Design for Excellence Foundation at TT Electronics
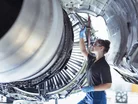
A good product is more than its design. It’s the end-to-end process, including manufacturing, that brings a solid design to market. In the quest for better manufacturing processes – a goal common among producers of engineered systems – Design for Excellence, more commonly known as DFx, is a widely established framework of methods, guidelines and standards for creating better-quality products.
“Ideally, this framework is applied at the concept design phase, enhancing development as early as possible to produce higher quality products, reduce cost and shorten development cycles,” says Sanjeev Katiyar, the Senior Engineering Manager at TT Electronics. “Larger corporate entities expect DFx as a fundamental service from their Contract Electronics Manufacturer (CEM), yet smaller designers may be less aware of its import.”
Katiyar has more than 25 years of progressive experience in the electronics manufacturing space, featuring immersive exposure to both OEM and contract manufacturing. He currently serves as the SMTA Ohio Valley Chapter President.
In his current role at TT Electronics, a global provider of engineered technologies for performance-critical applications, Katiyar leads technology roadmap realisation in six focus areas: automation, PCBA technology, coating materials, material handling, digitiastion and NPI COE.
DFx trends and strategies
Partnership is at the heart of DFx, especially in regulated markets such as aerospace, defence and healthcare.
“It’s not cliché to say that partnership matters in these arenas – adding critical value where OEMs face a deficiency of in-house expertise even as they simultaneously face supply chain and time-to-market obstacles,” said Katiyar. “It’s in this complex and highly volatile landscape that partnership has become its own new frontier, with collaboration proving a powerful design strategy.”
The DFx process not only creates an ideal opportunity to determine and correct issues in new products, but also those related to mature, or already developed products. Because defects, the need for new parts, or the restructure or redesign of a PCB often occur with mature products, DFx can interject feedback that drives the most reliable product.
According to Katiyar, a template for DFx methods could include:
- Goal-specific design methods target different phases of a product’s lifecycle. The “x” is the area of focus, such as product design specs, supply chain and testability
- Lean design processes, utilising lean manufacturing principles to eliminate waste
- Identification of problems and needs
- Analysis of solutions
- Optimisation for efficiency and performance (for example, a shorter time to market results in fewer development costs).
Subcontractor relationships in the electronics industry can reduce costs and shorten development cycles.
“Great engineering design practices start with careful consideration of the product requirements to reduce delays and redesign costs later,” Katiyar said. “Here, you don’t know what you don’t know, and this is where collaboration plays a high-value role. Depth of partnership adds competitive value in the form of reduced costs as well as development timelines.”
Consider that factors such as FDA approval of medical devices or the Size, Weight, and Power (SWaP) concerns common to next-generation defence electronics require unique insight.
“These and many other industry-specific challenges can present unanticipated roadblocks to developing an excellent product, already complex due to the nature of performance-critical applications such as surgical navigation, automation and electrification.”
Any design trade-offs are best determined and planned early in the design process, negotiating the smoothest and fastest path to market. When competitors have more resources and a deeper in-house talent pool, it’s crucial to capitalise on partnerships that can level the playing field.
“Design for manufacture, for test, for supply chain – these all fall under the DFx banner and represent value-added engineering solutions that minimise quality issues and ultimately bring about speed to market,” Katiyar said. “Establishing a cohesive approach that permeates design thinking from engineering to procurement, operations, commercial, legal, marketing and c-suite affects comprehensive value in the design process. This is also how OEMs and product developers can tap into a deep well of industry knowledge they may not otherwise access – and increase focus on time-to-market goals and product longevity as an integral part of their design and manufacturing processes.”
This approach has an impact, not only internally, but also on external forces, such as the global electronics supply chain. Resiliency here can make or break a product design; this is ideally addressed at the earliest stage of development. However, it is partnerships that are the not-so-secret ingredient, effectively supporting redesigns and adjusting schedules by avoiding or eliminating surprises.
“It’s this source of creative and experienced thinking that also mitigates risk in the supply chain with proprietary tools, software platforms and artificial intelligence that can be accessed as needed.”
DFx and subcontractor relationships can impact the manufacturing sector
As the electronics industry faces growth in subcontractor relationships – in contrast to onsite manufacturing resources that may have been more common in years past – Katiyar believes that it is essential to share insight and feedback on the processes between the design and manufacture of a product.
“There are always variables to consider, but DFx increases confidence that products are reliable, testable and facilitates a faster time to market,” said Katiyar. “The DFx framework itself provides the interface between design and manufacture to ensure a smooth transition to production.
“Creating a manufacturing ecosystem built for future advances and product longevity is crucial to the long-term success of any product. Trouble is, it’s not always obvious that these things don’t necessarily exist. It may not be until product testing fails, an upgrade is required, or a supply chain is disrupted that the core elements of a design will be revealed to be unnecessarily complex and costly.”
Here, partnership can make all the difference – collaborating early and at every stage of the product life cycle ensures that the product is designed correctly from the outset.
“This is high-value engineering and testing at its best, and can be documented in the bottom line.”
At TT Electronics, the team is focused on continuous collaboration with their customers to help them achieve their goals.