JLR Advances Green Manufacturing With Recycled Seat Foam
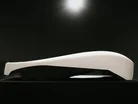
Jaguar Land Rover (JLR) is setting a precedent in the auto industry through its innovative use of recycled materials.
The British car manufacturer, in collaboration with Dow and Adient, pioneers the introduction of recycled seat foam into luxury vehicle production, fostering a circular economy in automotive manufacturing.
Recycling innovation
In a bid to address environmental concerns associated with vehicle production, JLR is focussing on innovative recycling technologies.
The company has established the JLR Circularity Lab located in Gaydon, England, which is dedicated to reducing emissions and waste while securing a stable supply of necessary resources.
A significant part of this initiative is the introduction of a "circular seat" made using recycled polyurethane foam, which is set to undergo testing in 2025.
So, what exactly is seat foam? It's a derivative of polyurethane, a polymer that's linked by carbamate bonds, forming a versatile but durable material widely used in various applications including vehicle seats.
However, due to its longevity and resilience, polyurethane is hard to break down, typically ending up in landfill sites and persisting in the environment for many years.
The recycled variant of this foam used in JLR’s circular seat is estimated to reduce associated CO2 emissions by half, preserving performance and curtailing more than 44kg of CO2 emissions per seat.
When put into perspective, this saving is equivalent to the amount of CO2 it takes to charge nearly three thousand smartphones.
Circular manufacturing collaboration
The undertaking is a collaborative effort with partners Dow and Adient, combining expertise from JLR’s Circularity Lab and the innovative materials developed under Dow’s MobilityScience platforms.
Notably, this is the first instance where recycled seat foam is utilised in a closed-loop system within vehicle production.
An examination of front bumpers using reduced polymer amounts hinted at promising results, with potential CO2 savings of 177,500 kg per model line and considerable cost reductions.
This initiative sets the stage for introducing eco-friendlier bumpers in new cars starting from 2025, directly contributing to lower overall vehicle emissions.
The venture is a part of JLR’s broader goal to produce vehicles that are not only luxurious but also environmentally responsible.
"This collaboration highlights Dow's MobilityScience initiative to drive sustainable mobility through advanced material science," says Don Penrice, Mobility President at Dow.
"By leveraging our expertise and collaborating with Adient and JLR, we are developing technologies that support our net-zero carbon emissions and our circular and renewable solutions goals.
“Through Dow's RENUVA™ sustainability program, Dow addresses the growing demand for recycled materials by converting End of Life waste into new raw circular materials, helping our customers meet their recycled content targets.
"Through chemical and advanced recycling processes, this breakthrough depolymerisation closed-loop recycling solution meets the requirements and maintains the superior comfort and quality of JLR seats.”
Driving towards future sustainability
JLR’s ongoing research at the Circularity Lab underscores its commitment to enhancing the recyclability of their luxury vehicles.
In the past, vehicle design seldom considered the ease of disassembly and material separation at end-of-life, consisting mainly of mixed materials that are challenging to segregate or recycle.
The Circularity Lab employs a practical approach to disassembly, working in conjunction with material experts and suppliers to develop strategies that overcome these barriers.
“I am so excited about the potential of this way of working," says Andrea Debbane, Chief Sustainability Officer at JLR.
"It represents a collective commitment to doing things differently, challenging us to rethink our approach from all angles to find the solutions needed to design and build the cars of the future.”
“Close collaboration with experts from the recycling and materials science industries, with our supply chain partners and colleagues from design and engineering is key – we need to work as a collective value chain to unlock meaningful change at scale.
"The knowledge and applications found demonstrate that full circularity is feasible and as a business this is critical to our transition.”
This proactive approach ensures that valuable materials such as glass, steel, aluminium and polymers can be reintegrated into the supply chain, underpinning the production of new vehicles without compromising quality.
JLR’s prior success in closed-loop recycling initiatives, such as the reuse of post-industrial waste aluminium from body panel stamps, bolsters their sustainability efforts.
Each project adds a new layer of understanding and capability, paving the way for future innovations that might see JLR setting new standards not only within its market segment but across the broader automotive industry.
The work done by the Circularity Lab reinforces not only JLR’s sustainability goals but also its aspiration to redefine corporate responsibility and community engagement within a circular economic framework.
“At Adient, we are proud to lead the change in integrating closed-loop recycled materials into our seating solutions," says Mick Flanagan, Vice President Customer Group at Adient.
"Our collaboration with JLR and Dow not only showcases our commitment to sustainability but also demonstrates how innovative partnerships can drive significant advancements in the automotive industry.
"By leveraging recycled polyurethane, we are setting new benchmarks for environmental responsibility while ensuring our products deliver the luxury and comfort our customers expect.”
Explore the latest edition of Manufacturing Digital and be part of the conversation at our global conference series, Manufacturing LIVE.
Discover all our upcoming events and secure your tickets today.
Manufacturing Digital is a BizClik brand.