Six AI Manufacturing Lighthouses to Take Notice of, pt 1
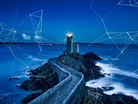
AI's impact on manufacturing can be felt and seen across operations.
From enhancing quality control to driving cost savings to reducing emissions to optimising production lines, AI is making the factory floor a smarter and more efficient place.
Nowhere is this more evident than with the manufacturers who are a part of the World Economic Forum's Global Lighthouse Network.
Cofounded with McKinsey, this pioneering initiative examines how Industry 4.0 technologies like AI are shaping the future of manufacturing operations.
Recently welcoming 22 new members, the Global Lighthouse Network is home to the trailblazing manufacturers who have embraced digital transformation to drive profound operational improvements and efficiency.
Their advanced sites set new standards for technological integration, productivity, sustainability and workforce development, enhancing human-machine collaboration.
Six manufacturing leaders whose sites were recognised by the Global Lighthouse initiative sat down with the World Economic Forum to expand on their use of AI.
Their insights demonstrate the holistic impact AI can have on operations, fundamentally transforming the factory itself.
Here's what the first three had to say.
Stephan Schlauss, Global Head of Manufacturing, Siemens AG
Siemens is undoubtedly one of the most technologically agile and trailblazing manufacturers.
Across its vast operations, the company widely adopts Industry 4.0 technologies as part of its strategy to create and build its Industrial Metaverse.
"At Siemens, we experience AI's transformative impact on manufacturing daily, boosting productivity, efficiency and sustainability," Stephan says.
"With rising labour costs, skill shortages and a need for eco-friendly solutions, AI is a crucial part of our vision for the industrial metaverse."
Manufacturing Digital recently reported on how Siemens's Electronics factory in Erlangen had been recognised as a Digital Lighthouse.
The third Siemens site to be recognised by the WEF, this award came after Siemens announced a staggering €500m (US$549.45m) in research and infrastructure in Erlangen, intending for the hub to drive development and research for the industrial metaverse.
We covered how Siemens Green Lean Digital approach was essential to this, an approach which was shaped by their strategy towards AI.
"AI applications deliver remarkable results across our entire value stream at Siemens Electronics Factory Erlangen. For example, machine learning optimises testing procedures, significantly increasing first-pass yield and boosting efficiency," adds Stephan.
"AI-enabled robots that pick and place different parts and materials in our fully automated assembly lines reduce automation costs by 90%. Manual workers are also empowered with AI-guided systems, enhancing productivity and quality. Our industrial-grade AI infrastructure, built on Siemens hardware and software, simplifies adoption and reduces change management."
Stephan also describes AI as having a positive impact on the workforce, enhancing training and learning as the industry struggles with a hiring and retention gap.
"Automated training and deployment pipelines minimise the efforts for updates, while continuous automated monitoring ensures reliability and trust in AI algorithms," he concludes.
"This enhances scalability, lowers adoption barriers and fosters trust."
Nihat Bayiz, Chief Production and Technology Officer, Beko
Beko is another global manufacturer recognised by the WEF for its pioneering utilisation of Industry 4.0 technologies.
Nihat Bayiz, Chief Production and Technology Officer at the company explained how AI adoption has profoundly enhanced Beko's manufacturing operations.
"Through the integration of AI-driven innovations, we have not only optimised our manufacturing processes and design but also empowered our workforce," Nihat says.
"Key AI applications include a smart machine learning powered control system that adjusts parameters in real time, reducing scrap and preventing defects in sheet metal forming, resulting in a 12.5% material cost savings.
"A decision tree-based model prevents clinching failures from variations in sheet thickness, cutting defect rates by 66%. and a closed-loop valve gate control using convolutional neural network algorithms optimises plastic injection, analysing over 150K data points and improving cycle time by 18%."
Beko's Ankara Dishwasher plant has been recognised as a key case study in the WEF Global Lighthouse Network. The plant's integration of over 35 in-house solutions with its IoT platform FLOW led to a myriad of quantifiable improvements.
These included a 46% reduction in time-to-market, a 29.2% drop in field failure rates and a 26.1% decrease in conversion costs.
AI is delivering Beko similar impressive results, according to Nihat.
"Advanced machine learning algorithms in cleaning cycle design reduced time to market by 46% and achieved 99% optimisation in cleaning performance," he says, noting the positive impact AI has had on the workforce at Beko as well.
"Training programmes covering basic AI principles to advanced machine learning applications have led to 3,160 training hours completed in six months.
"A global automation programme guides factory-scale adoption and use-case sharing, governed by central and local digital transformation offices, with plans to establish a lighthouse factory for each product group."
Anand Laxshmivarahan. R, Chief Digital and Information Officer, Jubilant Bhartia Group
Jubilant Bhartia Group, the Indian conglomerate with operations spanning manufacturing, pharmaceuticals, food, agribusiness and energy was recognised by the WEF Global Lighthouse Network earlier this year for its Ingrevia facility.
Dedicated to speciality chemical manufacturing, the facility based in Gujarat has embraced 4.0 technologies, exhibiting more than 30 integrated use cases leveraging AI, predictive platforms and digital twins.
"At Jubilant Ingrevia, we’ve embraced AI and machine learning across all production stages to boost efficiency, reduce process variations and optimise yield and throughput," says Anand Laxshmivarahan. R, Chief Digital and Information Officer, Jubilant Bhartia Group
"We’ve widely deployed 'digital twins' – virtual replicas of critical assets – to model, forecast and manage operations in real time. Specific AI or machine learning models optimise production parameters, leveraging historical and current data to ensure quality and resource efficiency.
"Using insights from our Digital Performance Management model, we’ve reduced process variability by 63%."
According to Anand, Jubilant Bhartia Group have experienced significant improvements through AI adoption, specifically in the field of predictive maintenance.
"Our manufacturing units are equipped with internet of things-based monitoring systems with predictive analytics – superior AI algorithms to predict equipment failures before they occur. This approach has reduced downtime by more than 50%, enhancing our operational efficiency remarkably," he says.
"Soft sensors, powered by AI, enhance data collection and analysis, improving product quality and optimising process conditions. The AI-driven analytics system manages energy consumption, reducing operational costs and achieving a 20% cut in Scope 1 emissions, supporting sustainability goals."
By pursuing AI integration holistically across operations, the group has experienced profound benefits, with plans to increase use of the technology moving forward.
"Integrating AI throughout our production process enhanced automation and boosted operational efficiency, laying the groundwork for a more sustainable and environmentally friendly future," Anand says.
"Diving in headfirst across all 50 of our plants, we plan to deploy 10-12 use cases involving emerging technologies throughout our global operations this year and next.
"A key first step in doing so has been to ensure all our plants are connected and integrated with an Operational Data Lake to get a real-time and integrated view of data to help us deliver AI or machine learning-based interventions to improve the yield and throughput.
"Our JUMP (Jubilant Model Plant) serves as a digital lighthouse to perfect AI models before broader deployment, while our Digital Centre of Excellence drives this transformation with AI experts and Digital 101 training for all employees. Recognition is also key in this journey – our rewards programme nurtures digital champions while DigiScoop spreads success stories, helping scale innovation."
Anand believes that the group's adoption of AI will: "Redefine what's possible in chemical manufacturing."
AI has the potential to do the same across a diversity of manufacturing verticals, as trailblazers like Siemens, Beko and the Jubilant Bhartia Group demonstrate.
Click here for part 2 of this two part series.
Make sure you check out the latest edition of Manufacturing Digital and also sign up to our global conference series - Manufacturing & Mobility LIVE
Manufacturing Digital is a BizClik brand
- Siemens & Tietoevry: Driving Nordic Grid ElectrificationDigital Factory
- Cyber Monday Pushes Greater Manufacturing SustainabilityProcurement & Supply Chain
- Thomas Broadbent & Siemens: Retrofitting With Digital TwinsDigital Factory
- Top 10: Manufacturing Accomplishments of 2024Procurement & Supply Chain