Roadmapping IoT Success with Legacy Manufacturing Equipment
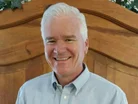
Smart machines can provide manufacturers with invaluable real-time insights into shop floor productivity, inventory, and potential quality and maintenance issues.
But buying new machinery to harness the Internet of Things (IoT) can be hard to justify, especially when interest rates remain high.
An effective option to IoT success is to add sensors to existing equipment and start capturing real-time data at a fraction of the cost.
Lynn Loughmiller, Software Engineering Manager at DELMIAWorks, Dassault Systèmes takes a closer look at how IoT can be an effective tool when working with existing equipment, and looking at just how efficient it may be.
What are the different types of sensors?
Available sensors support different types of data collection that enable manufacturers to track metrics related to productivity, consumption, wear, and other factors.
Here are five commonly used sensors.
- A proximity sensor is used for counting. One sensor may capture each part produced. Another may track the feet of material going into the machine. Comparing those two measures can help to understand scrap and percentage of loss.
- Amperage and pressure sensors work similarly. Amperage sensors can measure machine speed and force of tooling. Pressure sensors capture similar information for hydraulic-based machines. Having a standard base of amperages and pressures for each part can determine proper setup, tooling expectations, and machine norms. Meanwhile, variations from base measurements can indicate issues affecting part quality or equipment maintenance.
- A vibration sensor measures the amount and frequency of vibration in a machine or equipment. Those measurements can help detect imbalances and other issues to predict maintenance needs. Additionally, a vibration base measurement can provide a machine signature for good parts and a healthy machine.
- A flow meter can be added to a device to track whether it is applying the necessary amount of lubricant to the material, which can impact product quality.
How is sensor data captured in software?
Data from sensors is captured by a programmable logic controller (PLC) or a data logger. The device can then convert the data to a usable computer format and make it accessible to the shop floor network.
Newer smart IoT sensors can be made directly available to the shop floor network without intermediary devices. Once accessible to the network, the information is usually sent to a server that supports the Open Platform Communications (OPC) standard for industrial communications.
The OPC or other software may be needed to calibrate the data to match a machine’s own values.
From there, the information can be fed into a manufacturer’s enterprise resource planning (ERP) and/or manufacturing execution system (MES) software to populate various real-time reports with the data.
Both current and historical data are maintained in the software, making it possible to analyse this information from the perspective of quality, efficiency and other key metrics.
What do manufacturers do with captured software data?
Manufacturers typically use data captured by the software to:
- Collect information for end-of-shift reporting to help determine if the material is equal to the number of parts that the team anticipates producing.
- Track counts in a work centre to assist in production planning.
- Match the work order to what’s running in the machine to update inventory consumption.
- Compare how many cycles have been completed versus parts made to understand the scrap being produced.
- Determine downtimes for each work centre.
- Look for out-of-limit processes for quality control.
What is the most powerful use of sensors in manufacturing?
The most powerful use of sensors comes from combining the real-time data they generate with real-time production and process monitoring functionality that is integrated with the MES and ERP systems.
Real-time production monitoring helps bring meaning to the counts from sensors by capturing production cycles that can take mere milliseconds and displaying averages, such as X amount of product per minute. Counts in ERP and MES software also support automated workflows, such as materials orders, inventory updates, production scheduling, and other shop floor and accounting processes.
When combined with statistical analysis, real-time production and process monitoring can help establish parameters for performance, wear, etc., as well as track and flag when production cycles and processes measured by machine sensors head outside an acceptable range. The data can be used by an MES for scheduling production, ensuring quality, and performing preventative maintenance, among other processes.
The metrics or key performance indicators (KPIs) tracked will be specific to each manufacturer’s priorities. But starting with too many KPIs can ground monitoring and analysis initiatives to a halt—defocusing efforts while consuming valuable staff time. So, management should prioritise creating a short list of KPIs most relevant to the business. Once the company is regularly tracking metrics against these KPIs, new KPIs can be added.
How can manufacturers get started on their journey to IoT success?
To get started, the most successful manufacturers get sensors and monitoring working on one machine and begin collecting the sample information everyone agrees is important to that machine. Once the data coming in looks the way the team wants it to, the approach can be applied incrementally to other machinery.
It’s better to start with a machine where the team understands how the interface works and can be successful. Even if getting up and running is easy, the team will still learn things through the process, and that knowledge will help with the rest of the installation and give everyone confidence that the results are going to be as expected.
Manufacturers also should first hook up sensors and monitoring to a well-performing machine from which the team can collect data and create a baseline of understanding. This will serve as a springboard against which to measure other machines. And, when first monitoring the data from sensors, it’s important to note that sensors placed on different parts of a machine will often produce different results—even if the type of sensor is the same.
Additionally, there are physical implementation factors to consider. Many successful manufacturers have relied on their in-house maintenance teams for the install instead of using outside electricians, since the installers need to be familiar with their equipment, machines and the building.
Also, because the amount of metal on shop floors can leave WiFi and wireless devices unreliable, consider using wired connections to each machine rather than wireless ones. Finally, plan for the future by having network drops on every machine. This will ensure that all machines have network capacity as the team expands the installation of sensors across the shop floor and begins to collect data.
By following these best practices for bringing sensors and real-time monitoring to existing machinery, manufacturers can quickly gain insights to improve their efficiency and correct issues that have been losing money. And longer term, this can translate into greater efficiency, productivity and profitability.
Make sure you check out the latest edition of Manufacturing Digital and also sign up to our global conference series - Manufacturing & Mobility LIVE
Manufacturing Digital is a BizClik brand