Stratasys’ 3D printing journey & the impact on healthcare
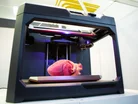
Stratasys has pioneered 3D printing for more than three decades, from its headquarters in Rehovot, Israel. It is a fast and efficient technology which, when combined with, for example, automation and robotics, can transform manufacturing production.
Erez Ben-Zvi is the Vice President for Medical at Stratasys.
“My key responsibilities include overseeing and managing all of the activities within the medical business unit,” he says. “This includes the formulation and execution of our strategic initiatives, as well as the careful monitoring of our profit and loss statement.”
Ben-Zvi has always had a passion for the medical field, helping others and doing something with an impact on others lives.
“My journey started in the third year of my studies, when I joined a startup company that developed image processing software for real-time analysis and navigation of cardiovascular interventional procedures to lead the quality management and regulatory affairs field.”
The role and the nature of a startup company exposed Ben-Zvi to the fundamental pillars of the medical device environment, product development life cycle process and interaction with regulatory bodies and key industry leaders.
“Being part of the development and introduction to the market of life-saving products that assist surgeons in performing better and influence the way patient care is given worldwide motivated me and has driven my ‘Why?’ ever since.”
In the following years, Ben-Zvi specialised in product management from inception to commercialisation and worked in senior roles, including as Head of Global Market Development for 3D printing proof of concept solutions, designing the go-to-market strategy and leading the product sales and growth.
3D printing for surgical planning and patient education
The healthcare sector is a field in which innovation and new technologies have a direct
impact on improving processes, operation results and saving lives. Ben-Zvi sees that there are many ways in which 3D printing is being used in this space, notably for:
- The production of highly-accurate patient-specific anatomic models and surgical guides
- For preoperative surgical planning
- Diagnostic use
- Accurate guide and placement of tools.
“A multi-colour, multi-material 3D print of a patient’s kidney can be produced to scale, showing the exact placement of a tumour and allowing for the design of anatomy-matched surgical guides,” said Ben-Zvi. “This allows surgeons a better view and planning prior to the operation followed by precise and safe guidance of surgery tools such as drillers and saws during the surgery.
“These help surgeons reduce potential risks and complications, save procedure time and help perform precise and successful kidney-sparing surgery, improving patient outcomes.”
Models can also be made for the purposes of patient education by bridging communication between doctors and their patients and even between the medical staff itself.
“Doctors often face difficulties in explaining to patients their clinical condition and the
reason for their decision to operate,” he says. “Having a tangible replica of a patient’s exact anatomy may assist doctors in bridging the clinical and anatomy knowledge gap of the patients and their families, reducing anxiety and confusion.”
For the medical staff, these patient anatomy replicas may assist with imaging interpretation and having the entire medical team speak the same language. Another use of models is for clinical training.
“We have developed materials which are able to accurately mimic human tissue and bone, and our PolyJet-based multi-material, multi-colour 3D printers are capable of creating these in one piece,” said Ben-Zvi.
This can minimise the use of cadavers, with replacements at a fraction of the cost of traditional manufacturing methods. Additionally, medical device manufacturers can use these realistic models to validate device performance and accelerate product development.
However, developments in materials and machines have enabled healthcare applications to go far beyond creating models.
“On the materials side, we have developed biocompatible and sterilisable materials, which open up a new range of applications.”
Stratasys has forged partnerships with relevant companies, whose technology proposition provides the right fit for the company to continue to meet its customers’ needs.
“One recent example that underscores this, is our partnership with CollPlant Biotechnologies. This pioneering regenerative and aesthetics medicine company develops innovative technologies and products based on its plant-based collagen for tissue regeneration and organ manufacturing,” said Ben-Zvi.
Through this partnership, Stratasys uses its P3 printing platform to support the development of a bio-fabricated breast implant solution, using Collplant’s plant-based collagen.
“This started with a regenerative breast implants programme, however we believe that there will be other exciting developments further down the line.”
Stratasys' vision for the future of 3D printing across industries
Despite the longstanding presence of 3D printing in healthcare, there’s a knowledge gap among many practitioners, complicating funding justification as well as the cross-industry challenge of shifting to production using 3D printing.
“To address this, 3D printing companies like Stratasys are increasingly focusing on education and market awareness alongside the improvement of printing platforms and materials to address new applications while meeting strict medical regulatory standards. The education effort is vital not only for securing funding and industry growth, but also for training the surgeons of tomorrow on everyday application use.”
Stratasys plans to continue to ensure greater sophistication in the 3D printing technologies themselves. However, much like any industry, much of the progress will be down to ongoing advances in materials.
“This is essential to open up new applications, and through our recent acquisition of Covestro’s materials business, we’re now in an even better place to deliver exciting new materials for the medical market, alongside the other industries we work in.”
“The future of 3D printing is promising, not just for the medical industry, but far beyond this too. Not only does it allow for decentralisation of production to overcome supply chain disruptions and optimise time-to-market, it also enables the production of parts in batch quantities as low as one.”
Recent technological advancements, including those around Selective Absorption Fusion Technology, have made it cost-effective to 3D print parts in much larger quantities than previously. This now means that manufacturers have the capability to 3D print tens of thousands of end-use parts with the level of control, accuracy, consistency expected from injection moulding.
“This, together with the technology’s agility and inherent time and cost-saving attributes will continue to make it the technology of choice for many processes throughout various industries.”
Regarding Stratasys, its focuses will centre on continuing to advance the materials it offers, bolstering software capabilities and delivering comprehensive solutions to the various industries it caters to.
“While we persist in innovating 3D printing technology, our commitment to enhancing software and materials is equally vital, especially when it comes to enabling seamless digital workflows for critical applications in healthcare, automotive, aerospace, industrial manufacturing and beyond.”