The impact of automation on equipment reliability
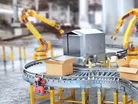
Bryan Christiansen is the founder and CEO of Limble CMMS. Here he discusses how automation can support maintenance operations, data management and quality control.
Reliability deals with the availability and the ability of equipment to function effectively and affordably. It is vital for estimating the risk of failure and the productivity of equipment throughout their useful life. To quantify the reliability of equipment, organisations take into account metrics such as mean time between failures (MTBF) and overall equipment efficiency (OEE). These are data-intensive metrics that require continuous monitoring of equipment operating conditions.
Automation boosts the efficiency of processes and equipment while enhancing the management of operations and maintenance data. There are several ways for organisations to automate their equipment depending on the complexity of processes, safety risks involved, plant layouts, etc. They are:
- Numerical controls (NC) and computerised numerical controls (CNC)
- Programmable logic controllers (PLCs)
- Industrial automated robots
- Computer-aided manufacturing (CAM)
- Silicon-based automation chips
Below are some of the ways that automation impacts reliability by simplifying maintenance operations, data management, and quality control.
-
Automation and maintenance
The evolution of production equipment and technology continues to transform production facilities into advanced units that require minimal human intervention. The focus is on limiting process and equipment downtime through the strategic implementation of predictive maintenance. Automated systems fitted with sensors and condition-monitoring utilities capture the operating conditions of equipment in real-time. Analysis of this data, which is relayed through the internet of things (IoT), enables the maintenance teams to identify, in advance, the defects or errors that can cause stoppage of processes or damage to equipment.
Highly automated systems incorporate several sensors and devices which require care when handling or maintaining. The additional devices can complicate maintenance operations by increasing the number of inspection and inspection points. By using condition monitoring sensors, technicians can pinpoint and isolate the exact defective part of the equipment that requires correction or replacement.
Access to accurate equipment data enables organisations to optimise their operations, establish safety standards, and improve the useful life of critical equipment. The data collected is stored on dedicated servers or cloud platforms for future reference. The data is vital for performing root cause analysis (RCA), failure mode and effect analysis (FMEA), and evaluating the reliability of critical assets.
On the side of organising and executing actual maintenance work, computerised maintenance management systems (CMMS) play a crucial role in automating maintenance tasks. They guarantee sufficient and timely maintenance of all equipment. The software can integrate with sensor and predictive analytics to generate alerts for corrective and routine maintenance tasks, keep a lifetime log of maintenance operations on every piece of equipment and reconciles spare parts and tool inventories. That way, the company ensures that assets are available throughout the production cycles and that they operate optimally.
-
Automation and data management
Manufacturers dealing with expensive and sophisticated equipment like aerospace engines, modern automobiles or advanced manufacturing systems may have fewer units in operation with little information on the actual performance of the equipment. Such organisations rely on cloud technology to create a digital replica of the physical equipment. The physical equipment is equipped with sensors that relay its actual operating characteristics to its cloud-based equivalent.
Upon receiving this data, machine learning techniques and algorithms extract any relevant operational data. Through this exchange of data, the manufacturer can identify the suitable operation patterns and the common anomalies affecting the operation of the physical equipment. This technology, also referred to as digital twins, enables manufacturers to optimise equipment at production and maximise their reliability.
By leveraging cloud technology and IoT platforms, organisations using advanced production equipment can collaborate with the development teams in real-time and perform remote troubleshooting or repairs. In return, the organisations can keep their operations running and retain a higher reliability score. On the other hand, the manufacturer gains more data and insights needed for improving the quality of production equipment.
-
Automation and production systems
Production entails several repetitive processes which are tedious if performed manually. Human operators are prone to fatigue and errors that lead to the production of defective or low-quality products. By automating production systems, organisations maintain production conditions like feed rate at a constant level. While this is important for quality control, it also plays a role in enhancing the reliability of equipment.
The automated systems keep an accurate production log. With this data, the organisation can evaluate the efficiency of its processes and identify instances that cause breakdowns or a dip in productivity.
Final thoughts
By automating equipment, companies can improve the quantity and quality of their products. Most automation systems facilitate the collection and storage of production data over time.
They also minimise instances of human errors that increase the probability of process or equipment failures. Access to accurate data enables maintenance teams to perform the correct maintenance activities and proactively eliminate defects causing recurrent downtime. Proper maintenance, optimum availability and affordable operations costs contribute to reliable systems.