Bridging the skills gap in automotive manufacturing
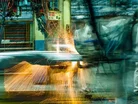
Automotive manufacturers are currently facing a series of challenges. With increased pressure to meet customer demand for more personalised designs, they are tasked with creating a more flexible production environment, reducing engineering time and costs, and accelerating speed to market if they are to remain competitive.
In addition, like other industries, automotive is looking at a global skills shortage, in which too few engineers are sufficiently qualified to operate sophisticated automated machinery and equipment, or support the advancements available via emerging technologies.
In some cases, robots can carry out an engineer’s tasks; however, few factory floors can rely entirely on robots. Where robots or automated machines are utilised, skilled workers are still required to oversee operations and provide instructions to the robots.
To date, the Internet of Things (IoT) and machine-to-machine interfaces are not predicted to fully replace the hands-on benefit a skilled engineer delivers.
Skills shortage
A number of industry reports have identified a lack of qualified individuals with the required skillset for today’s technology-centric world.
For example, according to forecasts made in the 2017 Engineering UK: The State of Engineering report, 186,000 people with engineering skills are required each year from now until 2024 to meet manufacturing needs. Today, in 2017, the demand for engineering graduates currently outstrips supply; the report indicates an annual shortfall of at least 20,000. Reports such as this do not predict what impact the UK leaving the EU will have on the requirements of the manufacturing industry.
In the US, the situation is similar, as detailed in a report by Deloitte which projects that 3.5 million manufacturing roles will need to be filled by 2025, of which 2 million are predicted to be affected by a lack of skilled workers.
Reasons behind the shortages
While ‘skills shortage’ is an issue far wider than the automotive industry, reasons can be identified why this sector has a lack of skilled workers.
Qualified engineers, for example, frequently leave their areas of expertise to pursue what they believe to be a more lucrative career in a different field, such as finance. Those who do remain true to their specialism, however, may choose to work in an area outside of the automotive sector.
There’s also a question of perception.
Smart factories are replacing more traditional production facilities, with advancements around newer processes such as 3D printing continually pushing the limits of conventional manufacturing. As a result, employees can spend more time using a computer rather than hands-on with “traditional” manufacturing equipment.
It appears that public perception hasn’t advanced at the same speed and technology has evolved, with some people imagining a career in manufacturing as it was one or two generations ago; with decent-paying jobs involving long assembly lines, manual labour and loud machinery. By way of illustration, a 2016 study in the US revealed that 71 percent of young people don’t see manufacturing as a high-tech career choice.
By dispelling such age-old misconceptions, and enlightening a new generation of employees what modern manufacturing really involves, we can begin to close the skills gap and inspire people to pursue high-tech and high-paying careers within the industry.
Technology is the answer
Companies today need people who can adapt to – and evolve with – ever changing technology. Whether automotive or otherwise, manufacturers have recognised the importance of creating a workforce of intelligent problem solvers. In addition to this, more manufacturers are now focusing on hiring and training talent that’s able to keep up with advancements—and drive investment—in technology.
If suitably qualified individuals aren’t available to employ then, in certain circumstances, automated software can provide an alternative solution. Technology-driven 3D printing, CNC machining, and injection moulding technologies, for example, can assist in-house engineers and designers with product requirements and, by enabling digital manufacturing processes, reduce a project’s time to market.
Technological solutions, such as automation software that generates design for manufacturability analysis, can relieve the pressure on engineers by supporting the entire production process. Digital manufacturing technologies offer speeds that meet – and often surpass – customer demands, with parts produced on-demand within a matter of days.
While the automotive industry may be facing some challenges, digital manufacturing and technological progress are enabling automotive engineers to deliver products to market faster than ever before. This is easing the competitive pressure on car manufacturers, and going some way to fill the void left by the shortage of skilled engineers.
By Stephen Dyson, head of Industry 4.0, Proto Labs