Capgemini: UK Manufacturing and Reindustrialisation
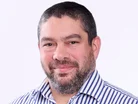
Why is now a particularly uncertain time for UK manufacturing?
It is an uncertain time for UK manufacturing. There are many questions circulating: why should we invest? What should we invest in? Will this lead to a return on the investments made, an increase in sales, market share, or a more certain delivery adherence? Fundamentally, how can we be more resilient in the supply of products and services to the customers and consumers, when supply chains have so much volatility in them? Operations in the UK, Europe and US are increasingly expensive, for a given level of productivity/automation, from energy (and transition) costs, stagflation, supply chain competition, materials sourcing, quality control, regulatory changes, staffing shortages, environmental concerns, and shifting geo-politics. If you're the plant lead or Chief of Operations, I wouldn’t be surprised if you’re not getting much sleep.
How can the manufacturing industry meet increased demand from reindustrialisation?
The UK is a leading and integral part of the global manufacturing economy. Maybe we don't do high-volume, low-margin production, but we're brilliant at high-end complex products: whether that be luxury goods, vehicles, construction equipment, vaccines/medicines, or defence equipment. We are at an inflection point where the UK manufacturing industry must step up to meet cost pressures, mitigate fluctuating global demand, and capture new markets and customers. To scale up, we cannot scale linearly based on today's factories and processes. We need to think differently, be more creative, and embrace new technologies to deliver high capacity at lower levels of ‘hard-to-come-by’ staffing. This represents an opportunity for investment, and the dawn of a fresh challenge in the manufacturing industry to define what the UK is the best at, and what the future will look like. “Made in the UK” carries a special significance. We should continue to be a blend of leading-edge design and traditional craft – augmented even more with cutting edge technology. Only through investment in reindustrialisation do you really get to control this narrative.
Your report says that nearly 20% of the current manufacturing and engineering workforce in the UK will retire by 2026. It also says that to fill that gap, 186,000 skilled workers need to be recruited every year. What does UK manufacturing have to do to achieve this goal?
This is a huge worry, especially in sectors such as life sciences. The continuity in skills may just evaporate. At its simplest level, UK manufacturing must rebrand and rebuild to be a more attractive career than other trades and encourage more UK-based people into the fold. Good wages, good prospects, good working conditions and world-class working spaces must abound. We can also look to automation, robotics, and intelligence-based systems to transform operations, factories, and supply chains to use less critical resources, be more sustainable and socio-economically diverse. In other words, the right people are needed to deliver more capacity, more competitively. The UK has always been a bastion of immigration, so we also need to encourage highly skilled international workers to reside here and share their knowledge.
In your report 63% of UK execs believe they will need to increase wages to retain the manufacturing workforce in the UK. Do you agree and if so,why?
Yes, things must change. It’s difficult to justify why manufacturing wages should be so relatively uncompetitive in the UK, European or US employment markets. People with engineering and digital skills already look to other sectors if they aren’t offered a good employment package with prospects for growth and further reward. To mitigate this, manufacturers can invest in automation, new facilities, and industrial processes, from the large one-off productions to mass-produced high-end luxury goods. This leads to demand for new skills, and there are already pathways available to train and recompense people identified as having the aptitude and attitude for being more than a basic operator. There are some key skills that can't be automated completely, but they can be augmented to increase productivity and quality outcomes (e.g. complex welding). As a UK publicly listed company we can, and must, incentivise investment in high-end manufacturing skills. Collectively our industry must work together across government, business, unions, and skills councils to encourage reindustrialisation investment.
A challenge with recruiting the new manufacturing workforce is a digital skills gap. Companies are investing in emerging technologies but the traditional labour force lacks the skills to adapt effectively. How does reindustrialisation factor into this and what do you think manufacturers should do to address it?
To my mind, reindustrialisation is a strong catalyst for this transformation of skills. You can't reshore and expect to bring low-skill, low-wage processes with you into countries with higher wage rates, energy costs and strict regulatory controls. Reindustrialisation affords an opportunity to reinvent your products, factories, processes, automation levels, and supply chains.
Bringing in technologies such as autonomous operations, AI and Generative AI, Internet of Things (IoT) / Operational Technology (OT), Automated Guided Vehicles (AGVs) and more drives the need to reimagine what manufacturing is, and how we as humans are augmented by these capabilities. It's true that fewer people are needed overall to deliver operations, but each individual person has a significant impact on productivity, cost control and capacity growth through their deeper knowledge of digital-physical processes and techniques. Manufacturers must be open to radical cultural change in operations to unleash the skills and creativity of their workforce. This mandates investment and trust in their ability to deliver growth and drive the new direction of a reindustrialised site.
What does the future of manufacturing post-reindustrialisation look like? How can companies adapt to find success?
It's not a case of “companies can adapt”. It is a case of "must" adapt to stay relevant as a supplier and an employer in the UK. Post-reindustrialisation doesn't mean there is a finish line. It is the next leap in manufacturing capability in the UK and near-shore countries. Three things will likely be true:
- We will have more productivity, resiliency, and agility to adapt and shape market conditions for new market competitive products and services,
- We will have embedded sustainability, energy, and resource efficiency into how we design, manufacture and supply products,
- We will have world leading digital skills embedded across our manufacturing sector, with a diverse cast of talent who can challenge and drive continuous innovation through the merging of digital and physical technologies.
The ‘How?’ comes down to investment and organisational bravery to change, and that's the job of the emerging inspirational leaders in this sector. Starting points could be; automating industrial operations, creating new insight with existing IT- and OT-based data streams, supply chain simplification, and investing in new energy efficient/alternative manufacturing processes. Particularly in the critical base of the manufacturing sector, the small and medium-sized enterprises (SMEs) need access to mentoring, government grants and proven transformation delivery.
What are Capgemini's plans for the next twelve months?
Over the next twelve months our mission is twofold – the first, to help our manufacturing clients create compelling business case investments that drive their UK and international reindustrialisation strategies. And secondly, deliver on these opportunities by bringing their staff on this journey, helping them tangibly experience the "what's in it for me?". I strongly believe that this is a substantial mission with a significant outcome for the UK.
******
Make sure you check out the latest edition of Manufacturing Digital and also sign up to our global conference series - Procurement & Supply Chain 2024 & Sustainability LIVE 2024
******
Manufacturing Digital is a BizClik brand.