A Look Inside The Innovative Manufacturing Technology Centre
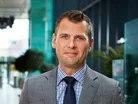
With over 25 years of experience in research and development, Joe Darlington is the Director of Engineering at the Manufacturing Technology Centre (MTC).
He collaborates with the automotive, power & energy, and defence industries, focusing on enhancing productivity and mitigating investment risks through innovative digital engineering technologies.
Joe joined MTC 13 years ago as part of its digital engineering capability.
Over the years, he has gained diverse experience, ranging from virtual manufacturing and manufacturing simulation to business transformation.
His remit now encompasses a wide range of engineering capabilities, including core technologies like additive manufacturing and laser technologies, as well as helping organisations achieve their business targets through change management programmes.
Prior to his time at the MTC Joe worked in research organisations and universities around the UK, collaborating with major manufacturers to encourage and facilitate technological advancement.
What has your career journey to the Manufacturing Technology Centre (MTC) taught you about the manufacturing industry? What broader changes and trends have arisen?
My background is in applied R&D, having spent the past 25 years working in research and technology organisations embedded within industry. As a result, my passion is industrial transformation through technological advancements.
During that time, I’ve worked in various research organisations and universities around the UK, both working with a UK and international client base on technology adoption.
My work has predominantly focused on the digital side of things, helping clients and organisations understand how to leverage technology in various settings. This involves not only transforming the way they develop processes and products but also enabling better decision-making earlier in the design and development stages.
Typically, this blends the commercial aspects of technological advancement with the specific innovations that the technology itself brings. For example, in additive manufacturing, this could mean making a component lighter, more robust, or improving its thermal performance.
During my time in R&D, I worked with major manufacturers like Ford and Rolls-Royce and in the supply chain during my time at Warwick Manufacturing Group.
This experience exposed me to a completely different part of the supply chain spectrum, going from developing multi-million-pound long-term strategies for product processes to addressing shorter-term challenges with limited technical resources.
These two ‘apprenticeships,’ as I like to call them, in distinct areas of the supply chain allowed me to view the process through two very different lenses, giving me a more rounded insight into the overall, integrated supply chain.
Can you tell me about the history of MTC?
Located in Coventry, the Manufacturing Technology Centre (MTC) is a leading UK applied research organisation.
It plays a vital role in industrial transformation by focusing on future manufacturing technologies and transferring research findings to industry, thereby strengthening the UK’s industrial base.
Established in 2010, the MTC operates three sites across the UK and employs nearly 1,000 people, consisting of a blend of industrialists and engineers.
The centre bridges the gap between academia and industry, having been founded by Loughborough University, The University of Birmingham, and The University of Nottingham.
MTC is also part of The High Value Manufacturing (HVM) Catapult, forming part of a broader network designed to bridge the gap between academia and industry, facilitating the commercialisation of innovative technologies.
Can you tell me about what you're currently working on at MTC?
My current remit spans our overall engineering portfolio, covering a broad spectrum of capabilities from more core, advance process technologies such as additive manufacturing and laser technologies through to enabling adoption and change management of these innovations, to enhance our UK industry’s ways of operating.
As part of these change management capabilities, we look at issues such as how technology can be successfully landed and implemented within an organisation as well as how industry standards can be applied to help organisations accelerate the industrialisation of their discreet processes and products.
In more recent years, as the organisation has grown, I’ve led internal change programmes to ensure that our technology investments are long-term and impactful.
Over the past three-four years in particular, my scope has expanded across our entire engineering footprint to look at those more disruptive process technologies I mentioned.
Much of the work here is around accelerating new processes and consequently rethinking product design to leverage these new capabilities. When an organisation wants to adopt a technology, we assist them in developing the change process to facilitate this transition.
As we embrace Industry 4.0, what does successful technological implementation look like for manufacturers?
To me, successful implementation of technology stems from encouraging the industry to ask - what can digital mean for you?
A good example of this is Project Convergence. Project Convergence is a £14 million, three-year collaborative R&D project led by Moog Aircraft Segment, a market leader in servo-valves used to control various aspects of aircraft, such as engines, braking, steering and utility controls.
Moog wanted to protect and enhance its position within the global aviation market via two key initiatives.
Firstly, by building a new, consolidated factory site in Tewkesbury, more than doubling its current footprint in the region and secondly, via Project Convergence. The project runs parallel to the new factory build and will deliver innovations in digitised manufacturing, developing new processes, improving productivity and implementing state‐of‐the‐art production testing technologies.
Through implementing cutting-edge digital technologies and practices within these elements, Moog is creating a more efficient, connected and intelligent manufacturing process, securing a competitive edge.
While this is an example of what successful integration looks like, there are scenarios where you’ll see an industry buy into a disruptive technology too early, when it isn’t well understood enough, and this causes implementation to be tricky or ineffective.
Long-term deployment is where we tend to see the real challenges of technology implementation within Industry 4.0, so it’s critical to think about what the long-term return is.
A lot of time and consideration needs to be put into the front end of the process design, including concise definitions of the problem that the technology aims to address, and the specific needs that a product or system must meet to be successful. These need to be crystal clear before a process can be developed and successfully adopted within an organisation.
AI. What are your predictions, for manufacturing, business and beyond?
One future scenario for manufacturing may be full transparency and connectivity across the supply chain.
This would enable organisations to resource efficiently and have oversight of the process from start to finish. While this might seem like a logical progression, it presents significant technical and commercial challenges to unlock potential new business models.
There are many elements to consider, none less so than security issues such as data breaches and cyber-attacks, so the infrastructure must be exceptionally robust.
Another opportunity which has the potential to be really exciting over the next coming years is the potential for AI to unlock knowledge-based engineering.
Organisations are rich with intelligence and insights to combine these up and downstream critically at the point of need.
Traditionally, this information would be scattered across numerous documents, datasets and subject matter experts, but with this technology, it could be systemized into an intelligent digital assistant for engineers.
These tools will provide enhancements into new critical design considerations such as sustainability and circularity to help navigate those competing design constraints. It’s all about improving the quality of the decision-making process.
AI is new technological territory, coming with risks and responsibilities. What do you think these are, and what role does governance play in mitigating them?
Looking beyond manufacturing, AI is set to impact virtually every industry. Over the past 18 months, as AI has gained more public attention, our understanding of its potential has evolved dramatically.
As a result, managing and regulating AI will be a significant task moving forward. Like many technologies, the promise and practical application of AI must be developed alongside ethical and regulated frameworks.
A key component of these frameworks will be building trust and confidence in the AI process. This requires clear oversight and understanding of how AI models arrive at their outcomes.
Data biases significantly impact the final output, and in the coming years, much work will be needed to understand and control these. Another key factor here will be ensuring trust in the security of AI models and systems. Without these factors, AI cannot be safely, and effectively enhanced to its full potential across sectors.
Industry 5.0 is on the horizon- what benefits is it set to bring to broader society?
From my perspective, the transition from Industry 4.0 to Industry 5.0 will be a natural progression, with Industry 4.0 serving as a stepping stone towards greater human integration and connectivity with AI.
This is where we are likely to see knowledge-based engineering come into play, with AI augmenting decision-making through intelligent digital assistants. There is still a lot of work to be done before Industry 5.0 is a reality, but it has a lot of really exciting potential for real-world applications.
******
Make sure you check out the latest edition of Manufacturing Digital and also sign up to our global conference series - Procurement & Supply Chain 2024 & Sustainability LIVE 2024
******
Manufacturing Digital is a BizClik brand.