segments.”
What is zero-emission energy automation?
“Automation facilitates the process of zero-emission renewable energy generation, making much higher production volumes possible than those without automated technologies. For example, automation plays a key role in terms of increasing battery production capacity and ensuring better battery integrity/performance.”
How does Comau use hydrogen?
“Comau does not actually use hydrogen but works with several customers in various parts of the world to automate the production of fuel cells and electrolysers. It should be noted at the outset that the assembly and production of electrolysers and fuel cells tend to be slow, expensive and labor-intensive. Comau is working to industrialise these processes by developing a proprietary portfolio of solutions that can automate key manufacturing steps, including cell preparation, stacking, compression, welding, leak testing and more. This will enable energy suppliers to scale production volumes while increasing the quality of the high-precision process.”
Alessandro Piscioneri, Comau's Global Head of strategic Marketing for Robotics, Digital and Non automotive business
Tell us about the crucial role of automation.
“Automation is important for several reasons. The first reason is related to the architecture of a fuel cell. The core, known as the fuel cell stack, consists of hundreds of repeating elements (100 to 300 cells per stack), while the cells themselves are composed of several layers - 2 to 4 per cell, based on experience to date. This inherent repetition is a key factor in automation, leading to cycle times of 1-10 seconds per layer (depending on the product and plant throughput) during which each layer is picked up, quality-checked, and placed correctly in the stack. The high levels of precision and quality required during the assembly process are another reason why automation can help improve fuel cell production. First, each cell must be aligned to a tolerance of 0.1 mm, and each component and layer is checked for geometric and surface defects. Most manufacturers require full traceability of the process, and until a stack is sealed, many fuel cells require compliance with cleanroom standards.”
What do the next 12 months hold for you and the company?
“Looking ahead, research and development will continue to be heavily focused on future generations of batteries and hydrogen-based energy sources. We will see the need for longer vehicle range, faster refueling or charging times, improved safety, reduced costs, and a greener production chain (from raw materials to recycling) grow, and all of this will drive many changes and new products.
“To meet these needs, Comau will continue to develop cutting-edge hydrogen-related technologies while strengthening its ability to provide electrification solutions, where currently the greatest investments are concentrated in the transportation area. A recent example is the flexible battery module production line that Comau is developing for next-generation 8- and 16-cell battery modules at the Automotive Cells Company (ACC) Gigafactory in Billy-Berclau Douvrin, northern France. The line, which is designed to produce up to 8 GWh per year by the end of 2024 with an estimated production rate of 53 pieces per hour when fully operational, will enable ACC to help create a European-based battery ecosystem covering the entire value chain.
“As far as Comau is concerned, in the coming months we will continue to offer automated solutions to meet the production needs emerging in new markets. In fact, the demand for automation is growing in almost all industrial sectors, and our company, thanks to 50 years of experience in the automotive industry-which is the industry with the greatest complexity and technological density-can provide customers with consolidated know-how and continuous investment in research and innovation. We already have several projects under development for example in the field of solar panel installation, logistics automation, in addition to the fields already mentioned, such as electrification and hydrogen.”