How They Produce Multiple Drive-Types at Porsche Leipzig
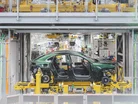
It doesn't take an expert to see that the automotive sector is undergoing significant transformation.
From EV innovation to embracing technologies like automation and AI, automotive manufacturers are both adapting to and creating the future of mobility.
One area critical to this transformation is the rise of multi-OEM production and assembly. As the automotive market segments and changes, annual volumes per vehicle and model runtimes are shrinking.
This makes assembly a more costly process, a fact that can be remedied by assembling multiple models on one joint production line.
Multi-OEM assembly is no simple task, especially with the complexity and diversity of modern vehicles. This is reflected by the contemporary transformation of the term 'platform' in automotive manufacturing.
This term once described the common technical underbody on which various body-in-white derivates could be realised.
Today it breaks down further into the Geometric Platform, which includes the car body's common structure and pick-up points and the Electric Platform which has key features in End-of-Line testing.
But why is multi-OEM assembly so complicated?
Multiple drive-types on a single production line: what's the challenge?
Producing multiple drive types-like internal combustion engines (ICEs), EVs and hybrid cars-on a single assembly line is challenging for six key reasons.
1. Supply chain complexity
Because each drive type involves different logistics and suppliers, coordinating and delivering parts on time grows more complex. Precise planning is required to avoid delays and manage inventory.
2. Varied assembly steps
Assembly processes differ significantly for each drive type. EVs require large battery packs and electric powertrains, whilst ICE vehicles involve exhaust assemblies and fuel systems. To integrate these distinctive parts into one line, equipment and assembly processes must be reconfigured to enable greater flexibility.
3. Quality control variations
Across a production line, ensuring consistent quality is vital. But this is a challenging process when working with different systems that require specialised testing and quality checks. For example EVs often need extra testing for electrical safety and battery integrity. The procedures required for this can increase wait times.
4. Line downtime and reconfigurations
When switching between different drive types, manufacturers encounter the risk of downtime. This is because stations and assembly line tools, from conveyor belts to robots must be adjusted, adding time and possible inefficiencies.
5. Different component needs
Each drive type has unique components, like electric motors for EVs and engines for ICEs and complex systems that combine both for hybrids. Integrating these distinct parts can be challenging and time consuming, requiring the same integration needed at assembly.
6. Specialised workforce skills
Workers on the line need a range of skills to handle different drive systems. While ICEs require expertise in mechanical engine components, EVs involve high-voltage systems and complex electronic components. Training workers to handle all types safely and efficiently adds to production challenges.
One manufacturer that is excelling at manufacturing multiple-drive type vehicles on a single production line is Porsche.
By embracing automation and innovative robot technology, the automotive leader has brought the all-electric Macan into its dominant production line.
By exploring the success of its production plant in Leipzig, other automotive manufacturers can learn vital insights about how to effectively integrate multiple-drive types and enhance overall processes.
A triumphant marriage
Within the Porsche blog that explores the success of it's production plant in Leipzig, the process of vehicle manufacturing is compared to a marriage.
A marriage that had to be reinvented at at Porsche Leipzig to maximise results.
At the centre of this marriage was the union between the body of a Porsche Macan and its all-electric powertrain chassis, brought in by a driverless transport system.
Making this union successful was critical at the plant, where three different drive concepts-gasoline-driven, electric vehicles and hybrid vehicles- are manufactured on a single production line.
Producing near 600 Panamera and Macan cars daily for customers in this way, The Leipzig production line is described as unusually 'efficient, complex and multifaceted'.
Head Engineer Sebastian Böttcher notes that the plant is: " Like clockwork, just on a different scale.”
Achieving this result has been a lengthy journey, beginning in 2016 when the Porsche Executive Board decided to produce the all-electric Macan in the Leipzig factory.
Production that runs like clockwork
Due to production limitations, Porsche decided the Macan had to be produced on the existing production line which had been reserved for vehicles with a hybrid drive or combustion engine.
“We soon realised we would have to completely revise the existing marriage and many other workflows at the plant,” says Böttcher.
“An additional type of powertrain is like a little world of its own, with new requirements, special procedures, and special tools. We had a lot of learning to do.”
A key challenge they faced was differing component needs. A gasoline-driven or hybrid vehicle requires 20 screws to secure its underbody and chassis.
EVs by contrast require 50, a change which created additional steps and work on the same assembly line.
- 50,000 square meters
- 3.6 kilometers: the distance covered by a vehicle on the line
- 331 (work) cycles per vehicle
- 2 product lines on which currently three drive concepts are assembled
- 5,000 parts assembled on the vehicle during pre- and final assembly
- 4,000 work steps per vehicle
To solve this issue, Sebastian Böttcher and his team turned to expansion and automation. The four assembly stations they had grew into nine, and six additional robots and 18 automatic screw stations we added.
Porsche worked with external partners to develop an automatic screw leading system capable of handling a diversity of screw sizes, shapes, torques and angles at high-speeds across a range of fittings and product lines.
The manufacturer also develop a specialist camera system which autonomously examines the surface of its EVs high-voltage batteries for foreign objects like nuts or mislaid washers.
The company has also developed a measuring device, that passes along the assembly line to evaluate screw spindles during ongoing production operations.
This device dramatically reduces delays and idle time, and currently has its patent pending.
“All in all, we have created a highly productive system which has been seamlessly incorporated into all the plant workflows,” Sebastian Böttcher adds.
“There’s obviously always things that need optimising, but that’s standard procedure for us at Porsche.”
The pearl necklace approach
Core to Porsche's success at integrating multiple drive types on a single production line is its philosophical approach to production.
“The pearl necklace principle has a key part to play in everything we do here,” says Denny Schubert of the Vehicle Control Systems department.
The pearl necklace principle emphasizes order and precision, with employees according to Denny working to: "precisely manage the order in which the vehicles are processed, lined up like on a string of pearls."
This means utilising employees effectively, minimising warehousing and presorting parts.
At Porsche, this is a concept that ensures effective employee utilisation, minimizes warehousing, and perfectly presorts the parts and sends them to the assembly line at the right time. The plant plans ten days ahead, enabling suppliers to precisely coordinate production and supply with the needs of the assembly line.
When manufacturing a diversity of vehicles with different component and testing needs, this coordination is critical to ensuring smooth production.
“Producing three different powertrain types on a single line is demanding for everyone at the plant. Our work is highly complex,” says Martin Reinbacher of Industrial Engineering.
“We have to plan in a very networked and interdepartmental way in order to come up with efficient solutions. But we see this paying off every day.”
The pearl necklace informs Porsche's ability to run its production line 'like clockwork' emphasizing forward-planning, precise coordination and effective management.
The company demonstrates that organisation is the overarching challenge when it comes to assembling multiple-drive types on a single production line.
Manufacturers seeking to do the same must invest in their staff, facilities and capacity for long-term planning, intimately understanding the unique engineering needs and challenges of differing vehicle types.
Doing so will ensure a bright future, in an automotive sector where vehicle choice and flexibility is a growing consumer and production concern.
Make sure you check out the latest edition of Manufacturing Digital and also sign up to our global conference series - Manufacturing & Mobility LIVE
Manufacturing Digital is a BizClik brand
- Volvo & Dassault Systèmes: Simulating Our Automotive FutureDigital Factory
- BMW Drives Emission-Free Battery Transport With EV TrucksSustainability & ESG
- Automotive Buyers Seek AI Integration, Not Costly Add-OnsAI & Automation
- DHL Supply Chain & Diageo Drive Change with Hydrogen TrucksProcurement & Supply Chain