How Smart Factories are Reshaping the Manufacturing Sector
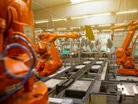
There is an ongoing wave of manufacturing innovation. Since COVID-19, which saw rapid investment in and implementation of automation and AI technologies, smart factories have grown increasingly prevalent.
They’ve enhanced productivity, efficiency and results across the manufacturing sector and beyond.
However they still pose marked challenges to companies, in terms of safety, costs and effective management. A solution to this may be developing a maturity framework that accounts for people, processes and modular technology.
The benefits and challenges smart factories pose to supply chain manufacturing
56% of manufacturers have invested US$100M or more towards smart factories, with Tesla, Samsung, HP, BMW and more all embracing them. Driving this decision are the significant benefits of smart factories, which enhance product quality, sustainability and decrease overall costs.
However these companies - and almost all companies experimenting with smart factories - have had to embrace a large-scale, systematic transformation. One which entails prominent costs and can be highly problematic.
Ideally, smart factories should be a holistic fusion between human and industrial labour, effortlessly integrating industrial robots, automated systems, sensor networks and AI enhancement with the existing workforce. Smart factory implementation should be treated as a spectrum, not as a one-fits-all solution. Each company, industry and individual factory floor requires its own distinctive blend of automation. Determining where companies fall on this spectrum is revealed when they implement a tailored maturity framework.
A maturity framework for smart supply chain manufacturing
A maturity framework balances human centricity, resilience and sustainability - helping companies establish how smart factories can help them and the human beings they employ. In a study of major manufacturing firms, the journal of Research-Technology Management identified the three key aspects of a successful maturity framework. People, process and technology.
03: Introduce Agile processes
The traditional stage-gate model for developing and implementing innovations will not keep up with the pace of technological change according to the report. Introducing agile processes will remedy this, providing much-needed autonomy and flexibility in smart factory implementation. Key to this is a continuous evaluation cycle that provides opportunities to improve product processes, redirecting focus as new technology and opportunities emerge.
02: Cultivate digital people
The entire workforce needs to evolve as digital transformation occurs. The manufacturing industry must address the existing skills gap in employees with effective recruitment, training and development. As workforce demands move from manual skill to digital competencies, managers must focus on empowering people with digital skills and helping to develop members of the workforce who don’t.
01: Configure Modular technology
The digital systems required to manage a factory are highly complex, breeding frustration and confusion with its endless choices. Diving technological solutions into modules and delivering each one step by step is the solution, helping employee training and constructing a mobile solutions architecture. By configuring modular technology teams can work more autonomously and technologies can be updated to support new functionalities over time, allowing for continuous innovation and new opportunities.
Ultimately, smart factories offer the opportunity to enhance productivity and efficiency, but will only succeed in supply chain manufacturing if they account for human-involvement and rapid change.
Guy Courtin, Vice President of Industry and Advanced Technology at Tecsys Inc, says: “Being able to run a factory 24/7 with [limited] labour and high efficiencies – that’s really the holy grail of manufacturing. You can definitely understand the interest,”
“What isn’t often talked about is the relationship with labour…There’s a certain uneasiness in introducing automation in that respect. It’s a delicate line to walk.” Many companies, with careful planning and analysis, are walking that line. Maturity frameworks could be key to doing it.
******
Make sure you check out the latest edition of Manufacturing Digital and also sign up to our global conference series - Procurement & Supply Chain 2024 & Sustainability LIVE 2024
******
Manufacturing Digital is a BizClik brand.